Eagle Mark 4 names Mike Tozzi President
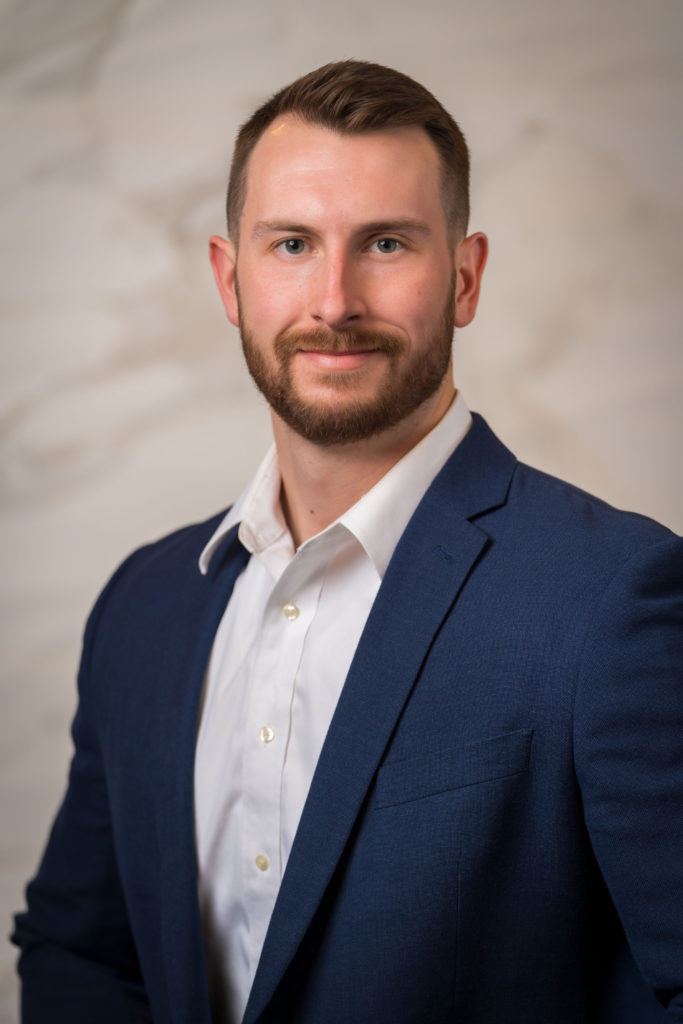
Eagle Mark 4, a supplier of Kalmar Ottawa yard trucks and exclusive parts inventory, is pleased to announce that Mike Tozzi has been named President, effective immediately. Being an energetic leader, Tozzi brings years of sales, business development, and operations experience to the position. Tozzi formerly was the acting Operations Manager at GNCO Inc., the parent corporation of multiple material handling companies across the U.S., responsible for overseeing Eagle Mark 4, Wilson Barrett, Towlift Rental, Warehouse Systems, and Trackmobile Departments. “We are excited to recognize Mike’s leadership and business development skills. He will continue strengthening relationships with employees, suppliers, customers, and partners that will lead Eagle Mark 4 to the next level,” said Matt Adams, GNCO President. “More importantly, he’s a great fit within our culture, demonstrating our vision, mission, and values both inside and outside of work.” “My goal is to ensure that the company continues to succeed and that our employees have all the support they need,” said Tozzi. “We have plans to expand our footprint out West, positioning us to better serve our customers on a national scale.” “The biggest challenge Eagle Mark 4 faces right now is keeping up with the amount of growth we have experienced both regionally and nationally,” said Tozzi, “Our success is a testament to the current employees’ efforts, and to continue to succeed, we need to further develop and support our employees as well as recruit talented new hires.” Tozzi helped Eagle Mark 4 achieve record revenue growth, including a 44.5% percent increase in year-to-date revenue in 2022 when compared with 2021, earning the Kalmar Ottawa Premier Partner award for the 2022 year. As one of the country’s largest yard truck parts providers, Tozzi managed the development and launching of Eagle Mark 4’s online B2B Parts Warehouse, yardtruckparts.com, making it possible for businesses to buy yard truck parts from the comfort of their computer or mobile device. Tozzi, 29, was captain of John Carroll University’s football team while earning a Bachelor of Science in Business Management and Leadership (’16) and holds various certificates in Leadership Development and Supervision. Tozzi was a Towlift Sales and Marketing Intern before returning as a Business Development Associate. Tozzi is a member of Beta Gamma Sigma and the Professional Gridiron Group, as well as a volunteer for the non-profit Global Empathy Now. Tozzi also serves on the board for ProtecTozz, a polycarbonate cleat guard that protects football players’ feet from injury, that he invented with his father, Dr. Mark Tozzi. In his free time, you can find Tozzi working to transition his football skills to golf, focusing on fitness, or traveling.
Big Joe hires new Strategic Products Manager
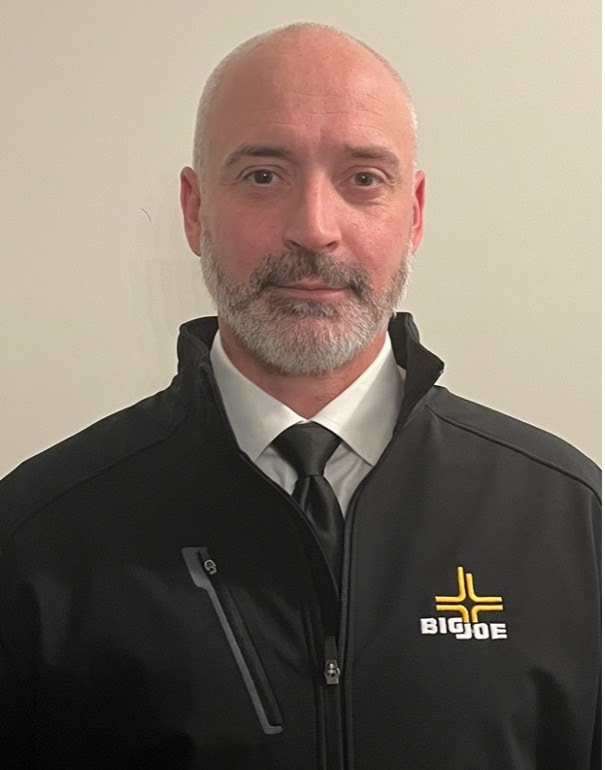
Big Joe Forklifts is also proud to announce the addition of Kurt Spyke who will serve as the Strategic Products Manager: New Products. Spyke joins the Big Joe team to build early engagement and customer experiences with new products such as the J2-192. Spyke comes to Big Joe with nearly 20 years of experience across the material handling industry. With a focus on new products, Spyke will build and develop relationships throughout Big Joe’s multichannel distribution network to enhance customer engagement, adoption, and experiences in relation to new equipment releases and new market opportunities for the company. “Joining the team at Big Joe came at a perfect time for me,” Spyke said. “I’m excited to take on a new role that will be an opportunity to grow both personally and professionally. I’m fortunate to be at the forefront of bringing our new products to market and to work with customers early on, building momentum for the future. I look forward to introducing the J2-192 to the market and providing a solution for those looking for something that allows them to improve their operations and ultimately serve their customers better.” The Big Joe J2-192 can be used with a wide range of pallet types or order-picking carts and elevates loads to 192 inches via a three-stage steel mast. In addition to enhancing productivity and driving characteristics, the J2’s dual control system enables the operator to choose a stance that improves their line of sight during travel, while staging loads, or when elevated. The J2-192 comes outfitted from the factory with a 24v industrial 340ah battery to support the run time needs of most users and features AC drive motors, an LCD programmable display, pallet clamp, and an anchor, tether, and harness system that attaches to the machine’s overhead guard.
