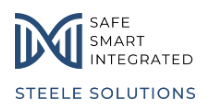
Steele Solutions showcasing advanced structural steel platforms and material handling chutes at MODEX 2024
Booth highlights will include exclusive demonstrations of the future of elevated structural platforms and SST™ material handling chutes, with individual