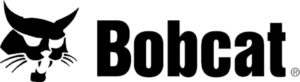
Year in Review: Bobcat recaps new products, investments and initiatives of 2023
As 2023 comes to a close, Bobcat Company is recapping its major initiatives and announcements from the year. Bobcat, a
As 2023 comes to a close, Bobcat Company is recapping its major initiatives and announcements from the year. Bobcat, a
Organizations introduce new state-of-the-art bloodmobile to support community Toyota Material Handling’s ongoing partnership with the American Red Cross continues to
Doosan Bobcat, Inc., a company within Doosan Group, will showcase its latest product and technology concepts Jan. 9-12, 2024, at
Based in Phoenix, Ariz., Precision operates a branch in Phoenix and a second location in Aurora, CO H&E Equipment Services
CLARK Material Company employees have been #RaisingHope and spreading Holiday cheer by sponsoring 100 children on the Lexington Salvation Army’s
Bobcat Company and its employees recently held their annual fall giving campaign, garnering more than $175,000 in donations to nonprofit organizations in 17
Irish-based forklift manufacturer Combilift celebrated 25 years in business in 2023 and has wrapped up the year by producing a
George Arrants, Vice President, ASE Education Foundation will present “What Makes Technicians Leave? and How to Stop Them” at the
Kevin Looney will present “2nd Generation HEUI for International & Ford 6.7 troubleshooting and repair” for EPA 04, 07 and
Fairchild Equipment has been awarded the prestigious MVP (Most Valuable Partner) Award for its outstanding achievements in 2023 by their
The Raymond Corporation proudly announced that Jordan Taft, a welder at Raymond’s Greene, New York, facility, has won gold in
Komatsu, through its wholly owned subsidiary in the U.S., Komatsu America Corp., has agreed to acquire American Battery Solutions, Inc. (ABS),
CLARK Material Handling Company has announced the appointment of Jerry Dolan as Aftermarket Regional Sales Manager for CLARK North America.
Toyota Material Handling congratulates Jeff Rufener, the company’s former president and CEO, on being honored with the 2023 Meritorious Service Award
Houston-based Mitsubishi Logisnext Americas is now accepting applications for its 20th Annual Cat® Lift Trucks Scholarship Program. This long-standing initiative continues its
From monumental charitable donations to building bicycles for children in need for a brighter holiday season, Raymond’s network continues to
December has arrived and as we close the books on another great year, there is again uncertainty for what is
OEM’s and Lift Truck dealers have always been paying close attention to what is happening in the auto industry, thinking
Ferri Equipment is the latest East Coast construction equipment dealer to join the growing LiuGong North America dealership network. Ferri
Mitsubishi Logisnext Americas (Logisnext), a North American provider and manufacturer of material handling and innovative automation and fleet solutions, has partnered