Big Joe launches innovative J2-192 Joey Order Picker
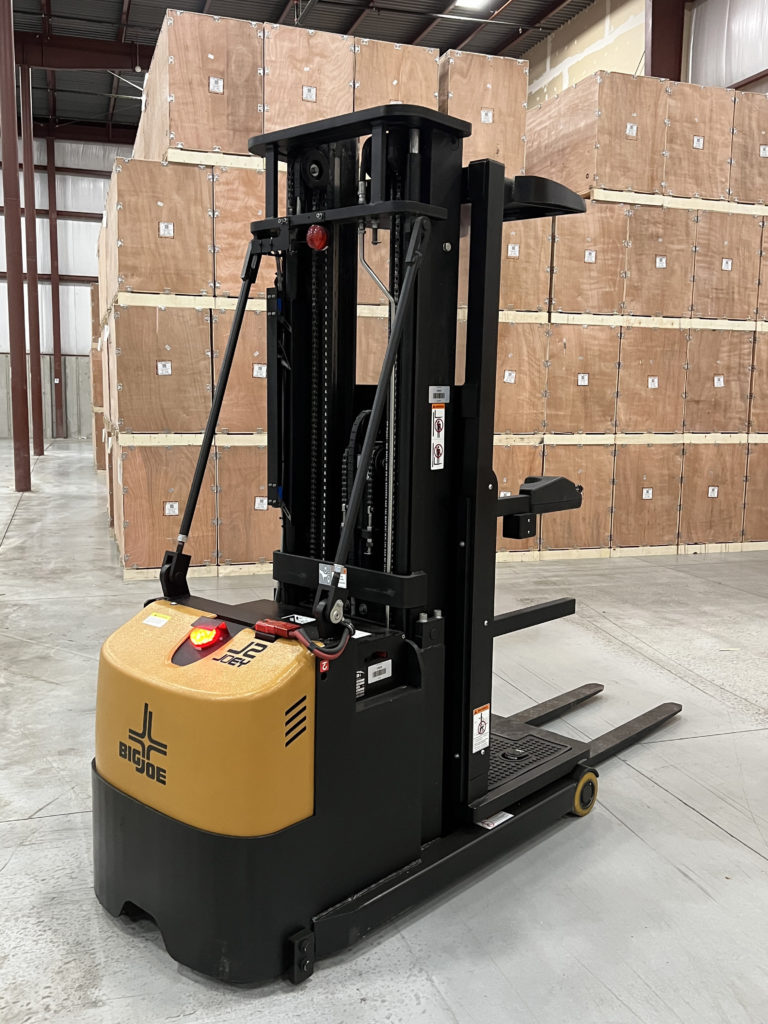
The J2-192 Joey Order Picker’s controls support forks forward or forks trailing operator stances while maintaining consistent steering orientation Big Joe has launched the J2-192 Joey Order Picker which is a versatile, safe, and productive machine; uniquely designed for order-picking operations. Available through Big Joe dealers, the J2-192 performs like no other order-picking machine on the market and expands the company’s J2 offering to reach higher heights than ever before. The primary innovation of this new Big Joe machine is that it supports both forks forward and forks trailing operator stances that can be changed on the fly while maintaining consistent steering orientation. Additionally, the J2-192, at just 36 inches wide, is highly maneuverable and has a much smaller overall footprint than full-size order pickers while still maintaining support for loads of over 2,000 lbs. The combination of these attributes allows the new order picker to deliver superior productivity in small retail aisles, urban fulfillment centers, or dense areas of the largest distribution centers. “The new Big Joe J2-192 is really a different kind of order picking machine for a different generation of supply chain needs,” said Chief Marketing Officer of Big Joe, Bill Pedriana. “As retail continues to do more local e-commerce fulfillment and distribution centers attempt to get more product variety closer to where people live, there is a huge need for a highly compact and versatile machine that is intuitive to operate. The J2-192’s dual control set-up and forks forward primary driving stance amplify the benefits of the design, and when in use… it’s fun to watch them run circles around traditional machines that were really designed for a different age.”
GNCO Inc. acquires FMH Material Handling Solutions
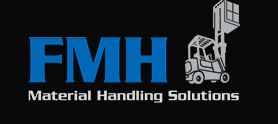
FMH Material Handling Solutions has been acquired by GNCO, Inc. effective January 1, 2023. FMH Material Handling Solutions is a business with a long history of success. We are excited to be part of its future growth story. This acquisition will make us a stronger, more diversified company geographically and strengthens our OEM partnerships” says Matt Adams, President at GNCO, Inc. FMH will remain under local management and committed to its vendors, suppliers, and customers within Colorado, New Mexico, and Texas. GNCO is committed to supporting the continued growth of FMH by providing resources and hiring top talent in the area for technicians, parts, and sales personnel. “After forty-four (44) years as a forklift distributor, John Faulkner has sold the majority of the FMH Assets to GNCO, Inc., based in Cleveland, Ohio. Faulkner became a Clark Dealer at the very young age of 27 and was the first Doosan dealer in America. Faulkner also represented Crown, CAT, Mitsubishi, Jungheinrich, Big Joe, Sellick, Kalmar, Donkey, and HELI Forklifts. in Colorado, New Mexico, Wyoming, and West Texas. Faulkner says …”The sell to GNCO, Inc. was the best move for the FMH employees, vendors, and his family”. Faulkner became the largest HELI Distribution Agent in the world in 2022. He will continue the distribution of HELI products under the name Industrial Forklifts, Inc. The HELI business is currently relocating to Phoenix, AZ. “
Doosan Infracore NA announces new CEO
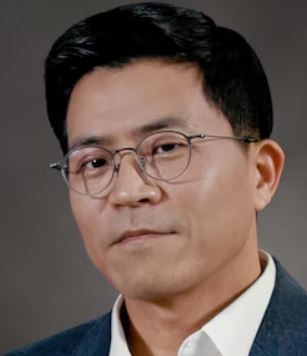
Chris Jeong was recently named the new chief executive officer (CEO) at Doosan Infracore North America. He succeeds Mr. Edward Song, the previous CEO, who was promoted to global sales head of Hyundai Doosan Infracore in Korea. Doosan Infracor North America has named a new CEO, and his first major assignment is to attend CONEXPO. Chris Jeong was named CEO, succeeding Edward Song, who was promoted to global sales head of Hyundai Doosan Infracore in Korea. Jeong most recently served as CEO of Doosan Infracore European Union. He joined Doosan in 2006 as a senior corporate strategy manager after completing his MBA at Carnegie Mellon University. He led strategic activities across various markets before he was promoted to vice president of sales and marketing for emerging markets. Jeong oversaw sales and marketing for Doosan employee teams in Asia, Oceania, the Commonwealth of Independent States, the Middle East, Africa, Latin America, Brazil, and India. “I’d like to acknowledge the many accomplishments of Doosan Infracore North America under the leadership of Mr. Edward Song,” Chris said. “Edward was instrumental in getting the new organization structured in 2018 as we recommitted the company to the heavy construction equipment industry in North America.” Song helped establish two regional parts distribution centers in North America, opened a machine customization plant in Savannah, Ga., and most recently introduced the new Doosan machine monitoring center at the corporate office in Suwanee. “It has been my pleasure serving you and your customers over the last five years, and I look forward to continuing to support the company and our products in my new role,” Edward says. “Much has transpired since 2018, and I’m pleased by the progress we’ve made working together to enhance the Doosan brand and grow the product line in North America.” Song praised Jeong’s leadership. “Chris will continue building on the strong foundation we’ve established, particularly the growth during the last five years,” confirms Edward. “His experience and insight will help us continue to move the company forward and expand our footprint in North America.” Jeong’s first major assignment will be to oversee the Doosan exhibit at CONEXPO-CON/AGG 2023 in Las Vegas from March 14-18. “I’m excited about our Doosan exhibit planned for the outdoor Festival Grounds,” he says. “We will be demonstrating our latest developments on Concept-X and autonomous equipment with live demonstrations throughout the day. We will have a full lineup of our current products as well as new additions to the lineup.”
