H&E opens new branch in Conroe, Texas
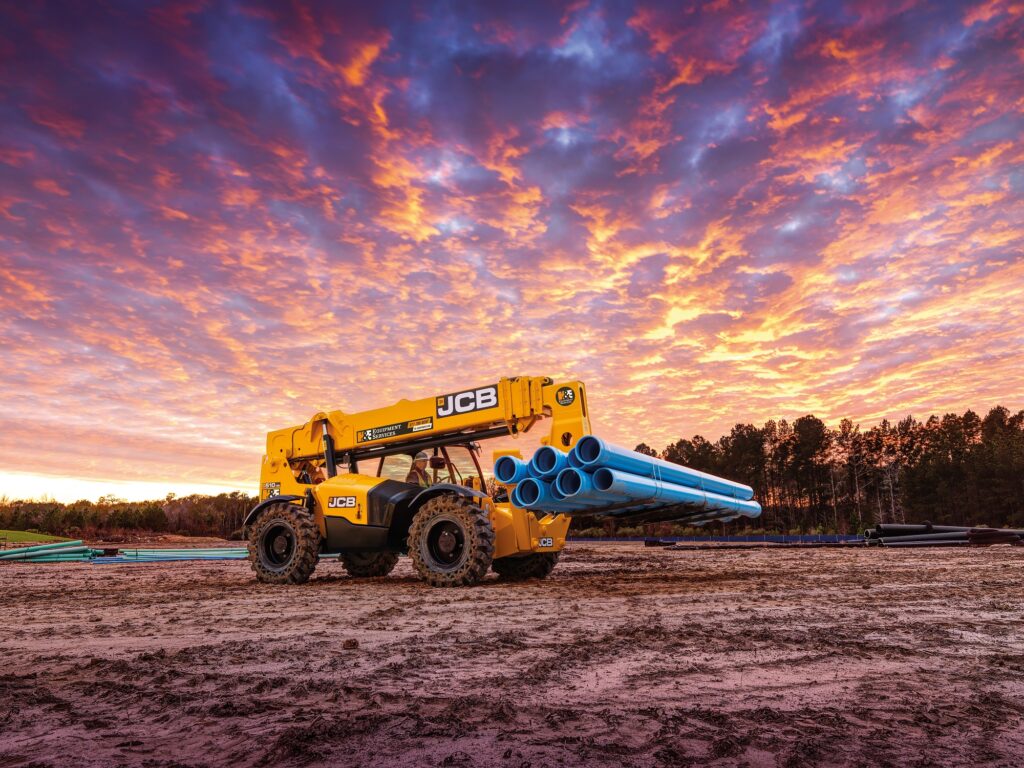
Effective November 13, 2023, H&E Equipment Services Inc. (H&E) announces the opening of its Conroe branch, its fifth rental location in the greater Houston market and the 25th in the state of Texas. Since the beginning of the second quarter of 2023, H&E has opened 14 new branches across the country, with four of those in the Lone Star State. The facility is located at 530 Frazier Commerce Drive, Conroe, TX 77303-5380, phone 936-286-3900. It includes a fully fenced yard area, offices, and a repair shop and carries a variety of construction and general industrial equipment. “The location of our Conroe branch gives H&E total coverage of the Houston area, especially the growing market north of the Woodlands. The new facility covers the territory between our Houston, Katy, and Bryan branches, so customers in outlying areas have more convenient service” says Branch Manager Tesha McGruder. “Our close proximity to I-45, state highways 105 and 75, and other major roadways is ideal for getting our new fleet to job sites quickly.” The Conroe branch specializes in the rental of aerial lifts, earthmoving equipment, telescopic forklifts, compaction equipment, generators, light towers, compressors, and more and represents the following manufacturers: Allmand, Atlas Copco, Bomag, Case, Club Car, Cushman, Doosan, Gehl, Generac Mobile, Genie, Hamm, Hilti, Husqvarna, JCB, JLG, John Deere, Kobelco, Kubota, LayMor, Ledwell, Lincoln Electric, Link-Belt Excavators, MEC, Miller, Multiquip, Polaris, Sany, Skyjack, SkyTrak, Sullair, Sullivan-Palatek, Tag, Towmaster, Unicarriers, Wacker Neuson, Yanmar, and others.
Hy-Brid Lifts announces Director of Sales for Southeast United States
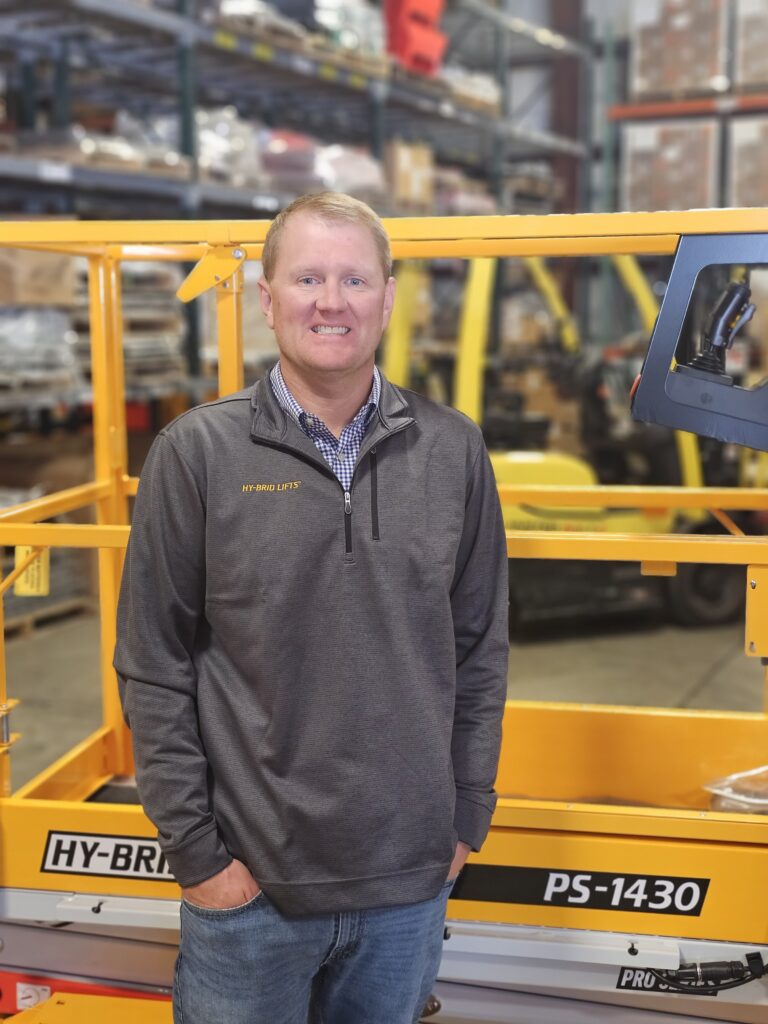
Hy-Brid Lifts announces David Price as director of sales covering the southeast United States. Price’s responsibilities include providing customer support as well as continuing the growth and channel development of the Hy-Brid Lifts line of low-level scissor lifts. “I am excited to join this team and look forward to the opportunity to work with our customers. Coming from the rental industry, I understand the importance of quality equipment and customer service backed by a solid service department,” said Price. “After touring the production facility and meeting the Hy-Brid Lifts family, it’s no surprise that this company is continuing to grow, and I look forward to being a part of that growth.” Price brings 12 years of industry experience to his new role, largely derived from his time in the rental equipment industry with United Rentals, Blueline Rentals and Equipmentshare. He spent a majority of his time in sales management with a strong emphasis on customer service and going above and beyond for every customer. “The entire Hy-Brid Lifts team is excited to have David on board to serve the southeast United States. David has a wealth of sales and rental industry knowledge that will strengthen our ability to serve our customers,” said Dave Wanta, Custom Equipment LLC vice president of sales. “David is a valuable addition to the team, and we look forward to the contributions that he will provide for our company’s continued growth.”
