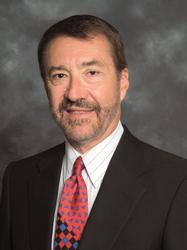
AI and Robots are aiming for dealers. Are you prepared?
Last month, we covered performance gaps and how to avoid them because if you cannot prevent them, there is a
Last month, we covered performance gaps and how to avoid them because if you cannot prevent them, there is a
Honkanen brings a nearly 25 years of automation expertise, a passion for simplifying complexity, and a customer-centric approach to his
As part of Engineers Week, Combilift opened its doors to local schools in an initiative to promote STEM education and
Backed by Toyota Ventures, IL Ventures, Elements VC, Payton Planar, and Doral Energy, CaPow scales production and R&D to meet growing
Mitsubishi Electric has launched its MELFA RH-10CRH and RH-20CRH SCARA robots, providing manufacturers with greater flexibility in adopting digital manufacturing
OSARO’s researchers have developed an innovative AI-powered technique that enables robots to accurately determine graspable object positions through physical interaction,
igus® has introduced the DR1000 four-axis delta robot that combines high speed and precision for demanding industrial applications. The DR1000,
Mezzanine Safeti-Gates extends safety gate line beyond people and products Mezzanine Safeti-Gates, Inc., has announced that it now offers RobotGate™,
Since its first commercial robot sale in 1975, Cimcorp has become a global leader in logistics automation with an open-minded
Matthews International has announced a global commercial partnership between its Automation Solutions business segment and Mobile Industrial Robots (MiR), a
On this episode of The New Warehouse Podcast, Kevin is on-site at Zebra Technologies’ robotics demo center in San Jose,
Walden Catalyst Ventures and NGP Capital Lead Investment to fuel Ati Motors Global Expansion across North America and APAC. Ati
This episode of The New Warehouse Podcast features Anthony Jules, Co-Founder and CEO of Robust AI. Anthony shares insights into
Partnership to drive adoption of next-generation high-speed, high-density storage and retrieval solutions for warehouse and last-mile operations Freespace Robotics has
RealMan Robotics is set to unveil its groundbreaking innovations at CES 2025, reaffirming its commitment to transforming industries and advancing
Welcome to another exciting episode of The New Warehouse Podcast! Today’s guest is Al Dekin, Chief Revenue Officer and Co-Founder
Addressing labor challenges and enhancing operational efficiency are crucial priorities in manufacturing, warehousing, and logistics. Automating the palletized material workflow
AMR Innovator Excited to Contribute to Industry Advancement Initiatives Seegrid Corporation has announced its membership in the Open Source Robotics
In this episode of The New Warehouse Podcast, Kevin speaks with Pramod Ghadge, Co-Founder and CEO of Unbox Robotics. The
Seegrid AMRs are enhancing efficiency, safety, and productivity in industrial facilities Seegrid highlights its innovative Tow Tractor S7 AMR. This dependable