The Gold Standard: Toyota Material Handling’s Kim Douglass becomes first woman to medal in TMHG Global Skills Challenge
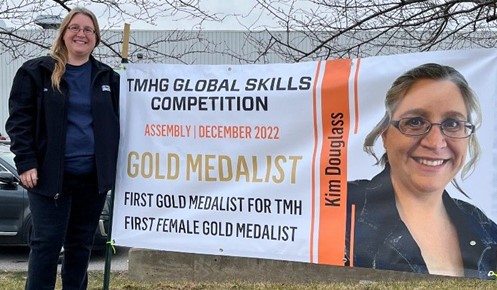
Kim Douglass, a Toyota Material Handling (TMH) associate, made history by becoming the first woman to ever place in the Toyota Material Handling Group (TMHG) Global Skills Competition, earning a gold medal in the ‘Assembly’ category during the annual international competition held last month in Takahama, Japan. Douglass beat competitors from other Toyota group companies based in China, France, Italy, and Sweden, as well as additional U.S. participants from The Raymond Corporation. “We couldn’t be prouder of Kim’s significant achievement and the way she represented Toyota Material Handling in this intense global competition,” said Tony Miller, TMH Senior Vice President of Engineering, Operations & Strategic Planning. “Kim never strayed from our core values and always approached the competition with respect and humility.” Douglass, who has been with Toyota for 13 years, participated in TMH’s internal competition and was eventually selected as the company’s representative for the ‘Assembly’ category. From there, she challenged competitors from Raymond’s Greene, New York, and Muscatine, Iowa factories in a regional competition prior to the big show in Japan. Douglass spent a full year in TMH’s training department as she prepared for the competition, practicing for several hours every day while also helping train others in the dojo area. It culminated in the nine-day trip to Japan last month – Douglass’ first trip outside of the U.S. When it was finally time for the big day, Douglass did her best to calm the nerves. “My thought was ‘This is just practice.’ I’m at home practicing.’ I kept saying it over and over to myself for three days,” Douglass said. “At one point, I glanced at the Japanese representative competing next to me, and I was like, ‘Nope, I can’t even look at him. I have to focus on my work only.’” Douglass finished assembling the plates in 3 minutes and 16 seconds and completed the torquing portion in eight minutes to earn the gold – much to her surprise. “I looked at my coach and said ‘Really!?’” Douglass recalls. “I did not expect to win. I was hoping to at least place, but I did not plan on winning gold.” Douglass said dozens of people congratulated her on the win – including many women sharing that they feel a sense of ‘girl power’ as a result of her achievement. But Douglass’ most memorable interaction came from a fellow competitor – Paige Frantz, a female representative from Raymond Muscatine who finished third. The duo developed a bond during the regional competition that continued as they pushed each other to get better. “She told me right from the beginning, ‘You’re going to place.’ When I got done, the first thing she did was hug me and said, ‘I knew you were going to do it … I knew you were going to win this.’ That was really meaningful to me. We’re all in this together, and I was so happy that she placed too. “One of the things I realized when we went through the tour in Takahama was there were not many women on the lines. So the fact that we’re showing everyone that women can do it – it’s awesome.” Douglass’ win is a testament to TMH’s industry-leading reputation of dedication to innovation, quality and service. The full-line material handling solutions provider and North America’s leading manufacturer of forklifts maintains a constant focus on delivering the highest quality and believes in the concept of ‘Kaizen’, or continuous improvement, in every aspect of its business. One area of improvement that TMH is especially focused on is encouraging more women to pursue a career in the material handling industry which makes Douglass’ win even more significant for the organization. The Toyota Women’s Impact Network, or T-WIN, plans to use Douglass’ achievement as a tangible example of what they hope to see more of in years to come. “Kim’s achievement is more than just a win for TMH or even for Toyota; it’s a win for all women in the material handling industry,” said Tracy Stachniak, TMH Vice President of Human Resources, Training & Development. “We are committed to supporting and promoting diversity and inclusion in every way we can. Kim’s gold medal says one thing loud and clear – women can do it, too.” The company celebrated Douglass’ gold medal with a special campus-wide day in her honor – coined Kim Douglass Day – complete with congratulatory signs and banners, a cafeteria offering based on her favorite meal, and gold cookies with red, white and blue ribbons attached to them. “The big thing I learned through this whole experience is just not to be afraid,” Douglass said. “I never entered the skills competition before out of fear. I didn’t know what to expect, so I didn’t do it. Ultimately, I decided to go for it because I feel like I’m good at assembly and felt like if I didn’t try, I was going to regret it. I’m so happy I did. I’m going to apply that mindset to other parts of my life and continue to take chances on myself. “I’m so thankful for everyone that supported me throughout this process, especially my coach Matt Heuer for always encouraging me to do my best.”
Casey Equipment joins LiuGong North America Dealer lineup
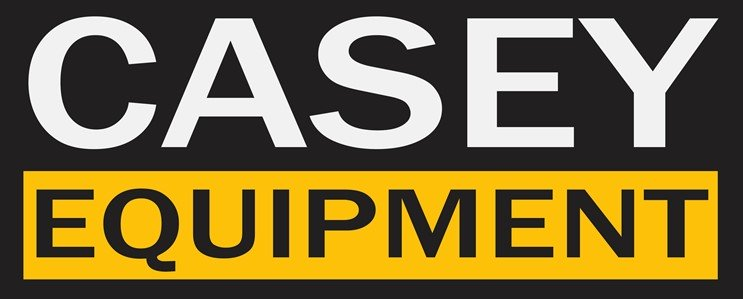
Casey Equipment is the latest Midwest dealer to join the rapidly expanding LiuGong North America dealership network. Leaders of the third-generation family-owned business said joining the lineup has been a smooth, straightforward process because of stellar communication and planning from LiuGong. The initial launch of LiuGong products at Casey Equipment went “virtually flawlessly with all of their support.” “From day one, we knew exactly who to contact for our initial needs and requirements,” said Jim Cox, Casey Equipment President. “We also felt confident that everyone from their president and CEO on down was engaged in getting us started on the right foot.” Casey Equipment is headquartered in Chicago, Illinois with three dealerships in Arlington Heights, Lemont, and Rockford. The company has served the Chicago and northwest Indiana areas for more than 45 years. In addition, to support, Cox said machine and parts availability played a major role in joining the LiuGong dealership network. While competitors have struggled with supply chain issues, LiuGong has worked tirelessly to fill their customers’ orders. “LiuGong seems to have it figured out better than most of the competitors out there,” he said. “We can quote, take orders and more importantly deliver equipment timely for our customers.” Casey Equipment is a premier dealer of new and used heavy equipment in the construction, forestry, asphalt paving, mining, and agricultural industries. They provide construction equipment rentals, services, and parts for the brands they carry. LiuGong North America President Andrew Ryan said Casey Equipment has a stellar reputation as a heavy equipment dealer in the Midwest, and they are thrilled to work together and expand their offerings in the region. “We are incredibly grateful to add another great partner in Casey Equipment to our growing dealer network,” he said. “Their reputation for excellence in Illinois and Indiana will be integral to improving our reach in the region.”
KION North America announces new partnership with Advanced Material Handling Systems
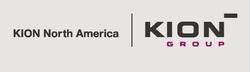
KION North America has appointed Advanced Material Handling Systems as a dealer partner within the KION North America dealer network. Advanced Material Handling Systems is authorized to sell Linde Material Handling and Baoli brands within its three locations in Atlanta, Georgia; Suwanee, Georgia; and Augusta, Georgia. “We are incredibly proud to announce our new partnership with Advanced Material Handling Systems,” said Director of Dealer Development, Rick Schiel. “We have strategically sought out dealers to join our dealer network who are committed solutions providers focused on expansion and growth. We are thrilled to have Advanced Material Handling Systems represent the Linde Material Handling and Baoli brands.” Advanced Material Handling Systems represents over four decades of market-leading experience in the material handling industry. With this organization’s long history of being a trusted solutions provider for its customers, Advanced Material Handling Systems is proud to offer enhanced offerings of the Linde Material Handling and Baoli brands throughout Georgia. This deliberate focus includes establishing Advanced Material Handling Systems as a separate entity with dedicated sales management and salespeople representing the KION North America product portfolio at their sites.
Atlantic Lift Truck announces expansion of its Wholesale Forklift Division
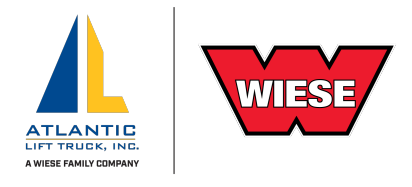
As part of the Wiese USA family of companies, Atlantic Lift Truck (ALT) is expanding its Wholesale Division with the creation of a Western States Wholesale Territory. After 45 years in the industry, founder and past ALT CEO/President, Glenn Baer will be developing the new territory. According to Glenn, “I’m having too much fun to retire, and I want to keep my brain active. What better way to have fun than to help forklift dealers of all sizes increase their Used Equipment revenue and Gross Profit!”
Fraza Sister Company Material Handling Group USA acquires Liftec Inc.