Hyster-Yale Group recognizes National STEM Day with manufacturing engineering and innovation programs
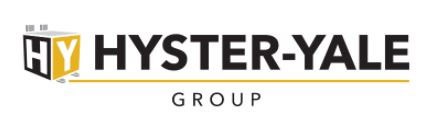
Major manufacturer of forklifts and related technologies collaborates with non-profit, universities across the country to foster opportunity and innovation among students pursuing careers in engineering Coinciding with National STEM Day, Hyster-Yale Group announces several milestones and opportunities for engineering students through its longstanding collaborations with academic and career development programs from coast to coast. The company is sponsoring dozens of senior capstone projects, providing mentorship and internship opportunities, opening a new innovation lab and lending industry perspective to new university engineering programs. Innovation Lab at the University of Portland The Hyster-Yale Group Innovation Lab will resume in January 2024 at the new Shiley-Marcos Center for Design and Innovation at the University of Portland. The lab was paused due to the COVID-19 pandemic and construction of the new facility. The lab, which has been a model for other industry-university cooperation, immerses student interns in real engineering and product development projects. Four interns have already been hired into development and innovation roles with the company. The lab is led by Chief Technologist of Innovation for Hyster-Yale Group, Ed Stilwell, who created and taught an innovation course for several years at the university. Internships and advisory councils The company works with other colleges in the communities where it operates to provide internship opportunities, including East Carolina University, Berea College, Eastern Kentucky University and the University of Kentucky. Hyster-Yale Group also serves alongside companies such as Lockheed Martin and Lexmark on the Eastern Kentucky University engineering advisory council. Anthony Wasson, Value Stream Manager, and Ken Deters, Director of Service Operations, are active on the council, which was established to provide industry perspective to the development and operation of the school’s new degree program in manufacturing engineering. At East Carolina University, the Warranty and Quality Improvement Manager for Hyster-Yale Group, John Roberson, also serves on an engineering advisory council. Hyster-Yale Group’s Counterbalanced Development Center (CBDC) in Oregon is in the planning process for 2024 internships with the Multiple Engineering Co-Operative Program (MECOP), a non-profit that works with member companies and universities in the Pacific Northwest to cultivate the highest level of engineering and business graduates by bridging academic theory with industry reality. Since 2000, more than 95 interns across mechanical, electrical, computer engineering and computer science disciplines have worked at the CBDC supporting various product development projects. At least 15 former MECOP interns are employed across the development team, working in design, validation, program management, software and simulation or virtual testing. Hyster-Yale Group posts internship opportunities for fall, spring and summer semesters at several locations. To learn more about all available internship opportunities or to apply, visit https://hyster-yalecareers.com/. University capstone projects Each year, the CBDC sponsors capstone projects for 35 to 40 seniors from local universities. The students work in teams on eight to 10 real-world and often multi-discipline engineering problems provided by Hyster-Yale Group. In Greenville, North Carolina, the company’s Warehouse Product Development Center and manufacturing facility also host engineering students from East Carolina University completing their capstone projects. In both cases, students are guided through the process of developing viable solutions by mentors from the company, accessing valuable experience and insight to the field and developing relationships in the industry as they progress. Student teams have created specialized test equipment, innovative human-machine interfaces, improvements to forklift operator comfort, new sensing methods and other innovations at the leading edge of the materials handling industry.
Bobcat expands in new facility in Monterrey, Mexico
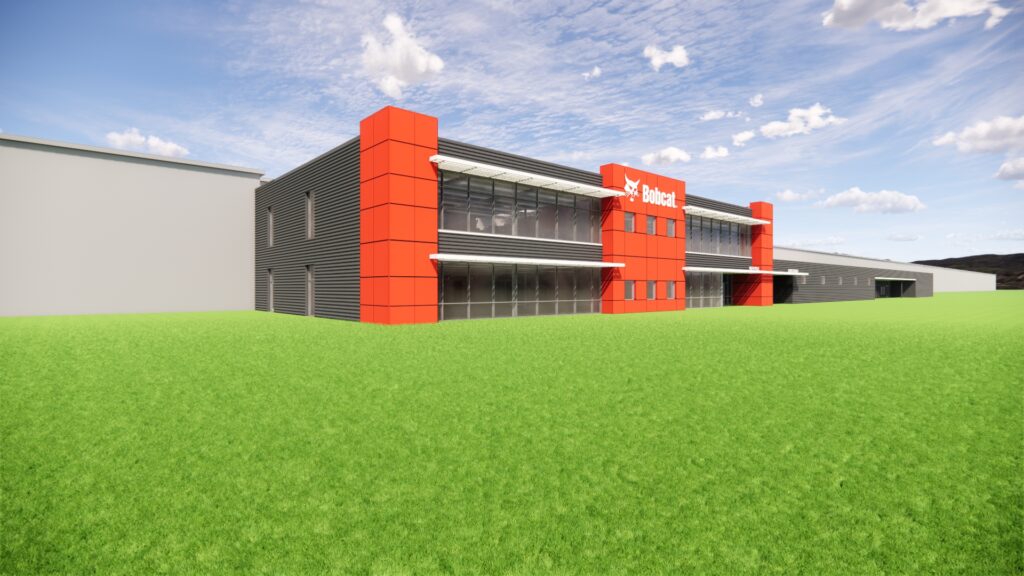
$300 million investment aims to boost production capacity to support customer demand and company growth Bobcat Company has announced their intentions to expand its footprint with a new manufacturing facility in Monterrey, Mexico, anticipated to begin production in early 2026. The investment, planned for approximately $300 million, will expand Bobcat’s existing global footprint to create additional production capacity and manufacturing capabilities for select compact track and skid-steer loader models. The new facility is expected to create an additional 600 to 800 jobs in the region. “As a global company with manufacturing facilities, offices, dealerships and customers across the globe, we have seen tremendous growth and increased demand for our products,” said Scott Park, Doosan Bobcat CEO and vice chairman. “We are excited to continue growing our footprint to meet demand for Bobcat solutions worldwide.” The 700,000-square-foot manufacturing facility is expected to increase Bobcat’s North American compact loader production capacity by 20%. The facility will feature areas for welding, painting and assembly, as well as an on-site warehouse and office space. Bobcat will implement state-of-the-art technology with an emphasis on quality, precision and energy efficiency. The Monterrey location will manufacture Bobcat M-Series compact loaders for North American distribution. This strategic manufacturing capacity alignment will allow Bobcat to focus its industry-leading R-Series compact loader production at its Gwinner, N.D. facility, and its Dobris, Czech Republic facility will continue to manufacture M-Series loaders for the Europe, Middle East and Africa regions. Bobcat will continue to focus on talent retention and hiring at all locations in support of continued expansion and growth. “This new facility allows us to design a manufacturing space for maximum efficiency, quality and production output,” said Mike Ballweber, Doosan Bobcat North America president. “By growing our manufacturing footprint, we can also further optimize our other global facilities to improve our operational efficiency and enhance employees’ workspaces.” This new location was selected after extensive review and consideration of expansions at existing Bobcat locations, along with the potential for new developments at locations across the globe. Monterrey was selected for its well-established industrial sector, skilled workforce, proximity to the U.S., cost competitiveness and strong business environment, among other factors.
Hyster recognized by Fast Company for world’s first hydrogen-powered top-pick container handler
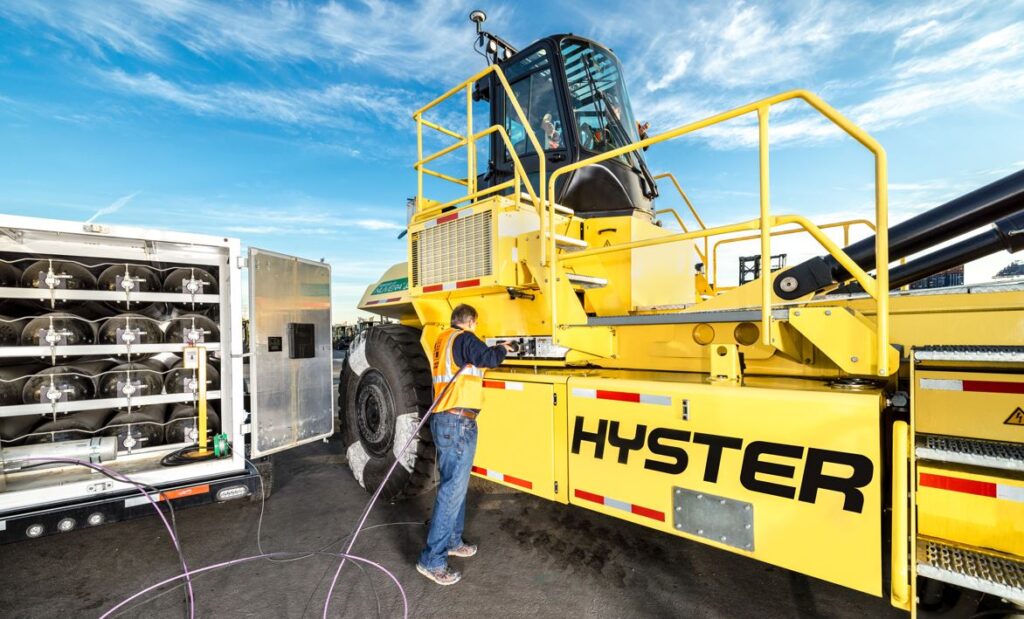
The solution, which is being piloted at the Port of Los Angeles, was named a finalist in the Innovation by Design Awards Hyster Company announces that the business publication Fast Company recognized the hydrogen-powered top pick as a finalist in its Innovation by Design Awards. The port equipment was named among the best sustainable projects of 2023 for its use of design to meaningfully reduce harm to the environment. The top-pick container handler, which is expected to provide emissions savings of 127 tons of carbon dioxide and almost half a ton of criteria pollution per year, is the first of its kind and is currently being piloted at the Fenix Marine Services terminal at the Port of Los Angeles. The truck is powered by two Nuvera® 45kw hydrogen fuel cells working in tandem with an on-board lithium-ion battery, with the fuel cells able to power the equipment directly or charge the battery. This allows operators to refuel the truck in about 15 minutes and then operate for 8 to 10 consecutive hours all while producing no harmful emissions – only heat and water. “With supply chains often accounting for more than 90% of an organization’s emissions, the pressure is on for ports to find sustainable solutions for their heavy-duty applications while still producing at the level they require,” said Jan Willem van den Brand, Director, Global Market Development, Big Trucks, Hyster. “This recognition joins a growing list of accolades that distinguish Hyster for this solution in particular, but also for our broader commitment to developing zero-emission solutions that push the boundaries of what is possible in electrifying intensive industries.” The top-pick container handler is one of several clean power-focused port equipment projects that Hyster is currently working on. Recently, the company shipped a hydrogen fuel cell-powered ReachStacker to Spain’s Port of Valencia, where it will undergo a pilot program of its own at one of Europe’s largest container terminals. Hyster will also supply an empty container handler and a terminal tractor, both powered by hydrogen fuel cells, to a port terminal in Germany, and is working with Capacity Trucks to develop electric and hydrogen-powered terminal tractors.
