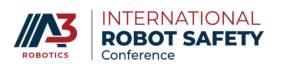
International Robot Safety Conference agenda features top industry experts on the latest Safety Standards, Techniques, and Technologies
Virtual Conference runs Sept. 20-22, offers an in-depth overview of robot safety Top industry experts from FedEx, Universal Robots, Fetch