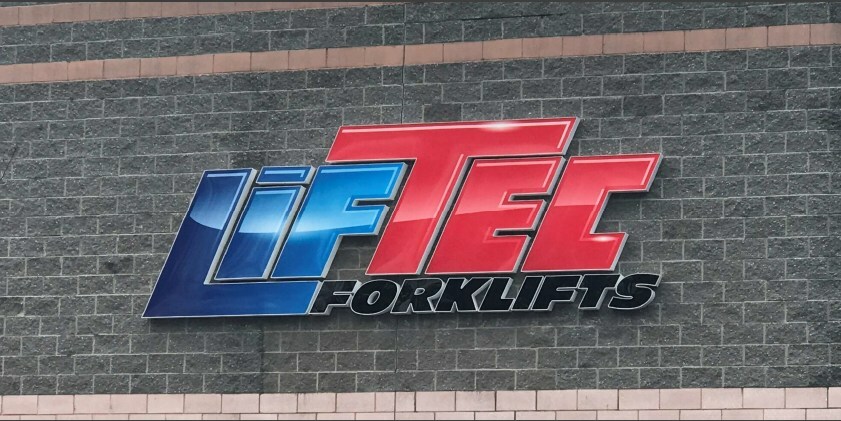
Fraza, a material handling equipment and solutions provider headquartered in southeast Michigan, announced its sister company, Material Handling Group USA (MH Group USA) has acquired Liftec, Inc. as a new dealer/location on the East Coast. Liftec is a proud dealer for Linde Material Handling, Baoli, Doosan, and UniCarriers. “An important strategy for our business is diversification, and geographic expansion is part of that strategy,” said Fraza and MH Group USA CEO and Owner Roger Runyan. “Bringing Liftec on board aligns with our mission to be the best service organization, period. This acquisition allows us to strengthen our relationships with key vendors and provide a greater support network to our customers. We also look forward to the expertise and knowledge their team will bring to our organization.” This expansion takes Fraza and MH Group USA’s operations outside of Michigan for the first time. The newly acquired business will continue operating as Liftec, but the team of 35 employees is now under the leadership of Runyan. Liftec has been in business for over 45 years serving the New York, New Jersey, and Pennsylvania metro areas with high-quality forklifts and material handling products and services. The Liftec acquisition also diversifies Fraza and MH Group USA’s market outside of automotive and into chemical manufacturing, which currently leads all industries, as well as major distribution centers for national and worldwide companies. Liftec’s diverse customer base will allow Fraza and MH Group USA to expand their market share of class I, II, and III material handling products.
HUBTEX FluX Sideloader is 360° steering on three wheels
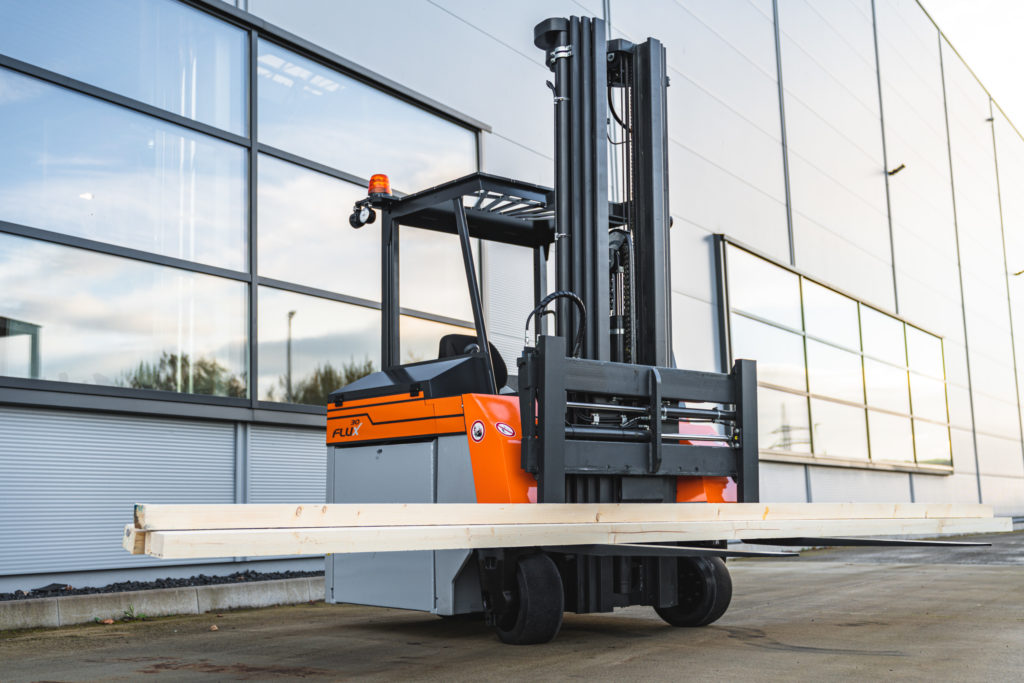
HUBTEX has given its FluX electric multidirectional counterbalance forklift truck an update. The latest generation for load capacities of up to 3 tons is making its debut at LogiMAT 2023. Visitors to Stand 10B20 in Hall 10 at the LogiMAT trade fair will be able to see the new central drivers’ position, which provides a higher-up all-around visibility compared to its predecessor. Additionally, the patented 360° HX steering has been added to the compact three-wheel running gear for the first time, ensuring smooth changes in direction from longitudinal to transverse travel. The new generation of HUBTEX’s FluX handles both pallet and long-load transport in a single vehicle. This hybrid used as a front and sideloader makes the new 3T FluX 30, suitable for a wide range of sectors, from the timber and metalworking industries to the building materials trade. HUBTEX has moved the driver’s cab to the middle of the vehicle giving the operator a better all-around view, including toward the load being carried. This improved visibility is enhanced by the vehicle’s new, more compact dimensions which include a new mast tilt feature. Being up to 20% smaller, the FluX is more maneuverable and agile too. The innovative design has made access to individual components, making them easier to access for servicing and programmed maintenance. Powerful and maneuverable – for both indoor and outdoor use The switch from a four to a three-wheel running system has done nothing to impair the features that people have come to expect from HUBTEX in terms of ergonomics and freedom of movement. For instance, the new FluX has retained the spoked steering wheel and joystick for user-friendly operation as well as the spacious driver’s cab, providing the operator with greater comfort, for those jobs that can end up taking a little longer. In addition, the patented HX steering has been developed further to enable it to be fitted to all HUBTEX electric vehicles with a three-wheel running system. The HX steering mechanism permits smooth transitions between steering modes, thus reducing tire wear. Operators can also wave goodbye to time-consuming and fiddly maneuvering, resulting in fast throughput times. Furthermore, the compact multidirectional truck is ideal for combined indoor and outdoor use in the warehouse thanks to its soft elastic tires and a maximum speed of 12 km/h, while its large battery (48 V, 930 Ah) means it can go on for more than a whole shift. An optional lithium-ion battery provides very quick charging supporting its use in a multi-shift operation.