H&E opens new branch in Texarkana, Texas
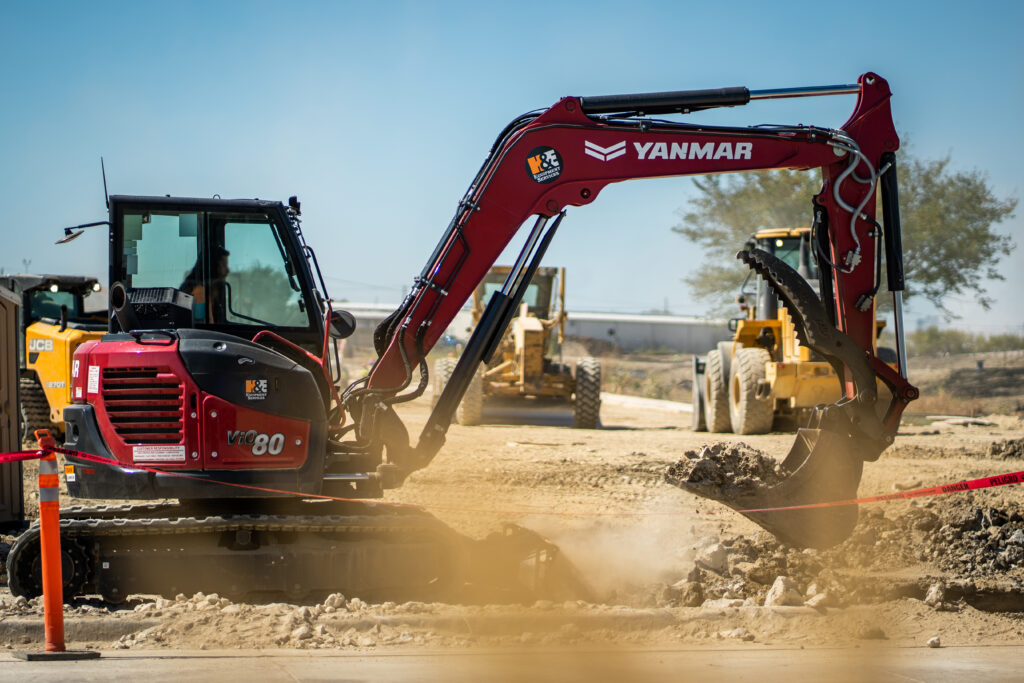
Effective November 6, 2023, H&E Equipment Services Inc. (H&E) announces the opening of its Texarkana branch. The location on the Texas-Arkansas line makes it the company’s 24th rental location in the state of Texas, but it is the third branch to serve the Arkansas market, primarily in the southwestern area of the state. So far this year, H&E has opened 13 new branches across the country. The facility is located at 4300 Gazola Street, Texarkana, TX 75501-7136, phone 430-455-4000. It includes a fully fenced yard area, offices, and a repair shop and carries a variety of construction and general industrial equipment. “H&E has extended its coverage across the Texas-Arkansas state line to easily reach any project between our existing Longview, Shreveport, El Dorado, and Little Rock branches. We’ve added greater fleet availability to the area, and the location of our new facility allows quick access to I-30, I-49, and state highways that branch off in all directions, so delivery of rental equipment to job sites is timely and efficient,” says Branch Manager Hunter Hatfield. “I’ve worked from our Dallas branch for many years, so I’ve hit the ground running and can help customers secure the right equipment for their projects from this new location.” The Texarkana branch specializes in the rental of aerial lifts, earthmoving equipment, telescopic forklifts, compaction equipment, generators, light towers, compressors, and more and represents the following manufacturers: Allmand, Atlas Copco, Bomag, Case, Club Car, Cushman, Doosan, Gehl, Generac Mobile, Genie, Hamm, Hilti, Husqvarna, JCB, JLG, John Deere, Kobelco, Kubota, LayMor, Ledwell, Lincoln Electric, Link-Belt Excavators, MEC, Miller, Multiquip, Polaris, Sany, Skyjack, SkyTrak, Sullair, Sullivan-Palatek, Tag, Towmaster, Unicarriers, Wacker Neuson, Yanmar, and others.
Alta Equipment Group acquires Ault Industries expanding construction equipment segment to Canada

Expands product portfolio with new OEMs, including an exclusive distributorship with McCloskey Diversifies end markets with entrance into Ontario and Quebec’s aggregate and mining industries Ault generated approximately $50.3 million in revenue, $4.5 million in net income, and $7.5 million in adjusted EBITDA for the trailing twelve months through June 30, 2023 and is expected to be immediately accretive to the Company’s free cash flow conversion, profitability, and earnings per share ratios Alta Equipment Group Inc. has announced that it has acquired Ault Industries Inc. (“Ault”), a privately held Canadian equipment distributor with locations in Ontario and Quebec. “The acquisition of Ault represents Alta’s first investment in Canada for our growing construction segment. We are extremely excited to partner with the Ault team as they have built a high-performing equipment dealership in the aggregate and mining space, a growing end market in their region and for Alta,” said Ryan Greenawalt, Chief Executive Officer of Alta. “In addition to entering the major construction markets of Toronto and Montreal, we also eagerly embrace a new relationship with McCloskey, a market leading OEM in the crushing and screening product category. We extend a warm welcome to the Ault team as they become part of the Alta family.” Strategic and Financial Highlights The acquisition expands Alta’s Construction Equipment segment into Canada’s two largest markets. As part of the acquisition, Alta assumes Ault’s exclusive dealer agreement with McCloskey, a best-in-class product in the crushing and screening category. Given Ault’s leading market position and strong brand relationships, the Company expects the acquisition to be accretive to the Company’s EBITDA to cash flow conversion and earnings per share ratios. Additional Transaction Details Total purchase price of $36.0 million, consisting of $23.2 million cash at close, a $2.2 million seller note, and $10.6 million worth of Alta’s common stock, which will be issued at $13 per share, equating to 818,473 shares vesting annually over a five-year period. The purchase price is subject to post-closing working capital adjustments. Ault’s brand name, employees, and management team will remain in place post-close. Including Ault, since the Company’s initial public offering in 2020, Alta has completed 16 acquisitions which have contributed $537 million in revenue, and $66 million in Adjusted EBITDA.
