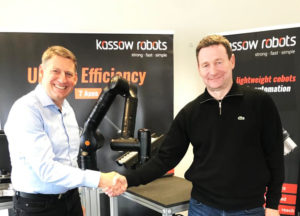
Kassow Robots expands sales team to support partners and expand manufacturer networks
Kassow Robots, a developer of 7-axis cobot solutions for machine tending, material handling, and related applications, is strengthening its sales
Kassow Robots, a developer of 7-axis cobot solutions for machine tending, material handling, and related applications, is strengthening its sales
In this episode, I was joined by Mike Kotzian of Kivnon. Mike is the Managing Director for the USA at
The new hire comes with deep knowledge and enthusiasm for automation across a range of industries including the medical market
AGILOX makes new top management appointments. Helmut Schmid takes over as CEO in January 2022, as successor to the previous
Company to expand its AI-powered growth platform for distributors Proton.ai, the leading AI-powered growth platform for wholesale distributors, announced today
The new robot, built based on the proven technology of the R5 model, can handle bins up to 425mm Warehouse
With 20 years of combined experience in the material handling industry, new hires Adam Gurga and Collin Russell will grow
Autonomous Mobile Robot provider to leverage Best-in-Class Simulation tools to accelerate delivery of Next Generation Material Handling Automation Solutions Seegrid
Automation key for ensuring presents are produced on time With Christmas around the corner, it is time to focus on
In this episode, I was joined by Jim Lawton of Zebra Technologies. Jim is the Vice President and General Manager
In this episode, I was joined by Brandon Coats of Mujin. Brandon is the Director of System Integration at Mujin
In this episode, I was joined by Matt Cherewka of Vecna Robotics. Matt is the Director of Business Development and
STXI Motion, a global motion control, and servo solution company, presents a range of low-voltage, mobile motion solutions, and cabinet-free
Swisslog, a provider of best-in-class warehouse automation and software, is providing a boost to delivery efficiency and click and collect
When the coronavirus pandemic hit in early 2020, the e-commerce fulfillment landscape underwent a massive shift in response to spikes
Mesa Air Group, Inc., has signed an agreement with aerospace technology company Flirtey to order four delivery drones, with an
In a market with reported labor shortages and shifts in supply chain conditions, material handling companies have a series of
Efficiency is key in all warehouses, but especially in the food and beverage industry. If operations don’t run smoothly, products
Coined by Gartner to describe one of the biggest automation trends of 2020, the concept of hyperautomation has rapidly spread
The latest addition to the popular Lachenmeier Stretch Hood Technology Line features a smaller footprint, minimized maintenance Signode, a global