Toyota Material Handling Solutions supports The Foodbank of Southern California
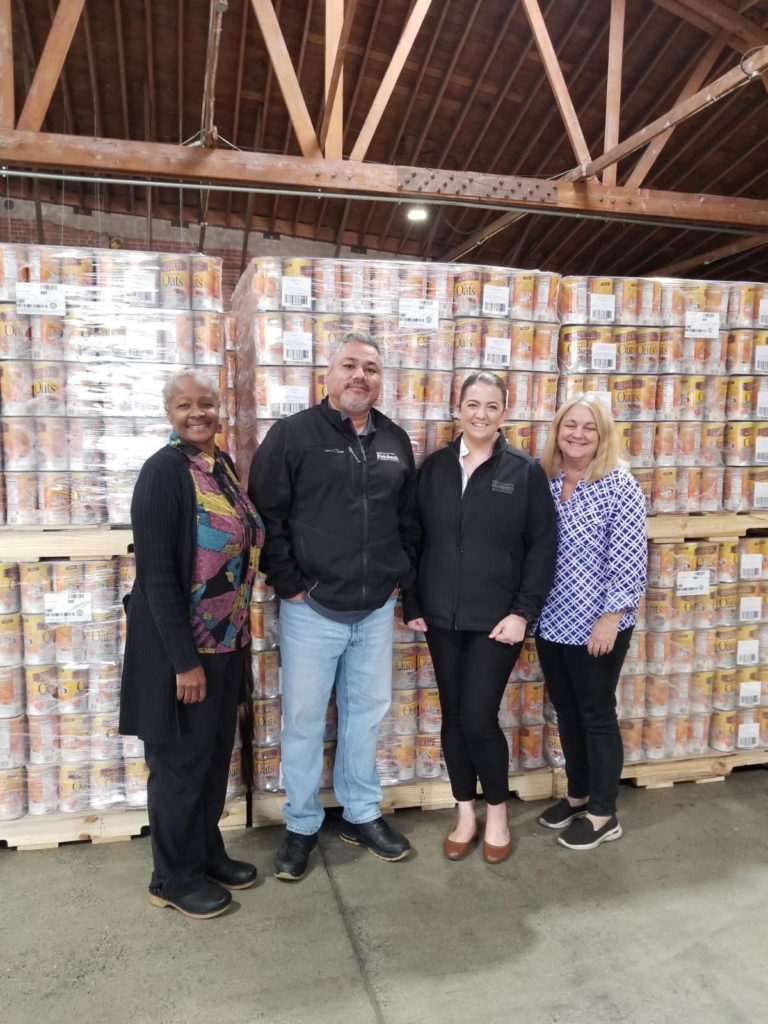
Toyota Material Handling Solutions (TMHS) announced its donation of $2,500 to The Foodbank of Southern California today. TMHS associates also collected 500 pounds of canned goods to accompany the cash donation. “Supporting our local food bank is a tradition here at TMHS,” said TMHS President & CEO Dr. Shankar Basu. “With food insecurity a big concern for many families, it is gratifying to know we’re helping provide healthy food choices to the poorest communities in Los Angeles.” The Foodbank of Southern California supports vulnerable children, families, and seniors in the community who have nowhere else to turn to for help. “We are incredibly grateful for our corporate donors, especially companies like TMHS who give back year after year,” said Jeanne Cooper, president of The Foodbank of Southern California. “Corporate food drives and monetary donations help us achieve our mission to ensure that no individual goes hungry in Los Angeles County, not even for a single day.”
Quinn Lift adds to its sales team
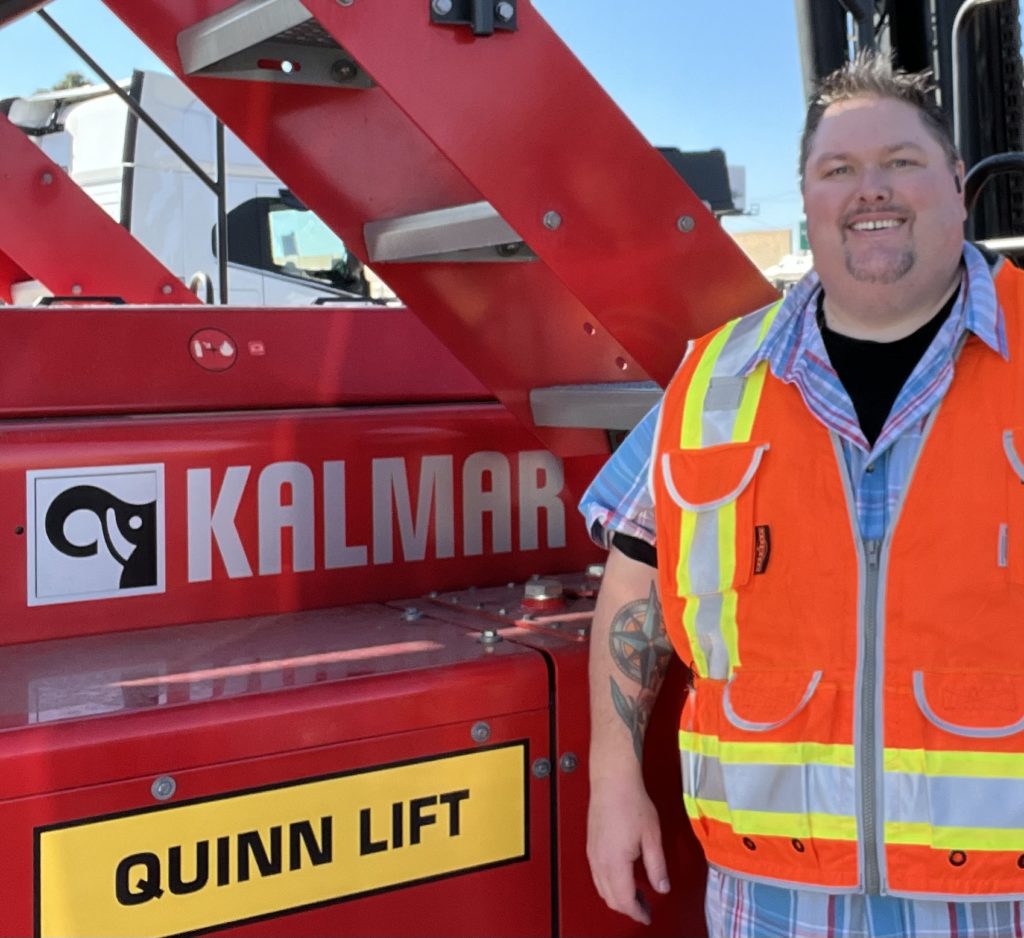
Quinn Lift has announced the addition of Kalmar Specialist Henry “Hank” Ansley to their sales team. Hank’s focus will be to grow the newly added Southern California counties of Los Angeles, San Bernardino, Orange, Riverside, Imperial, and Yuma county in Arizona. Quinn Lift’s sales manager Aaron Gallyer states, “Quinn Lift and Kalmar have been partners in central California for over 20 years and this territory expansion has allowed us to stock and rent a larger variety of 20k and uplift trucks”.
H&E opens new branch in Palm Bay area
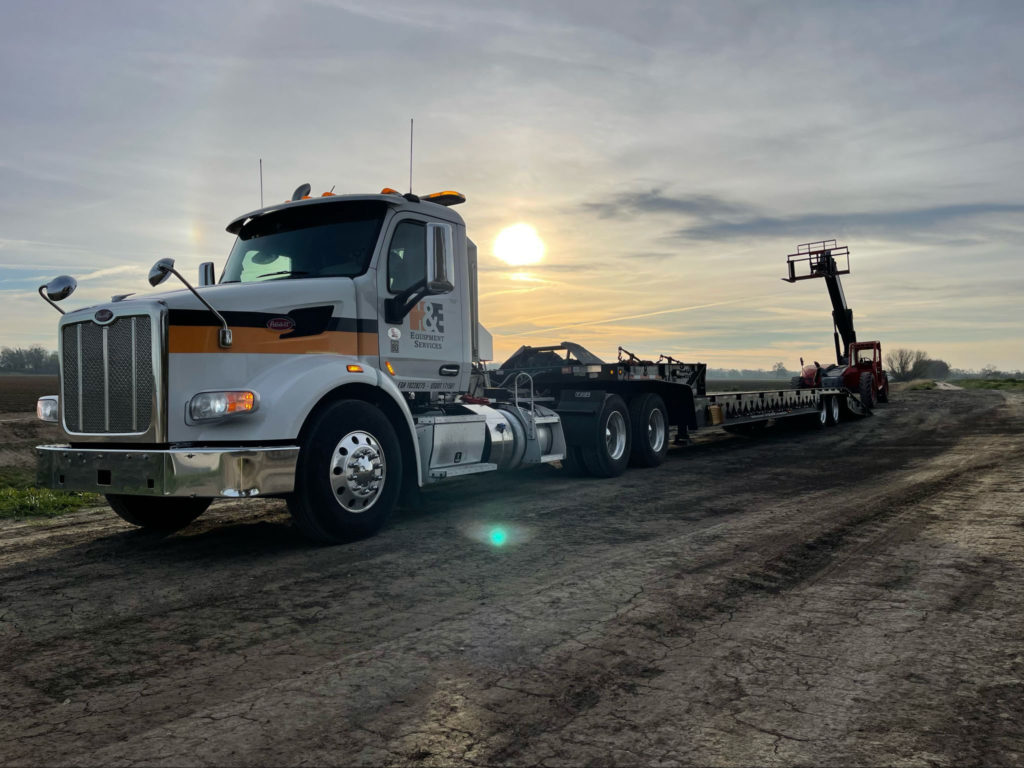
Effective December 22, 2022, H&E Equipment Services Inc. (H&E) announces the opening of its Palm Bay rental branch, its 12th in the state of Florida. The branch is located at 6625 Babcock St. SE, Malabar, FL 32950-5017, phone 321-294-6100. It includes a fully fenced yard area, offices, and a separate repair shop and is capable of handling a variety of construction and general industrial equipment for customers along Florida’s Space Coast. “H&E is expanding throughout Florida and has opened four new branches in the state in just this year alone. With the addition of this newest branch on the Atlantic coast, our Palm Bay location creates a service triangle with our existing Orlando and Lakeland branches to effectively locate the fleet to fill any customer need. We can also better reach our customer base in Cocoa Beach, Melbourne, Palm Bay, Vero Beach, and all along the coast of Central Florida with our close proximity to I-95,” says Branch Manager Stephen Bone. “In the next five years, this area will see nonresidential construction increase to the tune of over $9 billion, and we will have a good mix of equipment available to serve any project. We plan to grow right along with our customers.” The Palm Bay branch specializes in the rental of aerial lifts, telescopic forklifts, earthmoving machinery, compaction equipment, generators, compressors, and more and represents the following manufacturers: Allmand, Atlas Copco, Bomag, Case, Club Car, Cushman, Doosan, Gehl, Generac Mobile, Genie, Hilti, Husqvarna, JCB, JLG, John Deere, Kubota, LayMor, Ledwell, Lincoln Electric, Link-Belt Excavators, MEC, Miller, Multiquip, Polaris, Skyjack, SkyTrak, Sullair, Sullivan-Palatek, TAG, Taylor, Towmaster Trailers, Wacker Neuson, Yanmar, and others.
