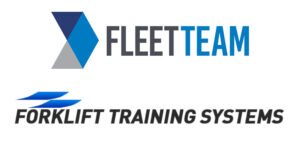
Fleet team expands with strategic acquisition of Forklift Training Systems
Fleet Team, fleet management and consulting company, has announced its acquisition of Forklift Training Systems, headquartered in Newark, Ohio. This
Fleet Team, fleet management and consulting company, has announced its acquisition of Forklift Training Systems, headquartered in Newark, Ohio. This
Toyota Material Handling announced the winners of the annual President’s Award, which recognizes the top Toyota forklift dealers in North
Effective April 1, 2024, H&E Rentals (H&E) announces the opening of its Decatur branch, the sixth general rental equipment location
Forklift operators who are insufficiently aware of the load they are lifting and the risks that come with exceeding the
The Program Recognizes the Company’s Highest Performing Dealers Across the U.S. and Canada Bobcat Company has announced its 2024 Dealer
The partnership between the home renovation expert and entrepreneur and the equipment manufacturer aims to inspire and empower Chip Gaines
The Manitowoc Company, Inc. has announced that board member John C. Pfeifer has chosen not to stand for reelection to
Bobcat Company and the National Recreation and Park Association (NRPA) are celebrating the culmination of their 2023 partnership grant to
University Research Program has invested more than $5 million in funding to advance the future of material handling The Raymond
Fairchild Equipment has announced the relocation of its Duluth, Minnesota facility to a new, more expansive location at 1308 18th
Raymond West is celebrating a significant milestone marking 75 years as a Raymond Intralogistics Solutions Provider. Raymond West has grown from
In the ever-evolving landscape of the forklift industry, staying ahead of market trends is crucial for resellers to maintain a
Brand recognized as stand-out industry leader in manufacturing, equipment design and automation Bobcat Company has been recognized as one of
RAVAS invites you to visit our booth at LogiMAT 2024 in Stuttgart. Located in Hall 10, Booth 10F76, they will
Toyota Material Handling North America (TMHNA), comprised of two main companies, Toyota Material Handling and The Raymond Corporation, will establish
Awards given to top-performing material handling equipment dealers Bobcat Company has recognized 21 material handling dealers for superior performance
Simplifies acquisition process, provides added flexibility Mitsubishi Logisnext Americas (Logisnext), a manufacturer and provider of material handling, automation, and fleet
Technology designed to support warehouse safety initiatives now available on 59 Yale forklift models Yale Lift Truck Technologies announced the
PS Logistics, a transportation and logistics company in the United States, has announced that its subsidiary Diamond State Trucking &
Fairchild Equipment, a provider of material handling solutions in the Midwest, has announced its expanded dealer footprint as the official