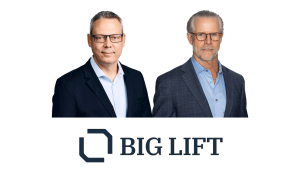
Big Lift adds CMO and VP of Sales to its management team
Today, Big Lift, LLC announced the appointment of Martin Boyd as Chief Marketing Officer and Jason Dunigan as Vice President
Today, Big Lift, LLC announced the appointment of Martin Boyd as Chief Marketing Officer and Jason Dunigan as Vice President
NOBLELIFT Opens New Facility in Korea and has a Grand Opening Ceremony. On September 25th, NOBLELIFT celebrated the official opening
Cyngn announced the expansion of its dealer network to include Raymond West. A leading distributor and integrator of intralogistics solutions,
Forklift-International.com, the online marketplace for material handling equipment, has announced a major milestone for its U.S. operations. The platform currently
Yale Lift Truck Technologies announces that the ERC050-060VGL series of lithium-ion-powered lift trucks has received a 2024 Green GOOD DESIGN® award. The line
Bobcat Company has been selected as a Red Dot Award: Design Concept winner for RogueX2, an all-electric, fully autonomous concept
KION Group has signed a cooperation agreement with a manufacturer of pallet shuttle systems, Eurofork, in Frankfurt am Main, Germany
Hyster Company announces its selection as a 2024 Green Supply Chain Partner by Inbound Logistics magazine. The award honors Hyster for innovating clean power
Bobcat Company, a global brand of compact equipment, innovation, and worksite solutions, introduces its all-new TL623 telehandler. This telescopic tool carrier is loaded with premium performance
Hy-Brid Lifts announced that Charlie Haskin will be the director of sales covering the western United States. Haskin’s responsibilities include
Combilift, the Irish manufacturing giant, celebrated a landmark achievement at the prestigious Irish Exporter of the Year Awards 2024, becoming
The Raymond Corporation hosts students for onsite tours and demonstrations on National Manufacturing Day, highlighting the importance of skills development
Intella Parts Company declared a winner in its contest to find the oldest operating Toyota forklift. Alexander Toolsie from Burlington,
Wolter Inc. just announced significant developments in our national growth strategy, including creating a new region and appointing key executive
Now under one roof: Automated trucks and software development, customer solutions development, project realization, and production The new facility improves efficiency
H&E Rentals has announced the opening of its Dallas South branch, the company’s 33rd location in the Lone Star State.
For the 12th consecutive time in the awards’ 16-year history, Combilift has been recognized as a Best-Managed Company, requalifying as
Lorri Lewis was named a trailblazer, Jennifer Timblin was honored as a rising star Hyster Company announces Director of Global Dealer
Cyngn announced the first build of the next-generation 12,000 lb DriveMod Tugger has been completed at the facility of its
For the 12th consecutive time in the awards’ 16-year history, Combilift has been recognized as a Best-Managed Company, requalifying as