Jungheinrich wins third consecutive EcoVadis platinum certificate for sustainability
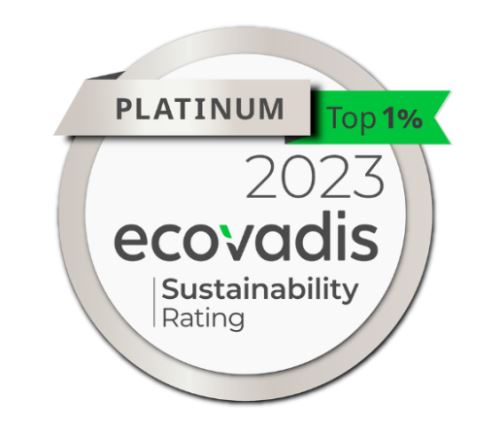
Jungheinrich is once again certified as one of the world’s most sustainable companies Awarded for “outstanding” environmental performance The award reflects Jungheinrich’s comprehensive commitment to human rights and sustainable supply chains Jungheinrich has once again been awarded a platinum certificate from EcoVadis for its corporate commitment, confirming its position among the top 1% of the world’s most sustainable companies. For the third time in a row, the international CSR rating agency EcoVadis has awarded Jungheinrich a platinum certificate for corporate responsibility. The award is recognition of Jungheinrich’s outstanding commitment to the environment, labour and human rights, ethics and sustainable procurement. With the platinum certification, EcoVadis once again confirms that Jungheinrich continues to rank among the top 1 per cent of the world’s most sustainable companies. “Jungheinrich creates sustainable value. We aspire to combine economic success with ecological and social responsibility. EcoVadis’s renewed platinum certification proves that we are succeeding in this. For us, it is both a confirmation of our strategy to date and an obligation to continue to drive forward and expand our commitment in the future as part of our Strategy 2025+. Sustainability is and will remain the foundation of our Group activities,” says Dr Lars Brzoska, Chairman of the Board of Management of Jungheinrich AG. Pioneer in environmental protection and human rights This year, EcoVadis particularly highlighted Jungheinrich’s “outstanding” environmental performance. Here, the company achieved the maximum number of points thanks to (among many notable factors) its effective measures to reduce greenhouse gas emissions and conserve valuable resources. Jungheinrich has made a clear commitment to the 1.5-degree target and aims to establish CO2e-neutral business operations at all sites and plants worldwide by 2030. All Jungheinrich sites in Germany, including the six German factories, have been sourcing exclusively green electricity since 2021. Since then, the Jungheinrich Group has continued to push ahead with the switch to renewable energies worldwide, with the transition to green electricity now complete in 21 countries. An important factor in this is the generation of the company’s own solar power. The company continues to equip its sites with photovoltaic systems, and recently covered the parking lot of its corporate headquarters in Hamburg with a 1,100-square-metre photovoltaic system. Jungheinrich also conserves resources by remanufacturing used forklifts on an industrial scale. Through this process, up to 99 per cent of the raw materials used in the truck are reused or recycled, saving up to 80 per cent CO2e compared to new production. In addition, Jungheinrich makes great efforts to ensure compliance with human rights along its value chain. To this end, the company has expanded its existing sustainable procurement management system to take particular account of human rights aspects. To tighten internal processes for ensuring human rights due diligence, Jungheinrich has also implemented an appropriate risk management system and defined the role of its Human Rights Officer and Human Rights Council, which brings together human rights experts within the Group. Jungheinrich conducts regular risk analyses to identify, assess and prevent potential human rights violations at an early stage. Jungheinrich’s platinum EcoVadis certifications in 2023, 2022 and 2021 build on the award of gold certificates in 2020 and 2019. EcoVadis is considered one of the world’s leading institutions for assessing corporate responsibility. Only the most sustainable 1% of all companies assessed receives a top platinum certificate from EcoVadis. In total, EcoVadis analyses the sustainability management of more than 100,000 companies worldwide with regard to the environment, labour and human rights, ethics, and sustainable procurement.
Bobcat Compact Loader inventors inducted into National Inventors Hall of Fame
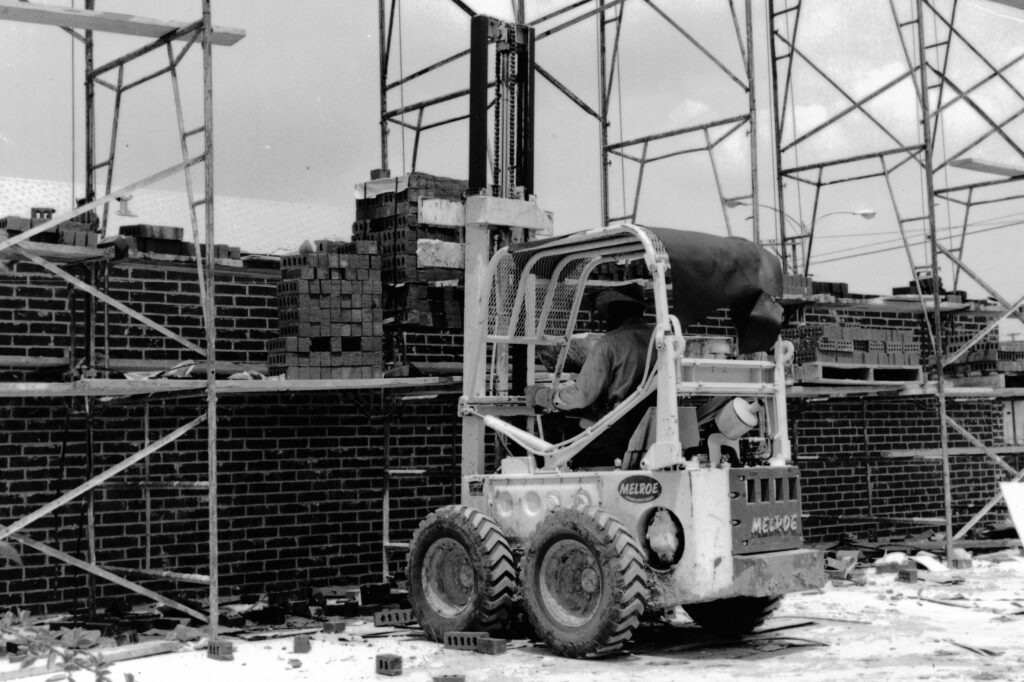
Cyril and Louis Keller Recognized During Illumination and Induction Ceremonies in Washington, D.C. Cyril and Louis Keller, the brothers who invented the world’s first compact loader (later named the Bobcat® skid-steer loader), have formally been inducted into the National Inventors Hall of Fame (NIHF). The Keller brothers were posthumously recognized during the NIHF Illumination and Induction Ceremonies held Oct. 25-26 in Washington, D.C. NIHF annually recognizes inventors, promotes creativity and advances the spirit of innovation and entrepreneurship. Bobcat representatives, along with members of the Keller family, were in attendance to celebrate this achievement. “The ingenuity of the Keller brothers spurred the compact equipment industry,” said Mike Ballweber, president, Doosan Bobcat North America. “Today at Bobcat, their spirit of inventiveness lives on, as our organization continues to innovate for the jobsite of the future and empower our customers to accomplish more.” The Illumination Ceremony at the National Inventors Hall of Fame Museum was celebrated Oct. 25 in Alexandria, VA. New inductees or their family members placed their names on illuminated hexagons in the museum’s Gallery of Icons. Members of the Keller family represented Cyril and Louis in this symbolic ceremony. The 2023 National Inventors Hall of Fame Induction Ceremony was held Oct. 26 at The Anthem in Washington, D.C., where the new Inductee class was honored for its contributions to society. Joe Keller, son of Louis, said, “If Dad and Cyril were here to accept this award, they would accept it for all the early and current Bobcat employees that have all helped bring the little Keller loader to be the Bobcat machine it is today. There is no one that the Bobcat loader hasn’t affected or helped through life—even though they may not know it.” Inventing an Industry In the 1950s, brothers Cyril (1922- 2020) and Louis (1923-2010) operated a small machinist-blacksmith shop in Minnesota, building and repairing machinery for local farmers. A farmer approached them with a need for a self-propelled loader light enough to be lifted to the second floor of a turkey barn and small enough to clean around the barn’s upright poles. In 1957, the Kellers built a three-wheeled loader with two drive wheels in front and a caster wheel in the rear – the precursor to the modern skid-steer loader. The loader came to the attention of Melroe Manufacturing Company (now Bobcat Company), which was awarded exclusive manufacturing rights to the machine on a royalty basis. Melroe hired the Kellers to refine the design and put the machine into production. To improve the design of the loader, a second set of drive wheels was added to the back of the loader in 1960. With four-wheel drive, the M400 became the world’s first true skid-steer loader. “Skid-steer” describes the unique steering system that enables the machine to turn within its own length. Later, the Bobcat brand name was established because of the machine’s toughness, quickness and agility. Commemorating its History In celebration of this recognition, Bobcat has its history on display in a new exhibit within the NIHF Museum. The museum exhibit features one of the Keller brothers’ original three-wheel loaders, along with a timeline of Bobcat’s history and a video display highlighting various aspects of Bobcat’s products, people and initiatives. The Bobcat exhibit will be on display through April 2024. Learn more about the history of Bobcat.
Industrial Forklifts adds new Major Accounts Manager
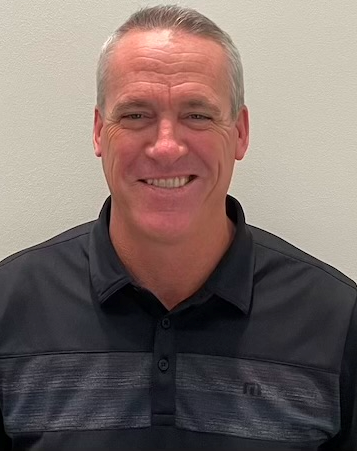
Industrial Forklifts in Phoenix, AZ has announced Trevor Cavanaugh will be their New Major Accounts Manager handling Oklahoma, Texas, New Mexico, Wyoming, Colorado, Arizona, and Southern California. Trevor brings a wealth of experience and a fresh perspective to their team. With 25 years of proven success in the industry, and an NCAA background, he has a track record of driving sales growth and fostering collaboration. His strategic vision and leadership skills will undoubtedly help your sales team and provide better support with Industrial Forklifts. Trevor will oversee Industrial Forklifts dealer development and implementing sales strategies.
