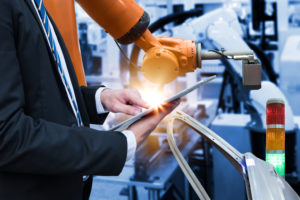
What’s the hype in hyperautomation?
Coined by Gartner to describe one of the biggest automation trends of 2020, the concept of hyperautomation has rapidly spread
Coined by Gartner to describe one of the biggest automation trends of 2020, the concept of hyperautomation has rapidly spread
The latest addition to the popular Lachenmeier Stretch Hood Technology Line features a smaller footprint, minimized maintenance Signode, a global
On this episode, I was joined by Tony Hollis of Saddle Creek Logistics. Tony is the Director of Technology &
PSA, the world’s largest consortium of professional systems integrators, just announced the addition of viisights to its approved technology partners.
Locus Robotics, the provider of autonomous mobile robots (AMR) for fulfillment warehouses and distribution centers, has announced the opening of
As part of MHI view’s ongoing video program, this MHI view episode focuses on: Making robots accessible to warehouse employees
Bringing deep and broad experience in complete turn-key processing solutions BMG (Brown Machine Group) has announced the appointment of Brian
In this episode, I was joined by Suman Kharbanda of FedEx. Suman is the Director of Advanced Technology and Innovation
Hyster Company continues its leadership in robotics, has announced its membership in the Association for Advancing Automation (A3). Formerly the
On this episode, I was joined by the CEO of Kindred.ai, Marin Tchakarov. Kindred.ai is bringing together advanced robotics and
Oshkosh Corporation, an innovator of mission-critical vehicles and essential equipment, and Carnegie Foundry, a robotics and artificial intelligence (AI) venture
Berkshire Grey, Inc., the provider of AI-enabled robotic solutions that automate supply chain processes, is partnering with Advanced Handling Systems
On this episode, I was joined by the VP of Digital Strategy at Blue Horseshoe, Steve Shebuski. Blue Horseshoe is
Robo Boston, one of the largest celebrations of robots and robotics of its kind, will take place in the innovative
Showcases Innovative, Impactful, and Intriguing new businesses AutoScheduler.AI, an innovative Warehouse Management System (WMS) accelerator, announces mention in Gartner® “Cool
GEODIS, a global transport and logistics provider, and Advanced Handling Systems (AHS, LLC), a full-service provider of integrated fulfillment and
BMG (Brown Machine Group) will be showcasing robotic automation technology from NAS Nalle Automation Systems at PACK EXPO Las Vegas,
Darr Equipment Co., one of the largest Caterpillar forklift dealerships in the country, announced the launch of 54 Intralogistics. The
With two decades of engineering, project management, and automation experience, David Campbell joins Burns & McDonnell to lead design and
Automation has become an irreversible trend, especially as the pandemic has affected industries around the world. This trend presents companies