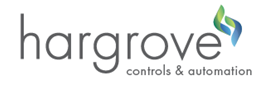
Unlocking the Power of Employee Ownership: Hargrove Controls & Automation’s Karen Griffin shares insights with ESOPs at 2023 CSIA Conference Panel
Vice President of Hargrove Controls & Automation Karen Griffin will be participating in a panel discussion on “Succession Planning to