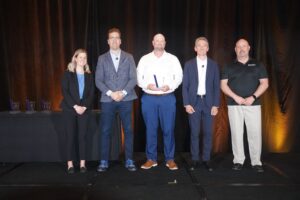
Carolina Handling wins Kautex Safety Award for AGV implementation
Carolina Handling has received the 2023 Health & Safety Award for Excellence from Kautex, A Textron Company, a Tier One
Carolina Handling has received the 2023 Health & Safety Award for Excellence from Kautex, A Textron Company, a Tier One
Toyota Material Handling receives the 2023 GOOD DESIGN Award as a testament to the engineering and design quality of the
Revenue up by 2.8 percent to € 2.859 billion (Q1 2023: € 2.781 billion) Adj. EBIT improves to € 226.7
EV Industry veteran brings extensive experience in accelerating growth AMPURE, formerly Webasto Charging Systems, appoints John Thomas as Global Head
Fairchild Equipment has announced that for the eighth time, we have been recognized by Hyster Company with the 2023 Dealer
Toyota Material Handling announced Welch Equipment Company as a recipient of the annual President’s Award at the company’s annual dealer
Bobcat Company recognized Forklifts Group as a top-performing material handling equipment dealer with a Diamond award at MODEX 2024. Dealers
CLARK Material Handling Company has announced the launch of the SE25-35, a 5,000-7,000-pound indoor/outdoor pneumatic forklift. Powered by a 48V
For the 33rd year in a row, Carolina Handling has been named a Dealer of Distinction (DOD) by The Raymond
Shoppa’s has announced that Toyota Material Handling (TMH), its main brand manufacturer, has awarded Shoppa’s Mid America the Toyota President’s
OTR Engineered Solutions (OTR) has announced that its new facility being built in Mexico is scheduled to commence business operations
Yale Lift Truck Technologies has announced winners of the 2023 Dealer of Excellence award, the company’s top honor for members
Hyster Company has announced the recipients of its 2023 Dealer of Distinction award, recognizing individual dealer performance and success during
Perkins has served as executive vice president of operations at Carolina Handling since April 1, 2020. He joined the company
H&E Equipment Services, Inc. has announced the signing of a definitive agreement to acquire Lewistown Rental, a Lewistown, Montana-based equipment
Where are forklifts made? Contrary to the prevailing notion that little is manufactured in the USA nowadays, the majority of
Hyundai Material Handling (HMH) has announced the winners of this year’s dealer awards at a ceremony held during MODEX 2024.
Mark Taggart assumed his new role as Chief Financial Officer of Toyota Material Handling North America on April 1. Taggart
Awards given to top-performing material handling equipment dealers Atlantic Forklift Services was recently recognized for superior performance as a Bobcat
Yale Lift Truck Technologies has announced that Jay Costello, who formerly served as director of dealer marketing, has received a lifetime