Toyota Material Handling leadership gives back in St. Louis
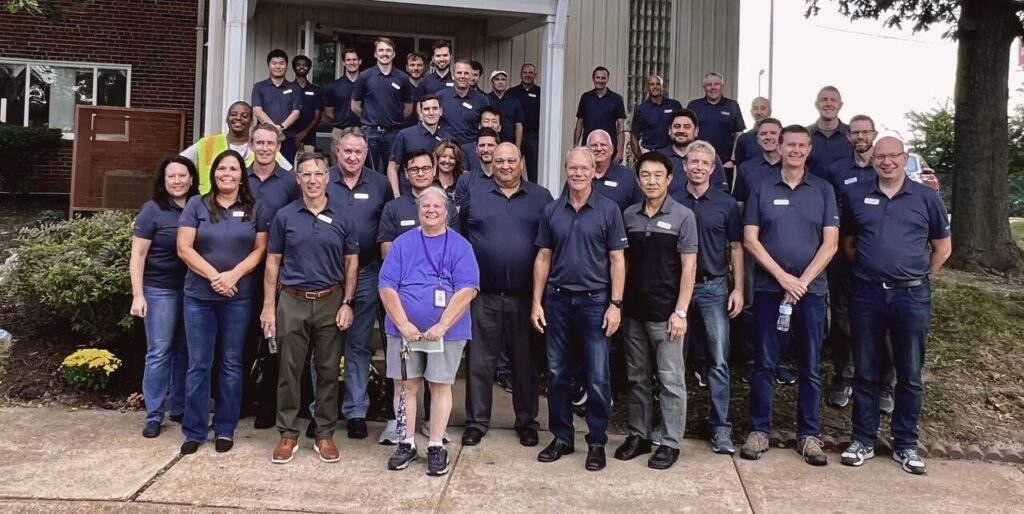
The Toyota Material Handling North America leadership team held a Strategic Planning Session in St. Louis and gave back during their business meeting. On Brett Wood’s LinkedIn page he made mention of this special giving back opportunity. “I’m proud that our entire leadership team always makes time in their schedule to volunteer in the city where we host our meeting. This is a perfect opportunity to put our corporate responsibility into practice and prioritize Toyota’s Core Values.” said Wood. This year the Toyota Leadership team volunteered at Lydia’s House, a center that provides a place of healing and hope for women and children who are victims of domestic violence. “We helped improve their landscaping, cleaned apartments, and set up furniture and essential items in apartments that provide a positive atmosphere to these families when they need it most.” said Wood. “These leaders make me proud for arriving a day early to volunteer at impactful organizations like Lydia’s House. These events are poignant reminders that if you want to lift yourself up, lift someone else first.” added Wood.
KION Group delivers strong earnings and free cash flow in the first nine months of 2023 and raises outlook
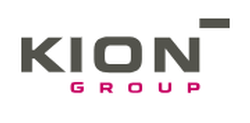
Revenue at €8.347 billion (Q1–Q3 2022: €8.243 billion) Adjusted EBIT more than doubles to €571.9 million (Q1–Q3 2022: €210.6 million) Adjusted EBIT margin at 6.9 percent (Q1–Q3 2022: 2.6 percent) Strong free cash flow at €329.3 million (Q1–Q3 2022: minus €971.9 million) Sustainability: MSCI increases KION Group’s ESG rating to AAA Outlook raised for the Group’s adjusted EBIT and free cash flow KION Group strengthens leadership team The KION Group achieved a strong increase in its profitability and free cash flow in the first nine months of this year. These results were mainly driven by a continued momentum in the Industrial Trucks & Services (ITS) segment. The primary reasons for this impressive performance were the stabilization of the supply chain enabling higher production volumes, and the positive effects of the measures initiated in 2022 to boost commercial and operational agility. “The significant upward trajectory of KION Group is once again underscored by these strong results for the first nine months of this year”, says Rob Smith, Chief Executive Officer of KION GROUP AG. “This strong momentum reinforces our leading position in intralogistics solutions for customers worldwide.” Consolidatedrevenue amounted to €8.347 billion in the first three quarters of 2023, a year-on-year rise of 1.3 percent (Q1–Q3 2022: €8.243 billion). The proportion of consolidated revenue attributable to the service business increased to 44.6 percent (Q1–Q3 2022: 41.7 percent). Total revenue in the Industrial Trucks & Services segment increased by 16.5 percent to €6.160 billion (Q1–Q3 2022: €5.288 billion). The systematic processing of the sizeable order book built in 2022 had a positive impact on revenue in the segment. In addition, price increases implemented in the previous year made a substantial contribution to revenue growth. At 48.1 percent, the proportion of the segment’s external revenue attributable to the service business was lower than in the prior-year period (Q1–Q3 2022: 51.7 percent). In the Supply Chain Solutions segment, total revenue contracted by 25.4 percent to €2.216 billion (Q1–Q3 2022: €2.970 billion). Whilst the stable and higher-margin service business (customer services) registered a proportionate increase to 34.9 percent (Q1–Q3 2022: 23.9 percent) of total revenue muted customer demand in the project business (business solutions) in the preceding quarters led to a drop in revenue. Moreover, the projects secured in the reporting period were predominantly of a long-term nature, from which the revenue will be recognized over an extended period. Adjusted EBIT for the nine-month period increased to €571.9 million (Q1–Q3 2022: €210.6 million). Price adjustments introduced in 2022 and, on the supply side, the general improvement in the availability of materials and stable costs contributed to these strong earnings. Reflecting this, the KION Group’s adjusted EBIT margin significantly increased to 6.9 percent (Q1–Q3 2022: 2.6 percent). The adjusted EBIT of the Industrial Trucks & Services segment more than doubled to €613.6 million (Q1–Q3 2022: €300.4 million). This was partly due to the earnings effect from increases in volumes and prices and the efficiency gains in production. The ITS segment’s adjusted EBIT margin returned to double digits to 10.0 percent for the first nine months of the year (Q1–Q3 2022: 5.7 percent). Adjusted EBIT for the Supply Chain Solutions segment was €30.7 million in the first three quarters of 2023 (Q1–Q3 2022: € minus 32.2 million). The segment’s earnings improved in the third quarter with the successive completion of lower-margin orders. The adjusted EBIT margin for the first nine months of 2023 turned positive to 1.4 percent (Q1–Q3 2022: minus 1.1 percent). The Group’s net incomefor the period amounted to €228.3 million, which was up by €161.4 million year on year (Q1–Q3 2022: €66.9 million). Basic earnings per share attributable to the shareholders of KION GROUP AG came to €1.70 (Q1–Q3 2022: €0.48) based on a weighted average of 131.1 million no-par-value shares (Q1–Q3 2022: 131.1 million). The Group generated free cash flowof €329.3 million (Q1–Q3 2022: € minus 971.9 million) during the reporting period. MSCI, one of the leading index providers, raised the KION Group’s sustainability rating to AAA at the end of September, putting the KION Group in the top 10 percent of its sector. Outlook In the third quarter of 2023, the KION Group once again significantly increased its earnings and margins compared with the corresponding quarter of 2022. The ongoing positive effects of the measures taken to enhance operational and commercial agility led to a particularly noticeable improvement in the financial performance of the Industrial Trucks & Services segment and thus of the Group compared with