Yale honored for lift truck technologies designed to support safety, productivity and sustainability
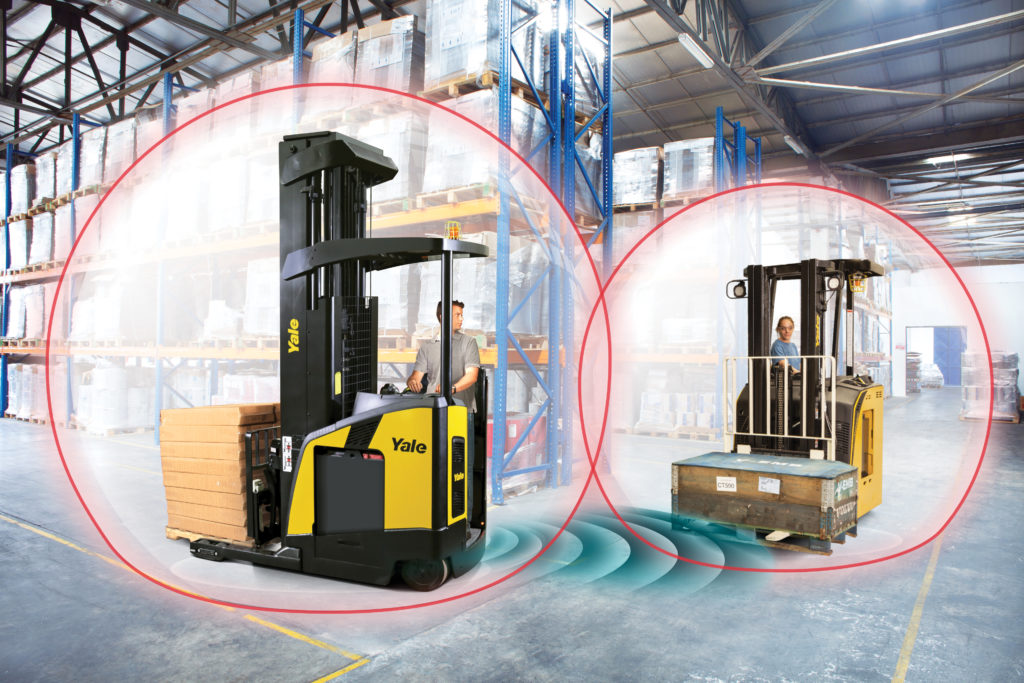
Yale Materials Handling Corporation has been named a 2022 Top Software and Technology Provider by Food Logistics magazine. The lift truck manufacturer provides a variety of technology solutions designed to meet the challenges of modern warehousing, including the industry’s widest range of lift truck motive power sources and a first-to-market suite of lift truck operator assistance technologies. The win marks the seventh consecutive year Yale has earned this recognition from Food Logistics, and the company’s eighth win overall. “Today’s warehouses are challenging environments, facing intense operational and business demands,” says Brad Long, Brand Manager, at Yale Materials Handling Corporation. “Employee turnover and inflation continue to put pressure on businesses, all while they pursue reductions in carbon emissions. Technology can play a key role in addressing these challenges, and our objective is to be the trusted collaborator for customers that need to find the right technology to meet their needs.” The Yale lineup of lift truck technologies includes: Yale Reliant is a suite of operator assistance technologies designed to help support lift truck safety best practices that can help limit the risk of incidents like crashes or tip-overs by enhancing operator and pedestrian situational awareness. It automatically adjusts truck performance like travel speed or hydraulic functions based on the stability of the truck, facility rules, and proximity to obstacles, people, and other trucks. The solution was developed to support a customer’s focus on operator safety and is the result of more than 40,000 hours of research and development. Robotic lift trucks are engineered to automate both horizontal and vertical storage workflows. These trucks can help warehouses to reduce both labor dependency and turnover by automating and optimizing workflows, enabling operations to reassign workers to value-added tasks. Advanced electric power solutions that produce zero harmful emissions, such as lithium-ion batteries and hydrogen fuel cells. Yale also offers models designed from the ground up around the slim form factor of a lithium-ion battery pack – not just an aftermarket retrofit – offering superior performance and ergonomic advantages. Yale Vision is a telemetry solution that provides warehouse managers with real-time data to manage the day-to-day operation of their lift truck fleet. Insights include equipment diagnostics, utilization data, impact detection, and more. Sensor-enabled ergonomic features include the Operator Sensing System, which allows operators of stand-up lift trucks the freedom to comfortably adjust their stance and operate the truck without having to continuously stand on a pedal. Advanced ergonomic features are meticulously designed around the operator to help reduce fatigue for greater efficiency and productivity throughout their shift. The annual Food Logistics Top Software and Technology Providers list honors leading software and technology providers that ensure a safe, efficient, and reliable global food and beverage supply chain. For more information on the 2022 list, click here.
