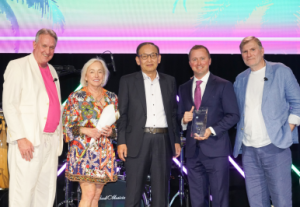
Shoppa’s Material Handling earns 20th Toyota President’s Award
Leading dealership recognized for excellence in customer satisfaction, sales, and operations Shoppa’s Material Handling has received the prestigious Toyota Material
Leading dealership recognized for excellence in customer satisfaction, sales, and operations Shoppa’s Material Handling has received the prestigious Toyota Material
Yale Lift Truck Technologies announces the winners of the 2024 Dealer of Excellence award, the company’s top honor for members
Camera system detects pedestrians near the lift truck in both indoor and outdoor environments, triggers alerts for operator awareness Hyster
Senate Judiciary Chairman Chuck Grassley and Rep. David Joyce introduced the Combating Organized Retail Crime Act (CORCA) to create a
CLARK Material Handling Company has announced the expansion of TRI LIFT Industry’s territory to include Charleston, South Carolina. TRI LIFT,
CLARK Material Handling announced the grand opening of its Global Headquarters in the Dallas-Fort Worth Metroplex. This milestone marks the
For the 34th consecutive year, Carolina Handling has been named a Dealer of Distinction (DOD) by The Raymond Corporation, a
With the integration of Toyota Material Handling and The Raymond Corporation now complete, Toyota Material Handling North America introduces a
Forklifts Group has announced it will expand its business operations to the West Coast with seven dealership locations. This will enable
Combilift, the global leader in innovative material handling, unveiled its pioneering Self-Propelled Inloader ‘COMBi-SPI’ at Bauma 2025. This highly anticipated launch marks a
JCB, headquartered in the UK, is set to double the size of a new factory currently under construction in Texas.
Carolina Handling has partnered with Kinexon, a global provider of real-time tracking and automated operations, to offer its customers AGV
MT120 Delivers Increased Operating Capacity, Best-In-Class Lift Height, Low Cost of Ownership Bobcat Company introduces the MT120, its most powerful
Yale Lift Truck Technologies announces a new pedestrian awareness camera solution, the latest addition to the Yale Reliant™ portfolio of active
Hyster announces the recipients of its 2024 Dealer of Distinction award, which recognizes individual dealer performance and their commitment to
The Program Recognizes the Company’s Highest Performing Dealers Across the U.S. and Canada Bobcat Company has announced its 2025 Dealer Leadership Groups.
Toyota Material Handling has announced the 15 recipients of its annual President’s Award. Presented at Toyota’s annual dealer meeting in
Bobcat Company showcased two new forklifts at ProMat 2025. The DV160S-9 and D45S-9 were introduced along with several other cutting-edge Bobcat products. The Bobcat booth featured
LiuGong North America has added Discount Forklift to its expanding dealer network, marking a significant milestone for both companies. With
Today, Mitsubishi Logisnext Americas, one of the world’s leading manufacturers and providers of material handling, automation, and fleet solutions, announced Berry