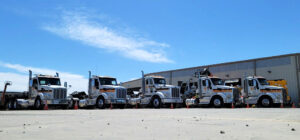
H&E opens new branch in the Myrtle Beach area
Effective June 17, 2024, H&E Rentals (H&E) has announced the opening of its Myrtle Beach branch, the fourth general rental
Effective June 17, 2024, H&E Rentals (H&E) has announced the opening of its Myrtle Beach branch, the fourth general rental
Jungheinrich, RAVAS EUROPE, SAFELOG with Mercedes, SSI Schäfer, and STILL have been announced as winners of the IFOY Award 2024.
On June 4th, JCB began work on a new $500 million factory in San Antonio, Texas – the biggest investment in the company’s
Yale Lift Truck Technologies announces a major milestone for its Yale Reliant™ operator assistance technology to mark the 11th edition
Bobcat Company is expanding its tractor lineup with the launch of three utility tractors: the Bobcat UT6066, UT6566, and UT6573. Bobcat
Conquer Your Equipment Dealership’s Sales with Powerful Strategies! Industry consultant George Keen has released his new paperback book to maximize
Catalano earns Gold Stevie for Best Business Influencer of the Year Toshiba America Business Solutions’ social media leader Robert Catalano
Toyota Material Handling is celebrating the 25th anniversary of its System of Active Stability™ (SAS), which revolutionized the material handling industry by reducing the
To demonstrate its support of National Forklift Safety Day, June 11, and its commitment to creating safe working environments, Hyundai
Helping to support safety initiatives in broader range of demanding material handling environments Hyster Company announced two major updates to
“Lift Your Standards by Lowering Your Load” Combilift has announced the launch of its new National Forklift Safety campaign, “Lift
Company officially breaks ground on new factory, which will be used for electric forklift production Toyota Material Handling, the North
Subsidiary of the esteemed Hangcha Group and its exclusive Québec dealer prepare for June event Hangcha Forklift Canada has announced
Innovative updates inspired by customer requests JLG® Industries, Inc. has introduced the all-new SkyTrak® 8042 telehandler, remastered to maintain the
Carolina Handling has been named the 2023 Top Performer of the Year by Modula, Inc., a manufacturer of vertical lift
New Age Industrial, a designer and manufacturer of aluminum storage and transport, has announced the retirement of Bob Brackle, National
Crown Equipment Corporation has announced the availability of the Crown SP 1500 Series order picker. The lift truck introduces innovative
Hy-Brid Lifts has announced Gary Coke as director of sales covering the south-central United States. Coke’s responsibilities include providing customer
H&E Rentals has announced the opening of its Jonesboro branch, the third general rental equipment location in the state of
Hyster-Yale Group (HYG), an integrated full-line lift truck manufacturer, has appointed ICON Equipment Solutions Philippines Inc. (ICON) as its official