Toyota Material Handling formalizes partnership with unique nonprofit Anchor House
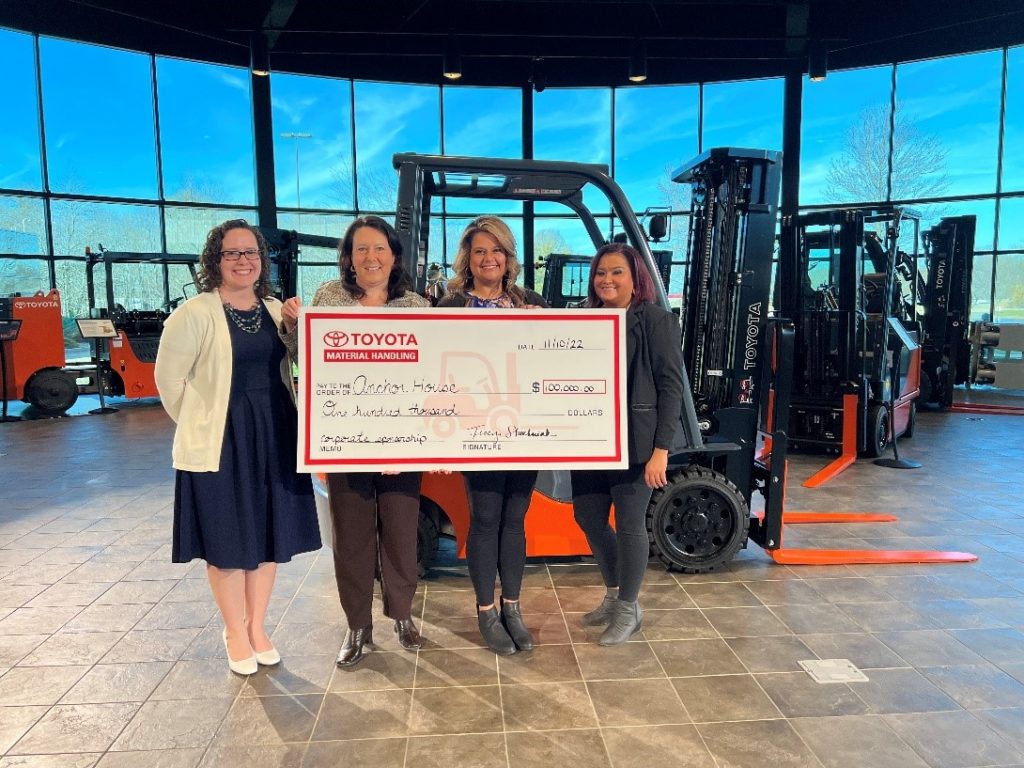
Toyota Material Handling (TMH), a manufacturer of forklifts and provider of a range of material handling solutions, announces a new partnership with Anchor House, a local nonprofit that focuses on investing in Jackson County residents through housing, employment resources, and nutritional assistance. Anchor House is the only homeless assistance program serving the local community, offering two emergency shelters and the largest food pantry in the area. “Toyota Material Handling is proud to partner with this local organization that has an impact on so many families and individuals in our community,” said Tracy Stachniak, TMH Vice President of Human Resources. “Anchor House is a staple in the community, and we are proud that this partnership will allow the shelter to broaden the ways they assist those in need.” Toyota’s commitment through this partnership includes $100,000 in financial support to Anchor House to be paid over the next four years. The company is also providing in-kind donations to meet needs that arise for Anchor House and its beneficiaries, such as non-perishable food or business and interview attire. TMH employees will have unique opportunities to make a difference by volunteering for the organization to provide shelter maintenance and food pantry donations. The partnership also includes support for Anchor House’s self-sufficiency program with Toyota providing employment skills training to residents involved in the program. The training includes but is not limited to interview skills, resumé writing, and application completion assistance. Through this program, TMH is helping develop a sustainable employment track for Anchor House families. “The growing need for our services in the community has been evident by the increased need for food and shelter we’ve continued to experience. Now more than ever, our friends and neighbors need our assistance,” said Anchor House Executive Director Megan Cherry.“With the growing need, we rely on vital partners like Toyota to help us with our important work. This allows us to meet those needs and ensure that no one is left in the cold or hungry. “We couldn’t be more grateful that Toyota has come alongside us to provide volunteers, hard work, and financial support to our mission. Toyota is one of our biggest champions and supporters. We are able to continue to meet the need because of this great partnership and work they support.” In 2022, Anchor House provided more than 10,500 nights of shelter to citizens in need and served over 14,000 people through its food pantry. The organization has continuously served the Jackson County community for over three decades and partners with multiple organizations in the area to provide holistic support for those with immediate and long-term needs. Learn more about Toyota Material Handling’s culture of volunteerism by clicking here or by visiting toyotaforklift.com.
Yale empowers operations to set their own standard with highly configurable new lift trucks
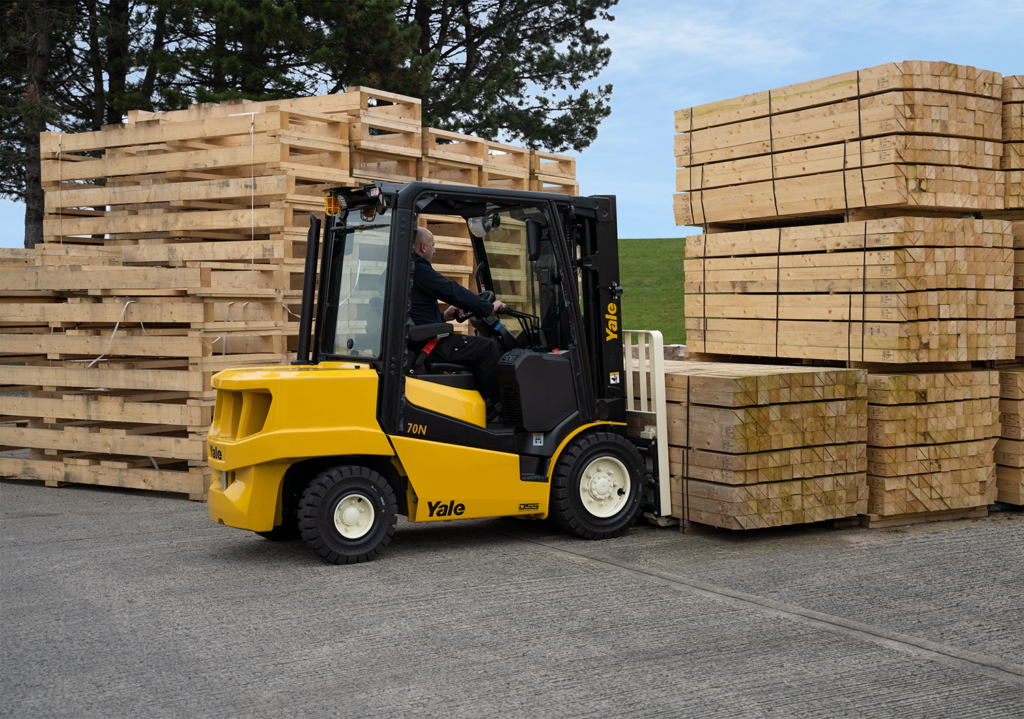
Yale Materials Handling Corporation rolls out the first lift trucks in its new Series N lineup with the introduction of counterbalanced models available in the 4,000-to-7,000-pound capacity range. Built on a scalable platform, not only does the Yale® Series N offer strong productivity, operator ergonomics, and a low total cost of ownership, it allows material handling operations to option up based on their unique needs. “Cost pressures and labor shortages are testing the ability of operations to balance profitability with productivity,” says Brad Long, Brand Manager, Yale Materials Handling Corporation. “Equipment can be part of the solution, but the one-size-fits-all forklift approach of yesteryear won’t cut it. The Series N gives warehouses and retail operations the freedom to dial the trucks to their own standards to meet the needs of their operators, application, and business challenges.” The configurability of the GP40-70N models does not come at the expense of comprehensive standard features: Operator-centric design – A large, strategically located step, generous grab handle, and contoured hood make it easy for the operator to get on and off the truck. A spacious compartment with easily adjustable controls helps operators stay comfortable and productive all shift. Enhanced visibility – The low dash and wide mast help enhance the visibility of the fork tips and load when picking, placing, or traveling forward, helping support operator awareness, confidence and efficiency. Safety and productivity – Standard on all Series N trucks, the innovative Dynamic Stability System (DSS) provides automated alerts and assistance to operators by implementing truck performance limitations in real-time to help minimize forward and sideways tip-overs*. Low total cost of operation – Start with custom configuring the right truck at the right price, then durable components and extended service intervals to help minimize downtime and reduce maintenance costs over the life of the equipment. The GP40-70N can be ordered with optional operator assistance systems designed to further support operator and pedestrian awareness, and help prevent facility and product damage in specific applications. These technologies include a rear-facing camera and rear-view display, spotlights and pedestrian awareness lights, and pre-set lift height selector.