the first half of 2023. Having already updated it in July 2023, the KION Group has once again raised its 2023 full-year outlook for the key performance indicators adjusted EBIT, free cash flow and return on capital employed (ROCE) because the earnings of the Industrial Trucks & Services segment in the third quarter of 2023 were better than expected. This was primarily due to the continued improvement in the availability of materials and the easing of material prices on the supply side. The 2023 full-year outlook for revenue and adjusted EBIT in the Supply Chain Solutions segment has been lowered. This is because the customer orders received in the reporting period were predominantly for long-term projects, which means that only a small volume of revenue from these projects will be recognized in 2023. Furthermore, customers are continuing to postpone the placement of orders. In light of this situation, the Executive Board of KION GROUP AG decided on October 13, 2023 to update the outlook for 2023, both for the Group and for the Industrial Trucks & Services and Supply Chain Solutions segments. The outlook had originally been published on March 2, 2023 and was most recently updated in July 2023. The new outlook is shown below: Outlook for 2023 KION Group Industrial Trucks & Services Supply Chain Solutions Outlook July 2023 Outlook October 2023 Outlook July 2023 Outlook October 2023 Outlook July 2023 Outlook October 2023 Revenue1 minimum €11.4 billion minimum €11.2 billion minimum €8.2 billion minimum €8.2 billion minimum €3.2 billion minimum €3.0 billion Adjusted EBIT1 minimum €680 million minimum €780 million minimum €730 million minimum €830 million minimum €65 million minimum €55 million Free cash flow minimum €615 million minimum €660 million – – – – ROCE minimum 6.0% minimum 7.0% – – – – 1 Disclosures for the Industrial Trucks & Services and Supply Chain Solutions
Toyota Material Handling receives Manufacturing Excellence Award for community impact
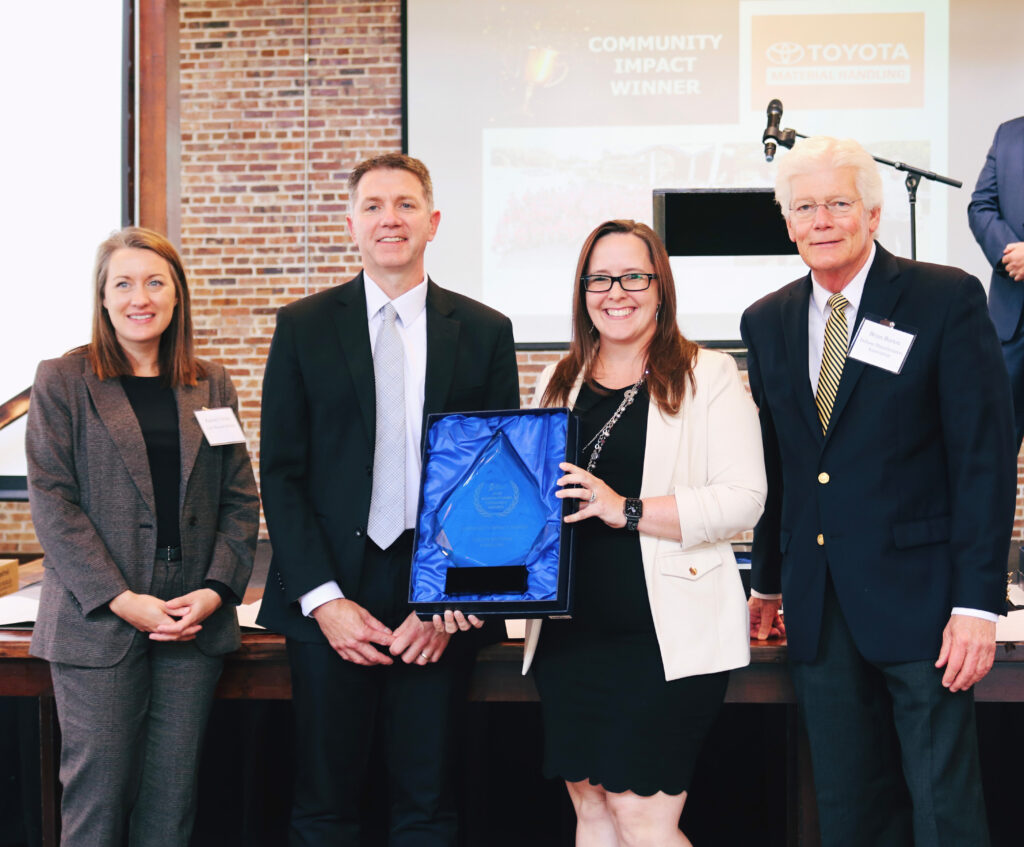
Toyota Material Handling (TMH), the North American leader in material handling innovation, received the 2023 Manufacturing Excellence Award for Community Impact during the Indiana Manufacturers Association’s (IMA) Hall of Fame Luncheon last week at Indianapolis’ Bitwell Event Center. The awards, given annually by the IMA, recognize manufacturers that make important contributions to the customers and communities they serve and set an example for other companies to follow. Toyota Material Handling was selected from a large group of applicants for showing exemplary leadership and a strong commitment to community service as reflected in its company policy, resources and employee participation. “At Toyota, we believe it is our responsibility to contribute to society in meaningful ways and make a real difference in the communities in which we live and work,” said Tony Miller, Toyota Material Handling Senior Vice President of Operations, Engineering & Strategic Planning. “We take that responsibility seriously, and it’s an honor to be recognized with this award by the IMA. I’d like to thank every one of our associates for their unwavering commitment to making our community a better place. This award is not about the contributions of a few; it’s only possible because of the efforts of everyone at Toyota. We will always seek opportunities to invest in the communities we serve and dedicate our time and resources to continuously improve the lives of those around us.” Corporate social responsibility is integral to Toyota’s culture. Toyota has cultivated numerous community-focused relationships, including corporate partnerships with the American Red Cross, United Way and Anchor House, a local nonprofit focusing on investing in neighbors through housing, employment resources and nutritional assistance. Throughout the year, Toyota sponsors and organizes volunteer activities on and off Toyota’s campus. In 2022, Toyota associates donated 12,000 hours of their time to support local organizations, contributing to a total economic impact of $750,000. “We instituted the Indiana Manufacturers Hall of Fame Awards in 2015 to help bring awareness and recognition to the many positive contributions of Hoosier manufacturers, and added the Manufacturing Excellence Awards in 2019 to focus and honor companies in specific areas of achievement,” said IMA President and CEO Brian Burton. “We congratulate Toyota Material Handling for their outstanding work and continued dedication to making Indiana manufacturing a positive and driving force for the state.”
H&E relocates branch in Pompano Beach Florida
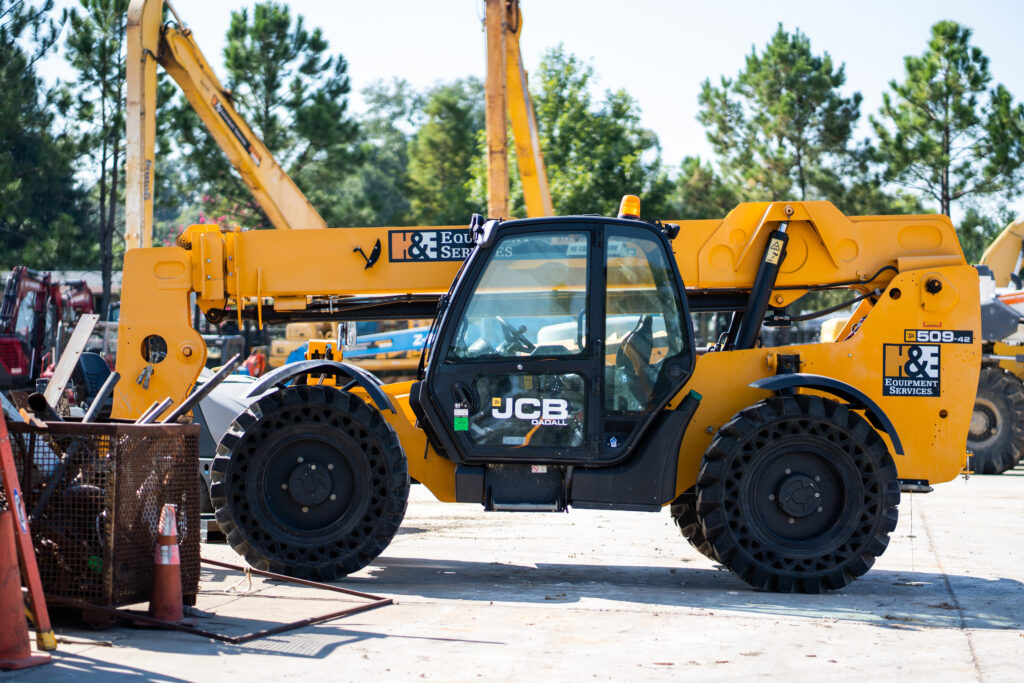
Effective October 18, 2023, H&E Equipment Services Inc. (H&E) has announced the relocation of its Pompano Beach, FL, branch. The facility is now located at 1660 N. Powerline Road, Pompano Beach, FL 33069-1623, phone 954-781-3099. The newly renovated property includes a fully fenced yard area, offices, and a separate repair shop and carries a variety of construction and general industrial equipment. “Our Pompano Beach location is just 2.6 miles northwest of our previous address. The newly renovated facility provides a comfortable environment, has a larger, more efficient yard to hold a variety of fleet, and maintains direct access to I-95 to move equipment quickly,” says Branch Manager Anthony Wallace. “And with our Hollywood branch just 17 miles south, we can work together to quickly locate available equipment and provide faster response time to job sites throughout South Florida.” The Pompano Beach branch specializes in the rental of aerial lifts, earthmoving equipment, telescopic forklifts, compaction equipment, generators, light towers, compressors, and more and represents the following manufacturers: Allmand, Atlas Copco, Bomag, Case, Club Car, Cushman, Doosan, Gehl, Generac Mobile, Genie, Hamm, Hilti, Husqvarna, JCB, JLG, John Deere, Kobelco, Kubota, LayMor, Ledwell, Lincoln Electric, Link-Belt Excavators, MEC, Miller, Multiquip, Polaris, Sany, Skyjack, SkyTrak, Sullair, Sullivan-Palatek, Tag, Towmaster, Unicarriers, Wacker Neuson, Yanmar, and others.
