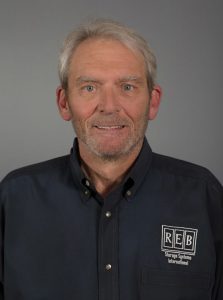
Industry leader Mike Baily remembered
Mike Baily, an Industry Specialist at REB, has passed away. A tribute was published on LinkedIn, expressing heartfelt messages about
Mike Baily, an Industry Specialist at REB, has passed away. A tribute was published on LinkedIn, expressing heartfelt messages about
Bradford Systems has announced a strategic partnership with Rainbow Dynamics. This collaboration aims to revolutionize storage and retrieval systems across
Visit booth #S1956 to see how versatile VRCs improve efficiency and worker safety PFlow Industries will showcase its vertical material
Mallard Manufacturing, a leader in gravity flow racking systems and solutions, will exhibit at PROMAT 2025 in Chicago, IL, from
New framing solution provides versatility, cost savings, and seamless integration with Steele Solutions’ platform systems. Steele Solutions Inc., a manufacturer
This growth will further Wize Solutions’ plans for the Phoenix Metro Area Wize Solutions has announced that it has acquired
Fourth quarter and full year 2024 diluted EPS of $1.22 and $8.46, respectively. Fourth quarter and full year 2024 net
Versatile portable racks provide a wide range of flexible storage solutions for warehouse professionals Selective pallet racking is a versatile,
KPI Solutions (KPI), a supply chain consulting, software, systems integration, and automation supplier, announced that Gartner has recognized the company
stow announced the successful completion of the largest mobile racking installation in Northern Europe, at Frigoscandia’s state-of-the-art logistics facility in
Consolidated net earnings attributable to Nucor stockholders of $249.9 million, or $1.05 per diluted share Adjusted net earnings attributable to
For businesses seeking optimal warehouse logistics management, Steel King Industries, an OEM with extensive expertise in designing and manufacturing high-quality
MAHLE Aftermarket turned to Kardex for an automated storage and retrieval solution following a shift in orders from large pallets
Nucor Corporation announced consolidated net earnings attributable to Nucor stockholders of $645.2 million, or $2.68 per diluted share, for the
Fairchild Systems, a division of Fairchild Equipment, has been named one of the top 8 dealers, receiving the prestigious 2023
Vertical reciprocating conveyors (VRCs) act as the pivotal link between two major trends in warehouse operations that are dramatically increasing
Net earnings attributable to Nucor stockholders of $844.8 million, or $3.46 per diluted share Net sales of $8.14 billion Net
Nucor Corporation just announced that it has acquired Southwest Data Products, Inc. (SWDP), a manufacturer and installer of data center
Google LLC, Microsoft Corporation, and Nucor Corporation have announced they will work together across the electricity ecosystem to develop new
Nucor Warehouse Systems has been selected to provide a structural rack for a hundred-foot-tall, rack-supported building using an advanced AS/RS