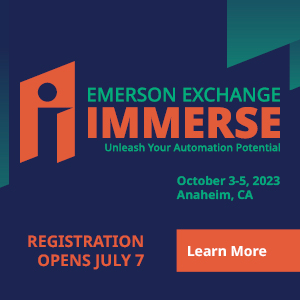
Registration now open for Emerson’s new Software-Focused Automation Conference
Emerson Exchange Immerse offers users an opportunity to share successes, improve skills and knowledge, and work hands-on with new technologies
Emerson Exchange Immerse offers users an opportunity to share successes, improve skills and knowledge, and work hands-on with new technologies
Joe Oliaro, VP of Sales and Chief Real Estate Officer at Wagner Logistics, joins this episode of the New Warehouse
ANT everywhere, a new product extension by the Swiss autonomous navigation leader, enables a new era of AGV & AMR
Plus One Robotics, a provider of AI vision perception software and solutions for robotic parcel handling, has expanded its sales team with two
CoEvolution is rapidly achieving success in the multi-fleet robot orchestration market with the deployment of its market-leading AI-powered solutions. By
Kivnon, a global producer of autonomous mobile robots (AMRs) and automated guided vehicles (AGVs), has announced that TAP, an industrial
MassRobotics, a robotics innovation organization, announced its inaugural Robotics Medal and Rising Star recipients at the IEEE ICRA conference in
Autonomously recognizes, locates and grasps randomly placed objects at a rate of up to 40 pieces per minute (PPM) Reduces
KPI Solutions (KPI), a supply chain consulting, software, systems integration, and automation supplier has announced that Kyle Smith has joined
OTTO Motors, a provider of autonomous mobile robots (AMRs), just announced that its autonomous forklift, OTTO Lifter, has been recognized
Plus One Robotics, a provider of AI vision perception software and solutions for robotic parcel handling, has announced the appointment of Martin
Technology is rapidly reshaping the way business is conducted, particularly for manufacturers. Robotics are poised to transform the entire manufacturing
AutoScheduler.AI, an innovative Warehouse Management System (WMS) accelerator, has been named a 2023 Top Food Chain Technology company by Food Chain Digest,
Senior Project Manager Sean Phillips, P.E. of Hargrove Controls & Automation, an industrial automation system integrator and a subsidiary of
Zion Solutions Group is steering the growth of material handling automation amidst evolving economic conditions. With a proven track record
Distribution center technology provider Lucas Systems announced its rollout of new technologies promising productivity, comfort, and ease of use to
In the latest episode of The New Warehouse podcast, Kevin Lawton sits down with Guy Courtin, the VP of Industry
Plus One Robotics, a provider of advanced AI vision software and solutions for robotic parcel handling, has announced the hiring
Bates will streamline technology onboarding and optimize the customer experience SVT Robotics, a provider of enterprise software for the integration
Industry veteran Chris Barber leads the eastern regional team to provide sales and service that transforms companies’ distribution and fulfillment