Industrial Forklifts ushers in “New Chapter” with new headquarters & full rebrand
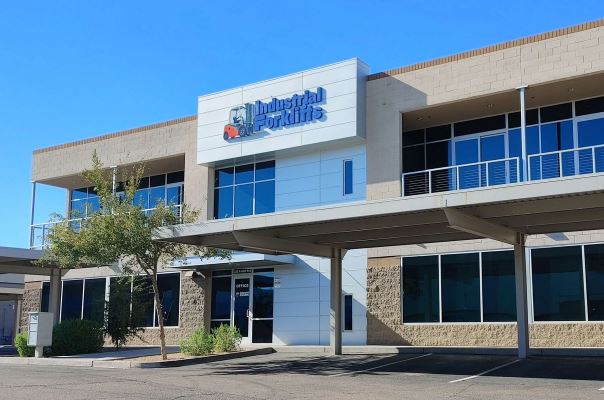
The Southwest has a new forklift brand to help it grow. Industrial Forklifts, Inc., the sole distributor of the Heli forklift brand in the Western United States, has completed its move from Denver, CO, to Phoenix, AZ. In the process they’ve acquired a totally new facility in the Papago Industrial District, off 48th Ave and Van Buren. The facility boasts parts storage, a state-of-the-art training room, and of course, a full showroom of material handling equipment. The Phoenix facility sites on 1.12 acres, with 36,000 sq. ft. dedicated to parts, service, and a showroom floor. Who’s it for? To strengthen their Dealer and Rental Network coverage across the U.S. “Everything’s new about our Phoenix location,” says Dan Summers, Director of Aftermarket Sales at Industrial Forklifts. “Due to the rapid expansion of Industrial Forklifts’ customer base, and the success of the Heli forklift line in America, we came to Phoenix for a new chapter.” To cap off the expansion, the new Industrial Forklifts building sports a brand-new logo. Industrial Forklifts began as a part of FMH Material Handling Solutions in 2006, based in Denver. Through a series of acquisitions and business choices, the Industrial Forklifts brand and team split from FMH in 2022. With the new Phoenix location, Industrial Forklifts has a new showcase to continue its mission of introducing Heli forklifts to all businesses. “We’re open and here to help,” says Nick Gushue, Vice President. “Everyone’s welcome to come by!”
Combilift’s CB15-5E wins the Italian Terminal and Logistics Award
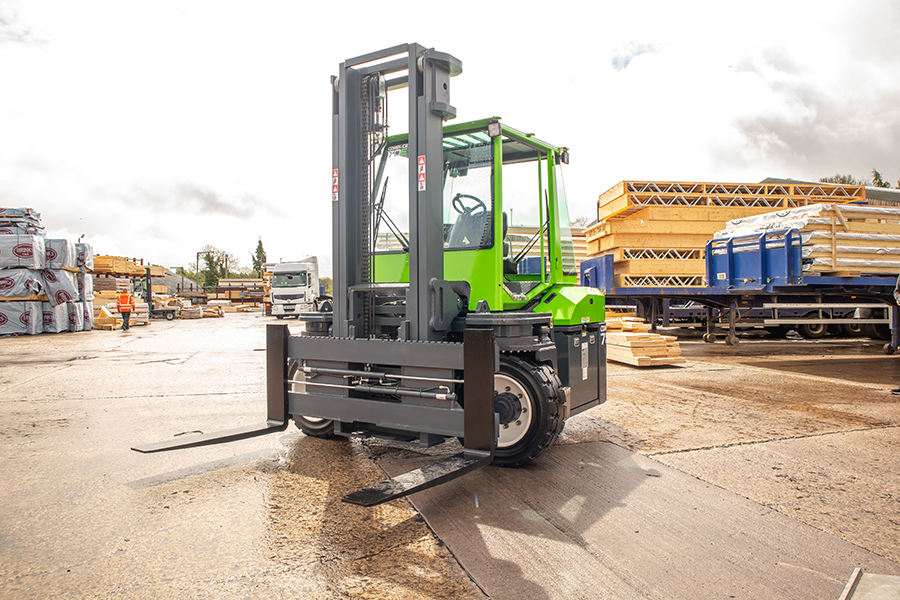
Combilift pick up award while attending GIS Expo in Italy Combilift, the largest global manufacturer of multidirectional trucks, articulated forklifts, and straddle carriers has announced that the Combi-CB15-5E has been honored with the coveted Italian Terminal and Logistics Award. This prestigious accolade recognizes the innovation in the operational field and its commitment to operator training and safety. The Italian Terminal and Logistics Award is a significant industry recognition, presented annually to highlight the skills of operators in port, intermodal, and logistics terminals both in Italy and abroad. The new Combi-CB15-5E is a further addition to Combilift’s ever-growing range of electric models which offers powerful performance, extensive battery life, and unrivaled ergonomics. This model, in the vibrant Combi-green livery, boasts the distinction of being the shortest 15,500lbs capacity counterbalance truck on the market whilst also benefitting from multidirectional ability, enabling the versatile space-saving handling of both long and bulky loads. Martin McVicar – CEO and Co-Founder of Combilift accepted the award alongside their EA Group partners and said: “We are honored to receive the Italian Terminal and Logistics Award for the CB155E. This recognition validates our unwavering commitment to innovation, safety, and training in the material handling industry. The CB15-5E is a perfect example of our dedication to providing our customers with efficient, eco-friendly, and safe solutions.”
A home run for Bigfork: Community impact project transforms local baseball field
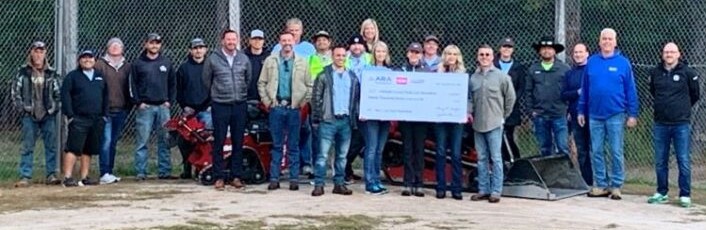
ARA, Toro Company Foundation, Local volunteers step up to the Plate for Area Youth The American Rental Association (ARA) Foundation, in partnership with The Toro Company Foundation, Flathead County Parks and Bigfork Baseball Association, completed a Community Impact project in Bigfork, Montana to benefit Aero Lane Park, a local baseball field. On September 27, volunteers from all four organizations worked together to enhance and upgrade the baseball diamond and park amenities. This included creating a new infield, new backstop fencing, refurbished bleachers and dugout benches as well as beautification updates throughout the park. “Creating high-quality playing fields is crucial to the ballplayers’ experience. ARA members from the local community and across the northwest region stepped up to the challenge, using their professional talents and equipment to transform the field and beautify the park,” said Judson McNeil, ARA Foundation director of programs and fundraising. To complete the work at the field, volunteers from ARA, The Toro Company Foundation and representatives from seven northwest regional and local rental operations turned out. The volunteers moved grass, replaced and stained bleachers, installed new gravel in the dugouts and parking areas, aerated the field and much more. All projects required the use of different equipment provided by local rental stores. “Having an outdoor space for our community’s youth to recreate, create memories, develop friendships and build character is an important aspect of our department,” said Chris Maestas, Flathead County Park director. “The generous monetary donation by ARA and Toro as well as the time and effort from their volunteers to improve a little league baseball field that is used heavily by the Bigfork community will have a lasting impact on the ball players and the community as a whole. Flathead County is fortunate to have the support of the groups and individuals who have stepped up to the plate to support our youth through parks and recreation.” The Bigfork project is the third Community Impact project the ARA Foundation has completed in partnership with The Toro Company Foundation in 2023. Planning is underway for the 2024 projects, visit the ARA Foundation website to learn more and submit an application.
