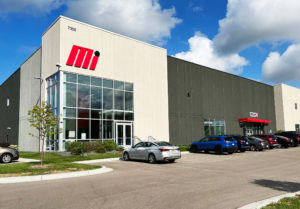
Motion AI opens new facility in Minnesota
Motion Industries, Inc., a distributor of maintenance, repair, and operation replacement parts, and a premier provider of industrial technology solutions
Motion Industries, Inc., a distributor of maintenance, repair, and operation replacement parts, and a premier provider of industrial technology solutions
The new venture focused on end-user goals will be led by Nick Malewicki Today Big Joe Forklifts announced the creation
Pandemic conditions have improved, but the new era of labor shortages and increased demand continues for warehouses. In this environment, some
Plus One Robotics, the fastest and most reliable parcel-handling robotics platform, performing over one million parcel picks each day in
MassRobotics, an innovation hub and startup cluster focused on the needs of the robotics community, today announced it is collaborating
Emerson to supply control systems, software, and engineering services Specialty chemicals company LANXESS has selected Emerson, a global software and
The acquisition will accelerate the automation growth Strategy with new complementary capabilities, expanded scale and international reach Lincoln Electric Holdings,
Israel-based smart inspection planning company c has announced that its CAD2SCAN software has received the VISION Award for best innovation in the machine vision
If you love talking warehouses and robotics, this episode is for you. Erik Nieves, founder of Plus One Robotics and
Tompkins Robotics, a global provider focused on the robotic automation of distribution and fulfillment operations, has announced two new leaders
Seegrid Corporation, a provider of autonomous mobile robots (AMRs) for material handling, has announced that Joe Pajer has joined the
Creating heterogeneous fleets of mobile robots by integrating products from different vendors is the next step in warehouse automation. CoEvolution
Applied Manufacturing Technologies COO Craig Salvalaggio will present “The Important Role of System Integrators in Robot Safety” at the International
Matthews Automation Solutions, a provider of innovative material handling systems and software, and proven process optimization expertise, has announced that
Zion Solutions Group, a supply chain integrator, has announced, Controller, Kathy Frank as a recipient of the 2022 Women in
Ziccardi and Moore’s combined efforts have helped retailers and 3PLs of all sizes leverage inVia’s AI-powered Automation System to meet
In his new role, the former Solutions Architect will lead internal business process development, and data quality management, and oversee
As an apparel manufacturer and distributor, Cutter & Buck is known for high-quality clothing crafted for active lifestyles and engineered
RoboBoston, one of the largest celebrations of robots and robotics of its kind, takes place in the innovative Boston Seaport
AGILOX, the provider of Autonomous Mobile Robot forklift solutions, is growing at a rapid pace. In order to keep up