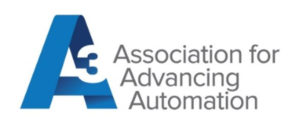
Robot sales hit record high in North America for third-straight quarter
Association for Advancing Automation latest stats shows the most robots sold in any quarter; the automotive industry returns to historic
Association for Advancing Automation latest stats shows the most robots sold in any quarter; the automotive industry returns to historic
GEODIS, a global transport and logistics provider, and Locus Robotics, a provider of autonomous mobile robots (AMRs) for fulfillment warehouses,
The New West Coast office enhances the company’s national presence for warehouse optimization and automation services MHS Lift, Inc., a
Welcome to the New Warehouse Podcast! In this episode, Kevin is live from MODEX 2022. Craig Henry, U.S. Industry Manager
Joining Kevin from the booth at MODEX 2022 is Vince Martinelli, Head of Product and Marketing at RightHand Robotics. Unlike
RightHand Robotics, a provider of data-driven, autonomous robotic picking solutions for order fulfillment, announced today that Gartner, the global research
Applied Manufacturing Technologies brings Scott Kilpatrick on as vice president of sales in a strategic hire to support an increase
AutoScheduler.AI, an innovative Warehouse Management System (WMS) accelerator, names Keith Moore as CEO with Tom Moore, Founder, moving to the Board of
Geek+, the global provider of autonomous mobile robot (AMR) technology has entered into a strategic partnership with Systemex Automation, a
Kassow Robots, a developer of 7-axis cobots for machine tending, material handling, and related applications, has partnered with Industrial Control
How fitting to have three guests join me for what is officially the 300th episode of The New Warehouse Podcast.
I’m excited to welcome back Seth Weisberg to the New Warehouse Podcast. Seth is the CEO of ABCO Systems which
According to a report by Oxford Economics, faster adoption of automation could equate to an extra $4.9 trillion per year
Joining me this week from the booth at MODEX 2022 is Jake Heldenberg from Vanderlande. Jake is the senior manager
The Northeast US premier material handling company marks a major business milestone, building on one hundred years of dedication, professionalism,
End-to-End Packaging Solutions for mitigating labor, efficiency, and waste-reduction challenges SupplyOne, Inc., the largest independent supplier of custom corrugated and
BMG announces the Mantis Robotic Trim Press Handler from NAS Nalle Automation Systems, the industry’s first robotic automated system that
In this week’s episode of The New Warehouse, I sit down with Sanjay Chopra, co-founder and CEO of Cognistx. Cognistx
Applied Manufacturing Technologies promotes Engineering Manager Arthur J. Kahler to Director – Controls Engineering, citing his contributions and hands-on leadership
This week’s podcast is another interesting discussion from MODEX 2022, where I sat down with Daniel Theobald of Vecna Robotics.