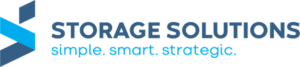
Jungheinrich AG to acquire Storage Solutions group
Strengthens Jungheinrich’s intralogistics business with a complementary regional footprint Adds strong growth platform for warehouse automation solutions in the U.S.
Strengthens Jungheinrich’s intralogistics business with a complementary regional footprint Adds strong growth platform for warehouse automation solutions in the U.S.
ORBIS® Corporation, an international provider in reusable packaging, has added the new 40×48 Odyssey® Low Profile (LP) pallet to its
Steel King Industries, a manufacturer of storage rack and material handling products has announced that Rona Rossier-Abel has been named
Millwood, Inc. acquired its second Texas and 36th location nationwide. Millwood Co-owners and Partners Chip Trebilcock and Steve Miller finalized
QUIET Platforms install PALLITE™ PIX™ storage solutions across their warehousing facilities PALLITE™, the award-winning international designer and manufacturer of high-density
The acquisition is Millwood’s second Waverly, OH location Millwood, Inc. acquired its second location in Southern Ohio and 35th location
Live from MODEX 2022, Joe Rooney, Executive Vice President at Baker Industrial Supply & Anchor Manufacturing, joins The New Warehouse
In a letter to clients, DAK Solutions Dave Kenealy shared acquisition news, “I am pleased to share that RMH Systems
Tubelite Inc.‘s Steve Green will retire as Vice President of Sales in March 2023 at the end of the company’s
On this week’s episode of The New Warehouse, Eric Andres of Hannibal Industries (Nucor Warehouse Systems) joins Kevin to discuss
SupplyOne’s Packaging Management Program provides a roadmap to enhanced efficiency, sustainability, and cash flow SupplyOne, Inc., an independent supplier of
The new location further expands PLA’s nationwide pallet, logistics, and supply chain services capabilities PLA, a portfolio company of Silver
Apex Companies, headquartered in Oak Brook, IL, has announced that Engineered Handling, Inc, a storage and warehouse equipment supplier based
The new ProGenic® GMA+ is NSF approved/Certified, FDA compliant, and offers non-halogen FM approval Polymer Solutions International (PSI®), a global
Nucor Warehouse Systems combines the legacy and expertise of Hannibal and Elite Storage Solutions material handling companies with the breadth
Live from MODEX 2022, I sit down with John Clark from Steel King Industries for this week’s episode of The
VP of Supply Chain Brian Pfannes to lead the Company beginning January 2023 Steel King Industries, a manufacturer of storage
Pallet Logistics of America (“PLA” or the “Company”), a portfolio company of Silver Oak Services Partners, LLC (“Silver Oak”) and
When it comes to warehouse safety, training is a key piece in building the foundation. That line of thinking was
CCPC is the 10th Ohio and 32nd Overall Millwood location Millwood, Inc. acquired its 10th Ohio and 32nd location nationwide.