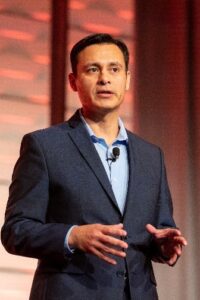
Toyota Material Handling promotes Jimenez to Vice President
Longtime Toyota leader to oversee Regulatory Affairs, Product Planning, & Product Assurance Toyota Material Handling (TMH) has recently announced the
Longtime Toyota leader to oversee Regulatory Affairs, Product Planning, & Product Assurance Toyota Material Handling (TMH) has recently announced the
Briggs Industrial Solutions, a Sammons Industrial company, announced Mark Piccirillo as the new Chief Financial Officer. A proven strategic leader,
Five parks each receive $50,000 for park restoration, beautification or enhancement needs and a new Bobcat zero-turn mower Bobcat Company,
LiuGong North America has welcomed Defatte Equipment Inc. to its material handling dealer network. Located in the northern coastal area
Effective July 17, 2023, H&E Equipment Services Inc. announces the relocation of its Winston-Salem branch to Greensboro, N.C. The new
Big Joe’s new CB30/CB35 Walkie Stackers offer a next-gen alternative to sit-down forklifts Big Joe Forklifts has officially introduced the
On National Hire a Veteran Day on July 25, Carolina Handling will launch an online auction to raise funds for
Alta Equipment Group Inc. (NYSE: ALTG) (“Alta” or the “Company”), a provider of premium material handling, construction and environmental processing
Hy-Brid Lifts, a provder of aerial lift equipment, announces John Davis as director of sales covering the south-central United States.
As the second half of 2023 begins, LiuGong continues to build upon its status as one of the fastest growing
Kalmar Ottawa, a manufacturer of terminal tractors and a trusted name in the industry, has announced its 65th anniversary. For
Continuing to illustrate that no one delivers more, Hyundai Material Handling recently introduced a series of new and innovative products
Christian Harm takes over as Chief Financial Officer (CFO) of KION GROUP AG with immediate effect Marcus Wassenberg leaves the
Effective June 30, 2023, H&E Equipment Services Inc. (H&E) announces the opening of its Port Allen branch, its eighth rental
Sponsorship celebrates the importance of local park and recreation spaces and the professionals who support these spaces across the nation
Effective June 26, 2023, H&E Equipment Services Inc. (H&E) announces the opening of its Statesville branch, its eighth rental location
AmeraMex International, Inc., a provider of heavy equipment for logistics companies, infrastructure construction and forestry conservation, announced that it has completed the final shipment of
Mitsubishi Logisnext Americas Group, the exclusive manufacturer and provider of UniCarriers Forklifts across North, Central and South America, has introduced the
Combination of Rocla and Jungheinrich® automated guided vehicle (AGV) portfolios in the North American market within existing AGV joint venture Rocrich
Effective June 15, 2023, H&E Equipment Services Inc. (H&E) has announced the opening of its Mobile branch, its fifth rental