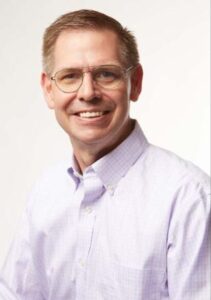
Nucor announces the addition of Nicholas C. Gangestad to the Nucor Board of Directors
Nucor Corporation announced its Board of Directors elected Nicholas C. Gangestad as a director effective September 1, 2023. Mr. Gangestad,
Nucor Corporation announced its Board of Directors elected Nicholas C. Gangestad as a director effective September 1, 2023. Mr. Gangestad,
WillScot Mobile Mini Holdings Corp. has announced PRORACK, a proprietary space management solution aimed at delivering unparalleled organization, productivity, and
Recognition honors leading suppliers in service, quality and continuous improvement ORBIS® Corporation, an international provider in reusable packaging, has earned
Event raised $330,000 to support practitioners and patients in the Pediatric Simulation and Resuscitation Program ORBIS® Corporation has hosted its
AttaBox® Enclosures, the provider of polycarbonate enclosure solutions, announces that its AttaBox Weight Distribution Shelf and Side Panel have received
Nucor Corporation today announced guidance for its second quarter ending July 1, 2023. Nucor expects second quarter earnings to be
Wildeck now offers its popular mezzanines in stainless steel. Stainless steel mezzanine platforms are designed to provide superior durability in
Welcome to the New Warehouse podcast. In this episode recorded at ProMat 2023, Kevin hosts Daniel Aguirre, Sales Manager at
Company expanding Headquarters to allow for growth, retain top talent, and be an employer of choice delivering quality material handling
Haver & Boecker Niagara offers Make and Hold and Stocking Agreement programs for screen media and wear parts. The programs
As per a recent market analysis by Future Market Insights (FMI), the global warehouse racking market is expected to capture
Net earnings attributable to Nucor stockholders of $1.14 billion, or $4.45 per diluted share Net sales of $8.71 billion Net earnings before noncontrolling interests of $1.23 billion;
RM2 has announced that Wayne Cochran has joined the company as Chief Operating Officer. Wayne brings with him a wealth
Effective April 1, 2023, Nichole Wheeler has been named Vice President and Chief Financial Officer of Cisco-Eagle according to president
MHS Lift, Inc. has been honored as a 2022 Great 8 Award winner by Wholesale Pallet Rack Products (WPRP), a wholesale distributor
Mezzanine Safeti-Gates, Inc., an innovator in the design and manufacturing of pallet drop safety gates that provide fall protection in
Barcoding, Inc., the provider of efficiency, accuracy, and connectivity, announces today the hiring of Michael Tassinari as the firm’s new Chief
Murata Machinery USA, Inc. ( Muratec), a logistics & clean room automation forerunner and a world-class leader in machine tool
UNEX Manufacturing, Inc. will be showcasing its dynamic solutions for manufacturing, fulfillment, retail, and logistics in Booth #S3527 at ProMat,
New pallet repair facility marks 37 locations nationwide Millwood, Inc. added a second New Jersey-based pallet repair location in Barrington,