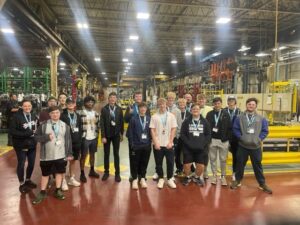
Mitsubishi Logisnext Americas hosts over 60 students at Marengo facility for National Manufacturing Day
Mitsubishi Logisnext Americas group (Logisnext), a North American provider and manufacturer of material handling and innovative automation and fleet solutions, proudly