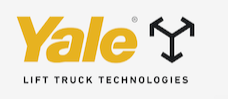
Yale Advanced Dynamic Stability takes top honors in product of the year competition
Readers of material handling publications vote the standalone operator assist technology the top automated data capture product of 2024 Yale
Readers of material handling publications vote the standalone operator assist technology the top automated data capture product of 2024 Yale
The KION Group finished the financial year 2024 with consistent operating performance and strong financial results: With slightly improved revenue
Mitsubishi Logisnext Americas Inc. has announced its participation in ProMat 2025. As an exclusive partner of Jungheinrich® lift trucks, narrow-aisle and
Yale Lift Truck Technologies has announced recognition by Food Logistics and Supply & Demand Chain Executive as a 2024 Top
Yale Lift Truck Technologies will bring an interactive booth experience featuring the latest advances in technology in and around the
Mitsubishi Logisnext Americas, the exclusive manufacturer and provider of UniCarriers® Forklifts across North, Central and South America, proudly announces the winners of its Premier Club Awards for 2024. This
Mitsubishi Logisnext Americas, one of the world’s leading manufacturers and providers of material handling, automation and fleet solutions, has announced
CLARK Material Handling Company has announced the winners of the 2024 Dealer of The Year, New Dealer of the Year,
As a Susan G. Komen® Pink Tie Guy Ambassador, Shoppa’s is Raising Vital Funds to Support Research, Advocacy, Patient Care,
Fairchild Equipment, a recognized leader in the material handling industry, has been awarded the prestigious MVP (Most Valuable Partner) Award
Effective February 10, 2025, H&E Rentals announced the relocation of its Bakersfield branch. The facility is now located at 34967
Attendees of The ARA Show 2025 had a lot on their hands. Before the tradeshow opening, talks on what the Future
Carolina Handling has been awarded the prestigious MVP (Most Valuable Partner) Award for its outstanding achievements in 2024 by industry
In the Asia Pacific Region Yale Lift Truck Technologies has launched the Yale® ERP2.0-3.5MXLG electric counterbalance forklift, powered by lithium-ion
Indoor and outdoor operations in the Asia Pacific Market Hyster has launched its new integrated lithium-ion battery-powered forklifts in the Asia
The Raymond Corporation has selected a new research proposal from Purdue University to receive funding through its University Research Program. After reviewing innovative
Toyota Material Handling MidSouth showcased its dedication to fostering the next generation of industry professionals by donating a 5,000-pound-capacity Toyota Core IC
Cyngn Inc. has announced that it will be deploying its DriveMod Tugger at a major Consumer Packaged Goods (CPG) distribution company.
The latest addition to JLG’s North American electric construction product lineup JLG Industries, Inc., has announced its 60-ft EC600AJ boom
Cyngn Inc. has announced that it has continued making notable inroads in the automotive manufacturing sector. To date, the company