Mitsubishi Logisnext Americas opens applications for the 19th annual Cat® Lift Trucks Scholarship Program to support the next generation of industry leaders

Houston-based Mitsubishi Logisnext Americas, one of the world’s leading manufacturers and providers of material handling, automation and fleet solutions, announced today the call for applications for its 199th Annual Cat® Lift Trucks Scholarship Program. Each year, the scholarship program honors an outstanding Houston-area high-school senior interested in pursuing a four-year degree related to the material handling industry. This year’s winner will be awarded a $5,000 scholarship to go towards their higher education. “We’re proud to announce this year’s Cat Lift Trucks scholarship program,” said Ken Barina, president of Mitsubishi Logisnext Americas. “Each year, we are continuously impressed by the academic achievements and dedication to community service of our scholarship applicants. We hope this program will continue to drive new opportunities for students pursuing higher education, and also help support and inspire the next generation of future leaders.” Since its launch in 2005, the Cat Lift Trucks scholarship program has awarded $135,000 in educational assistance to 26 Houston-area students. Past scholarship recipients have enrolled at Texas Universities and colleges, including Texas A&M University, The University of Texas at Austin, and Texas State Technical College, pursuing degrees in various fields such as mechanical and chemical engineering, welding technology, and entrepreneurship. Recipients are selected based on their academic performance, commitment to community service, demonstration of leadership abilities, and financial need. As the Official Lift Truck Provider of the Houston Livestock Show and Rodeo™ (HLSR), Cat Lift Trucks will announce the winner of the 2023 scholarship during the annual HLSR event, taking place February 28 – March 19, 2023, in Houston. “We’re honored to serve as a sponsor for the Houston Livestock Show and Rodeo and to be a part of its 90-year commitment to Texas youth and education,” said John Sneddon, executive vice president, Sales and Marketing, at Mitsubishi Logisnext Americas. “Initiatives such as the Cat Lift Trucks scholarship program are vital to helping inspire the future of manufacturing and business.” Applications for the 2023 Cat Lift Trucks scholarship must be submitted online by 11:59 p.m. CST on January 31, 2023. Finalists will be notified by February 10, 2023, and a winner will be selected by February 24, 2023. Applicants must be from a Houston-area school district and plan to enroll in a college, university, or technical school in Texas with a focus on engineering or a business-oriented or technical trade field related to the material handling industry. For more information on this year’s scholarship program and requirements, or to apply, visit https://www.logisnextamericas.com/en/cat/cat-lift-trucks-scholarship.
Big Joe returns to the Canadian market
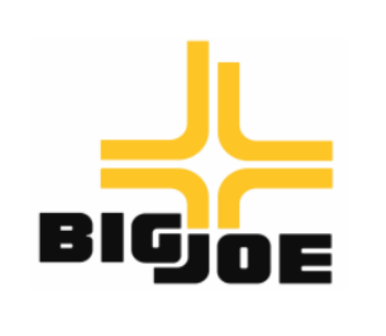
Big Joe Forklifts will re-enter the Canadian market effective Jan. 1, 2023 Big Joe Forklifts has announced its plan to return to the Canadian market for the first time since 2009 through the newly formed Big Joe Canada. The initial launch will ensure Big Joe equipment is readily available through a network of material handling dealerships across most Canadian provinces with whom Big Joe Canada has already partnered. This network will continue to grow to ensure that support for the Big Joe product line is second to none as it continues to expand into new market segments including lithium-powered sit-down forklifts and autonomous vehicles over the years to come. Big Joe is one of the fastest-growing companies in the lift truck industry globally, having grown by more than 1200% since 2009. Big Joe’s success has been driven by rapid product development resulting in a robust portfolio of innovative purpose-built machines that better address contemporary material handling needs than its competitors. As supply chains have adapted and evolved to support changes in consumer behaviors, Big Joe has been able to use this speed to market to enhance productivity, safety, and efficiency in operations as far ranging from heavy manufacturing to retail. The company’s electric forklifts, pallet trucks, walkie stackers, and access vehicles use the latest in human factors, lithium batteries, and motor technology to propel its simple philosophy – move more, hurt less. Big Joe is excited to team up with the newly formed Big Joe Canada to re-enter the Canadian market. Big Joe Canada will launch by onboarding dealers from its existing network across Canada before expanding this network. The expansion plan will include ensuring that dealers can expertly deploy products, services, parts, and warranties to ensure a high level of customer satisfaction across Canada. “The Canadian market is very important to Big Joe, and we have been working hard to find the right partner that shares our growth vision and can help us re-enter the market at the right time. On that point, we couldn’t be more pleased or excited to partner with Big Joe Canada to make that happen,” said Bill Pedriana, Big Joe’s CMO. “With an industry that continues to rapidly evolve due to emerging technologies and economic uncertainty, companies are looking to keep their operations moving by partnering with organizations that can be nimble and responsive to meet their changing needs. For us, the timing couldn’t be better to rejoin the Canadian market and offer our unique equipment solutions to help keep commerce moving forward during this dynamic time.” “Big Joe Canada is excited to expand with Big Joe to offer exceptional material handling solutions to our existing and future network of dealers across Canada,” said Ace Coustol, Regional Vice President, of Big Joe Canada. “Both entities are driven to provide products specific to our customer’s needs, reducing costs and downtime, and boosting efficiency. Joining forces in the Canadian market will allow us to streamline products and services to our valued customers and we look forward to expanding our tailor-made offerings.”
H&E opens new branch in Ocala Florida
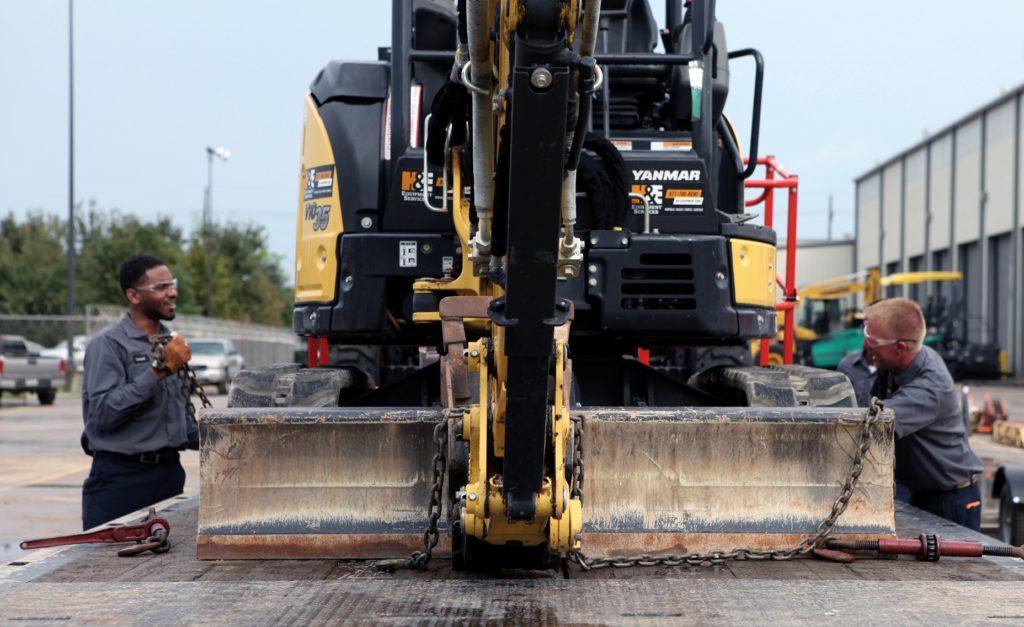
Effective December 13, 2022, H&E Equipment Services Inc. (H&E) announces the opening of its Ocala rental branch, its 11th in the state of Florida. The branch is located at 1800 NW 58th Lane, Ocala, FL 34475-3042, phone 352-644-9700. It includes a fully fenced yard area, offices, and a separate repair shop and is capable of handling a variety of construction and general industrial equipment for customers in Central Florida. “Our new Ocala branch fills a geographic gap in the central and northern parts of the state for us. We can now better reach our customer base between our existing Jacksonville and Orlando locations, and having a facility along the I-75 corridor gets us on the job site quickly. Steady population trends and other favorable economic conditions in the area point to a strong, long-term nonresidential construction forecast, and we have the equipment to effectively serve those projects,” says Branch Manager Jim Sill, who has worked in the area and in the industry for more than 30 years. “H&E has been in the Sunshine State for 20 years now and has one of the youngest fleets in the industry. That is a great combination to show our customers—new and existing—that we are here to stay and ready to grow with them.” The Ocala branch specializes in the rental of aerial lifts, telescopic forklifts, earthmoving machinery, compaction equipment, generators, compressors, and more and represents the following manufacturers: Allmand, Atlas Copco, Bomag, Case, Club Car, Cushman, Doosan, Gehl, Generac Mobile, Genie, Hilti, Husqvarna, JCB, JLG, John Deere, Kubota, LayMor, Ledwell, Lincoln Electric, Link-Belt Excavators, MEC, Miller, Multiquip, Polaris, Skyjack, SkyTrak, Sullair, Sullivan-Palatek, TAG, Taylor, Towmaster Trailers, Wacker Neuson, Yanmar, and others.