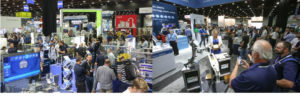
Automate 2022 exceeds expectations with largest attendance and exhibitor count ever
Association for Advancing Automation expands floor space for Automate 2023 after this year’s show ends with 24,000 registrants, 600 exhibitors,
Association for Advancing Automation expands floor space for Automate 2023 after this year’s show ends with 24,000 registrants, 600 exhibitors,
Caja Robotics, a provider of robotic and flexible goods-to-person solutions in fulfillment, engages in close cooperation with Fives, one of
RightHand Robotics, a provider of data-driven, autonomous robotic picking solutions for order fulfillment, announces the deployment and installation of RightPick™
Boston-based robotics and STEM nonprofit receive three years of funding from the Cummings Foundation MassRobotics is one of 140 Massachusetts
Autonomous mobile robot provider is recognized for solutions that address supply chain pressures, labor challenges, and rising costs Seegrid Corporation,
Partnership expands use of robotic piece-picking for order fulfillment centers in the APAC region RightHand Robotics, a provider of data-driven,
Applied Manufacturing Technologies COO Craig Salvalaggio and Controls Manager Terry Meister will share technical expertise on autonomous mobile robots and
Kassow Robots, a developer of 7-axis cobot solutions for machine tending, material handling, and related applications, exhibits at Automate for the
DESTACO has announced that it will be exhibiting in Booth No. 3013 at the upcoming Automate Tradeshow 2022, which will
Unpredictable markets, an unstable procurement chain, and impatient customers are just a few challenges your supply chain deals with. Balancing
FANUC America, a global provider in CNCs, robotics, and ROBOMACHINEs, will introduce the new DR-3iB/6 STAINLESS delta robot for primary
Seegrid Corporation, the manufacturer of autonomous mobile robots (AMRs) for material handling, has announced the launch of a new customer
RightHand Robotics, a provider of data-driven, autonomous robotic picking solutions for order fulfillment, announces its debut at LogiMAT 2022, the
Kassow Robots, a developer of 7-axis cobots for machine tending, material handling, and related applications, has partnered with BlueBay Automation
BeBop Sensors, Inc., the world provider of smart fabric sensor technologies, has announced the BeBop Sensors RoboSkin line of skin-like coverings
Mobile Industrial Robots (MiR) has announced that Mark Joppru has joined the autonomous mobile robot (AMR) first mover and global
In this episode, I was joined by the father-daughter duo of Dave and Maddie Haley. They are both in the
The Amazon Industrial Innovation Fund invests in BionicHIVE to address a key challenge in the fast-growing supply chain emerging technology
In this episode, I was joined by Ed Kennedy of Procensis at MODEX 2022. Procensis is focused on turning your
While 80% of employed U.S. adults consider an employer’s professional development and training offerings an important consideration when accepting a