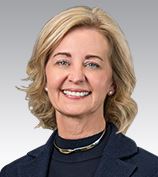
Nucor announces Executive Vice President MaryEmily Slate to retire, John Hollatz to be promoted
Nucor Corporation announced that MaryEmily Slate, Executive Vice President of Commercial, plans to retire due to health issues on June
Nucor Corporation announced that MaryEmily Slate, Executive Vice President of Commercial, plans to retire due to health issues on June
As many businesses across the country struggle to deal with rising labor and materials costs, the logistics industry is one
Wildeck, Inc, the largest U.S. manufacturer of industrial steel work platforms, material lifts, access solutions, and safety guarding products, has
Wildeck, Inc, one of the largest U.S. manufacturers of industrial steel work platforms and safety guarding products, has been continually
Nucor Corporation today announced consolidated net earnings of $2.10 billion, or $7.67 per diluted share, for the first quarter of
Nucor Corporation has announced that it has acquired steel racking manufacturer Elite Storage Solutions for $75 million. This acquisition expands
In this episode, I was joined by VP of Sales and Marketing at SpaceGuard Products Ray Niemeyer. SpaceGuard provides protective
S.A.F.E. Structure Designs has announced the delivery of custom fall protection maintenance platforms to the Army in Ft Hood, Texas.
S.A.F.E. Structure Designs has announced the delivery of custom fall protection maintenance platforms to the Army National Guard in Springfield
Storage Solutions Inc. announces forming a partnership with Daifuku North America in which Storage Solutions has become an official integrator
Creform Corporation, a manufacturer of unique products for material handling structures has designed and produced a mobile heavy-duty flow rack
Due to the demand for increased automation in material handling, distribution, and manufacturing facilities, Mezzanine Safeti-Gates, Inc. has extended options
Creform Corporation, a manufacturer of unique products for material handling and commercial structures has designed, built, and fully assembled a
Steel King Industries®, a manufacturer of storage rack and material handling products, has earned the prestigious MVS (Most Valuable Supplier)
National Rack Repair, Inc—an Indiana-based integrator of industrial storage and safety products, is now the North American home of the
With more than $1 billion in completed turnkey projects, Hannibal is the end-to-end material handling solutions provider for today Hannibal,
The acquisition adds expertise in warehouse automation and material handling Pantero has announced the acquisition of Ampro Material Handling, a Detroit-area racking
Steel King Industries, a manufacturer of storage rack and material handling products, is proud to announce Arlin Keck P.E., Steel
Combining rigid-frame engineering with the proven benefits of tension fabric membranes, Legacy Building Solutions offers superior quality fabric structures that
Acquisition incorporates new capabilities and an expanded team for TFS Racking & Automation Division TFS, an OnPoint Group Company, and provider