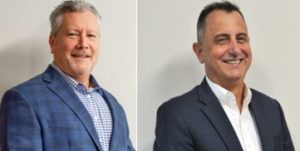
SUN Automation Group announces new leaders over SUN625 product line
SUN Automation Group (SUN), a global leader in providing innovative solutions to the global corrugated industry, has announced two well-deserved
SUN Automation Group (SUN), a global leader in providing innovative solutions to the global corrugated industry, has announced two well-deserved
Dr. Ilan Cohen, the Chairman, and CEO at Caja Robotics, returns to The New Warehouse to discuss robotics solutions for
Universal Robots joins this week’s episode of The New Warehouse podcast to discuss how their robotic solutions improve the world
Live from the booth at MODEX, Berkshire Grey joins this episode of The New Warehouse to discuss some of their
SWIFTI™ CRB 1300 industrial collaborative robot is six times faster and five times more precise than other robots in its
In this bite-size episode of The New Warehouse, Michael Hansen, Co-founder and Managing Director at ROEQ, joins Kevin to discuss
Two years ago, the starting signal was given for the completely new warehouse for DHL Pharma Logistics in Laekebeek (Brussels
KPI Integrated Solutions, a supply chain consulting, software, systems integration, and automation supplier announces the opening of a full-scale demonstration
Locus Robotics, a provider of autonomous mobile robots (AMR) for fulfillment and distribution warehouses, today announced more than $117 million
Kindred, part of Ocado Group, joins The New Warehouse podcast at MODEX 2022 to share how their robotics solutions improve
Perhaps you know Boston Dynamics from their viral videos of dancing robot dogs or their humanoid robot that moves with
AutoStore Holdings Ltd. (AutoStore) has announced the appointment of current Chief Revenue Officer Mats Hovland Vikse as CEO, effective January
On this week’s episode of The New Warehouse Podcast, we welcome Amir Bousani, Co-Founder and CEO of RGo Robotics. RGo
Numina Group, an independent systems integrator providing warehouse automation and order fulfillment solutions, has announced the addition of Cody Upp
Welcome to today’s episode of The New Warehouse, where we welcome Josh Cloer, Director of Sales at Mujin Corp. Mujin
Welcome to The New Warehouse Podcast. In this episode, our guest is Michael Myers, Director of Product Solutions from Third
Hy-Tek Material Handling debuts a new look as Hy-Tek Intralogistics- reflecting the company’s growth and new brand promise Hy-Tek Material
Fort Robotics joins The New Warehouse podcast live from MODEX 2022. David Sullivan, Principal Product Manager, and Mike Zipperer, Product Development
Motion Industries, Inc., a distributor of maintenance, repair, and operation replacement parts, and a premier provider of industrial technology solutions
The new venture focused on end-user goals will be led by Nick Malewicki Today Big Joe Forklifts announced the creation