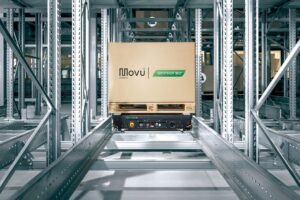
The Movu atlas pallet shuttle offers Westhof BIO automated high performance in deep-freeze storage
German Organic vegetable freezing company Westhof BIO has selected easily accessible, plug-and-play automation in the form of a stow Racking silo
German Organic vegetable freezing company Westhof BIO has selected easily accessible, plug-and-play automation in the form of a stow Racking silo
Nucor Warehouse Systems (NWS) has opened its doors to its Texas location at its Houston open house on Friday, April
Cabka, a provider of reusable transport packaging made from recycled plastic, has announced its participation in the upcoming Pack Expo
Bruce Krarup to assume role, responsibilities Millwood, Inc. has filled the position of Chief Financial Officer (CFO) effective February 27.
SIGI, the parent company of several of the world’s leading manufacturers of ergonomic vertical positioning equipment, has announced the appointment
ABCO Systems has been awarded the prestigious MVP (Most Valuable Partner) Award for its accomplishments in 2022 from the premier
Got-Rack.com just announced that Nelson Cantillo has joined their company to be its new VP of Corporate Strategy and Business
Virginia Tech life-cycle analysis tests plastic pallet’s durability ORBIS® Corporation, an international leader in reusable packaging, validated that its 40×48-inch
When times get hard, living in a small close‐knit community can oftentimes have a huge advantage. In following in their
Purchase means new product brand, additional erosion services Millwood, Inc. finalized the purchase of CORE Erosion Control Services in September.
Steel King Industries, Inc., a manufacturer of material handling products and systems for improving operational efficiency, announces that the I-Beam Cantilever
Hannibal Industries, one of the largest steel pallet rack manufacturers in the U.S., has announced that it has selected Baker
BEUMER Group, an industry provider in the design and manufacture of intralogistics systems, has successfully completed a nine-month modernization project