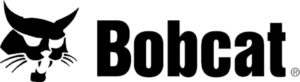
Bobcat Company expands lineup with heavy construction equipment
Four new large wheel loaders and two new large excavators join the Bobcat lineup Bobcat Company, an equipment, innovation and
Four new large wheel loaders and two new large excavators join the Bobcat lineup Bobcat Company, an equipment, innovation and
Material handling industry veteran with 26 years of experience named Leader in Excellence by Supply & Demand Chain Executive Hyster-Yale
H&E Rentals (H&E) announced the opening of its Lowell branch, the company’s fourth new location this year and its fourth facility in
Carolina Handling has named Brian St. John its Director of National Accounts. St. John joined Carolina Handling in 2014 as
Riekes Equipment doubled the size of its Sioux City, IA, facilities to support its growing operations. “We are very excited
Fairchild Equipment has announced its 40th anniversary this year, marking four decades of leadership and innovation in material handling solutions
Bobcat Company recognized Forklifts Group (Ohio) as one of its 2025 Dealer Leadership Groups, highlighting the company as one of Bobcat’s highest-performing
Big Joe Forklifts has announced four new products and its new corporate theme – Powering Progress™ reflects the new and
Yale Lift Truck Technologies has announced Yale Relay™, an overarching platform encompassing all automated lift trucks the company releases going forward and an
New, high-capacity diesel pneumatic Tire forklifts Bobcat Company, a global equipment, innovation and worksite solutions brand, has expanded its North
Celebrate four decades of collaboration in Canada Since the 1980s, Arrow Speed Controls and Mitsubishi Electric Automation have delivered automation solutions
Bobcat booth to highlight new forklifts, expanding the long tradition of delivering powerful performance and increased productivity Bobcat Company is
As part of Engineers Week, Combilift opened its doors to local schools in an initiative to promote STEM education and
Yale Representative recognized for hard work and vision as part of major accounts team Yale Lift Truck Technologies announced that
Equipment Fleet and Working Capital Management Generate Strong Fourth Quarter Cash Flows as Pressured Volumes and Gross Margins on Equipment
Bobcat Company has announced its 2025 Dealer Leadership Groups. The 55 Bobcat dealerships honored this year are the company’s highest-performing dealers across respective
Hyster has announced an expanded lineup of high-capacity electric forklifts that offer the configurability to match a range of heavy-duty
Cromer Material Handling and Doosan Material Handling Solutions of Southern California have officially transitioned to Forklifts Group, a provider of material
Hyster-Yale Materials Handling, Inc., and Yale Lift Truck Technologies announced MH Equipment® has been appointed the authorized Yale® dealer for portions
Experience interactive demonstrations and next-generation technology transforming logistics and warehousing Mitsubishi Logisnext Americas Inc. (“Logisnext”), a manufacturer and provider of