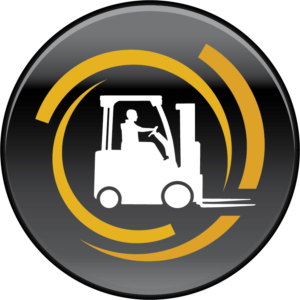
Yale breaks new ground for warehouses with Operator Assist Lift Truck Technology
Yale Reliant solution helps reinforce lift truck operating best practices by controlling performance based on real-time information and site-specific rules
Yale Reliant solution helps reinforce lift truck operating best practices by controlling performance based on real-time information and site-specific rules
Kaman Distribution Group (“KDG”), a value-added distributor of bearings, power transmission, automation, and fluid power products, has announced the appointment
STXI Motion, a global motion control, and servo solutions company, introduces the servSD ready-to-connect low-voltage servo drive, aimed at applications
On this episode, I was joined by the Co-Founder and CEO at SIERA.AI, Saurav Agarwal. I was very excited for
DSV, the Danish transport and logistics company, is expanding its position in the 3PL market through the use of AutoStore
On this episode, I was joined by the Director of Strategy at ProMatDX, Matt Cherewka. We have had Vecna on
Leading Autonomous Mobile Robotics provider launches In-House Innovation Acceleration Team to rapidly deliver the future of material handling automation Seegrid
The company continues expanding its global presence with a center for collaboration and business development based in Nürnberg, Germany RightHand
The Willich office will provide customer support and increase the intralogistics automation company’s presence in continental Europe Cimcorp, a manufacturer
Repetitive and non-value-adding tasks are driving turnover rates in warehouses. As employers search for solutions to this problem, automation is
In order to meet the increasing demands of its customers, Toyota Industries Corporation (TICO) will bundle its software development in
Advanced Handling Systems (AHS, LLC) has announced that they will be partnering with Caja Robotics to optimize a Midwest distribution
Signode, a global manufacturer of a broad spectrum of end of line packaging equipment, tools, and consumables, will showcase its
In this episode, I was joined by the CEO of Locus Robotics, Rick Faulk. Recently Locus Robotics was valued at
In the future, VARTA will not only be a battery supplier for Pepper – the world’s first social humanoid robot
Motion Industries, Inc., a distributor of maintenance, repair, and operation replacement parts, and a premier provider of industrial technology solutions,
In this episode, I was joined by two guests, Dr. Ilan Cohen and Hannah Yanovsky of Caja Robotics. Ilan
In the Clayton, Indiana facility, Cimcorp’s Layer Pick system increases throughput and ensures order accuracy Cimcorp, a manufacturer and integrator
On this episode, I was joined by the Senior Vice President of Sales at Vecna Robotics, Jeff Huerta. Vecna has
In this episode, I was joined by the Warehouse Robotics Practice Leader at Bricz, Parth Pethani. Bricz is a global