Mitsubishi Logisnext Americas hosts over 60 students at Marengo facility for National Manufacturing Day
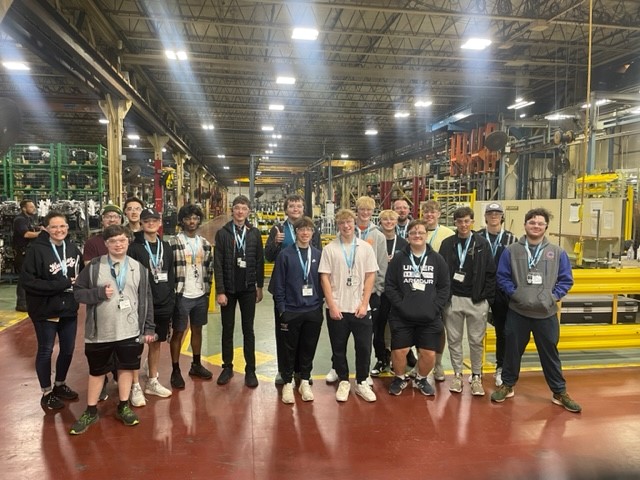
Mitsubishi Logisnext Americas group (Logisnext), a North American provider and manufacturer of material handling and innovative automation and fleet solutions, proudly opened its doors to over 60 local high school students for an exclusive tour of the Marengo facility in celebration of National Manufacturing (MFG) Day, Oct. 6. Led by Jon Crane, Senior Manager of Manufacturing Engineering and Facilities, Rob Jasinski, Director, Production, and Kenzie Heatherwick, Manufacturing Engineering Lead, from Mitsubishi Logisnext Americas, the tour provided an invaluable opportunity for students to explore the manufacturing world and discover exciting career prospects across the globe. During this tour, students had the chance to learn more about Logisnext’s cutting-edge technologies and innovative solutions. They gained firsthand experience with the manufacturing process which included everything from the fabrication of parts and robotic welding to powder coat painting and product assembly. “Innovation fuels manufacturing and tours like these are essential in nurturing our youth’s curiosity,” said Jon Crane, Senior Manager of Manufacturing Engineering and Facilities, Mitsubishi Logisnext Americas. “Our mission at Mitsubishi Logisnext Americas is not only to provide innovative solutions but also to inspire the next generation of manufacturing leaders. We aim to bridge the gap between education and industry providing students with a glimpse into the dynamic realm of manufacturing.” According to the National Association of Manufacturers, there is a pressing need to fill 4.6 million high-skill, high-tech, and high-paying jobs over the next decade. National MFG Day serves as a collaborative platform for manufacturers to address shared challenges, promoting not only individual growth but also community development and ensuring a thriving future for generations to come. Mitsubishi Logisnext Americas remains committed to fostering the growth of the manufacturing sector. The student tour underscores the company’s dedication to nurturing talent and promoting innovation within the industry.
Fairchild Equipment expands in Marinette WI
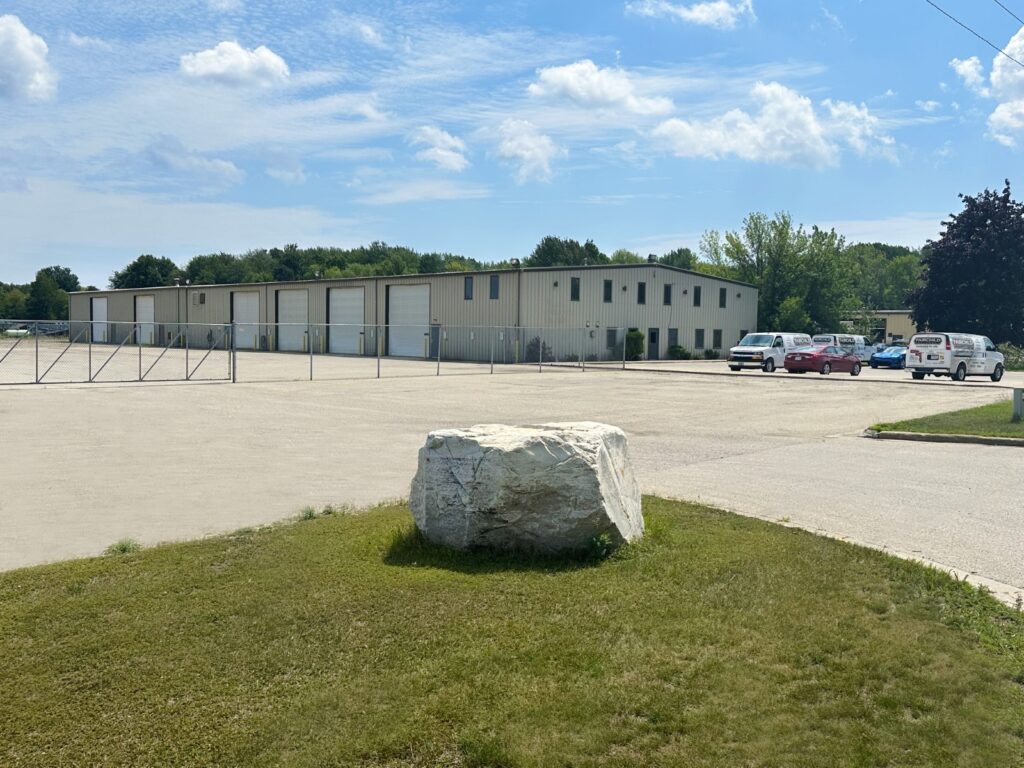
A new facility to support business communities in Northern Wisconsin and Upper Michigan Fairchild Equipment has announced the opening of its new facility in Marinette, Wisconsin. Since opening its first Marinette location at 2815 Mary Street in 1992, the company has experienced tremendous growth, leading to the need for a larger facility. Effective October 1, 2023, all operations will be conducted out of the new location at 2505 Biehl Avenue. “We are excited to be taking this step to help us continue to support the business communities in Northern Wisconsin and Upper Michigan,” said CEO of Fairchild Equipment, Chad Fairchild. “It has been our commitment to those businesses and their trust in us that has allowed us to become a major supplier of material handling equipment, parts, service, and fleet management for Northern Wisconsin and Michigan’s Upper Peninsula.” This new facility marks the fourth facility expansion since 2020 in Fairchild Equipment’s network of locations throughout the Midwest. It will better accommodate the expansive product line Fairchild Equipment offers, which includes warehouse and material handling equipment as well as engineered storage solutions and fleet management services. “Our team’s commitment to our mission of creating Customers for Life in this area is what has allowed us to grow to another level,” said Fairchild. “We are confident that our new facility will help us even better serve our customers and provide the best possible service.” The new facility is triple the size of the previous one. It will feature a showroom and a variety of new, used and rental equipment in stock. It will also feature a larger parts department, helping customers to get the parts they need faster. With a larger service department, customers will also be able to get their equipment serviced more quickly. “We are excited to be able to offer our customers a larger facility with more services and products,” said Mark Stammer, Director of Sales for Wisconsin, Michigan and Illinois. “We want to thank the companies that have entrusted us with supplying and maintaining their material handling equipment over the years. It’s been our commitment to those businesses and their trust in us that has allowed us to become a major supplier of material handling equipment, parts, service, and fleet management for Northern Wisconsin and Upper Michigan. We look forward to continuing to provide industry-leading support to our current customers and to the new customers who choose to partner with us in the future.”
Hyundai Material Handling introduces new branding

Hyundai Material Handling, a business unit of HD Hyundai Construction Equipment North America, Inc., is introducing new branding that reflects its growing presence and evolving mission in North America and as a global leader in the manufacturing of advanced material handling equipment. “Forging our own path sets Hyundai apart,” said Lewis Byers, Executive Vice President/COO, Hyundai Material Handling. “Now, it’s time that our brand – the name, image, and message, we send to the marketplace – captures our commitment to innovation and our focus on the future.” The branding includes a new corporate name and logo, new branding colors, and an updated look for its HYUNDAI MATERIAL HANDLING equipment brand. The new corporate name is HD Hyundai Xitesolution-Material Handling. The HD stands for Human Dynamics, reflecting the company’s mission of helping individuals achieve their goals. The Hyundai Xitesolution name links together it’s world-famous brand with how Hyundai is going beyond manufacturing to be a solutions provider to customers in an ever more competitive and complex world. “Material Handling” will continue to identify the equipment Hyundai offers and the market it serves. Included in the updated logo is a new “Forward Mark” icon that replaces the company’s familiar triangles. This new icon conveys Hyundai’s commitment to pushing forward, finding new innovations and new ways to help its customers move forward and be more efficient and productive in a changing world. As part of Hyundai’s commitment to sustainability, the new branding includes a new color treatment, merging its traditional blue with green. While the company has a new corporate logo, for dealers and customers, the company’s main brand ID will remain HYUNDAI MATERIAL HANDLING, helping to sustain the company’s dramatic growth in sales and awareness in the North American market. “A lot is changing in the way we present ourselves to the market,” added Lewis Byers. “But we want our dealers and forklift owners to know that some things will never change for us, and that’s our dedication to offering quality, value, and innovation in our products and services, and our commitment to make certain that when it comes to material handling, no one delivers more.”