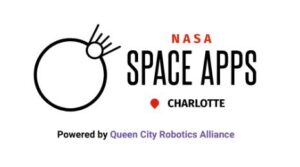
Queen City Robotics Alliance is Charlotte’s official host for the 2024 NASA Space Apps Challenge
This global event happens at The Zone October 5-6 Queen City Robotics Alliance announced that it has been selected as
This global event happens at The Zone October 5-6 Queen City Robotics Alliance announced that it has been selected as
Queen City Robotics Alliance has announced the addition of two new board members – Robert Hillman and Brian Keiger. Robert
AMT has appointed Craig Salvalaggio, previously the Chief Operating Officer (COO), as its new president to lead the company’s growth
Tompkins Solutions, a supply chain consulting and material handling integration firm, announced that Steven Nickel has joined the company as senior
Plus One Robotics, a provider of advanced robot vision perception software and solutions for parcel handling systems performing over one million picks per
Leading AMR Provider Recognized for Material Handling Automation Expertise and Commitment to Improving the Global Supply Chain Seegrid Corporation, the
Tompkins Robotics, a leader in the robotic automation of distribution and fulfillment operations, has partnered with Global Robotics Services (GRS),
STXI Motion, a global motion control and servo solution company, will present a variety of low-voltage mobile motion platform solutions intended for
Caja Robotics, a leader in robotic and flexible goods-to-person solutions for order fulfillment, announces today its partnership with Ranpak, a
On this episode, I was joined by the Director of Sales for BALYO, John Hayes. BALYO is an autonomous mobile
Baur will leverage deep experience to strengthen the company’s European presence Caja Robotics, a provider in flexible robotic goods-to-person solutions
Robo Boston, one of the largest celebrations of robots and robotics of its kind, will take place in the innovative
On this episode, I was joined by A.K. Schultz the Co-Founder and CEO of SVT Robotics. A.K. and I connected
RightHand Robotics introduces Next-Generation RightPick™ 3 Item-handling Robot System at ProMatDX, the company’s newest generation of the award-winning RightPick product
Toyota Material Handling (TMH), North America’s largest full-line material handling and forklift solutions provider, is leveraging trusted automation technology to offer customers a solution
The test center located in Karmøy, Norway, can replicate hot and cold weather conditions as well as simulate earthquakes AutoStore,
AMT and OTTO Motors partner to provide cutting-edge material handling solutions utilizing autonomous mobile robots (AMRs) amid growth in eCommerce
In this episode, I was joined by CEO and Founder of Vecna Robotics, Daniel Theobald, as we reconnected post MODEX
Company’s history shows a culture of innovation and commitment to quality This year marks a major milestone for JLS Automation.
1,000 LocusBots to support 12 DHL sites in North America this year DHL advances the nationwide deployment of Locus’s Industry-Leading