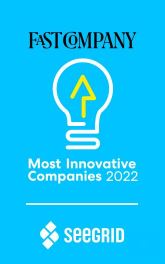
Autonomous Mobile Robot provider recognized for transforming the global supply chain with Intelligent Automation Solutions
Seegrid Corporation, the provider in autonomous mobile robots (AMRs) for material handling, has been named to Fast Company’s prestigious list