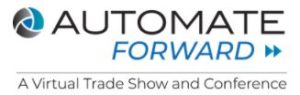
Automate Forward Keynote Speakers, Full agenda announced
Virtual Trade Show and Conference to feature more than 80 speakers, 250+ exhibitors More than 80 global experts will speak
Virtual Trade Show and Conference to feature more than 80 speakers, 250+ exhibitors More than 80 global experts will speak
In this episode, I was joined by a friend of the show Karen Leavitt who is the Chief Marketing Officer
In this episode, I was joined by Kraig Foreman who is the DHL President, eCommerce, DHL Supply Chain, North America.,
Innovative case-handling robots address the demand for warehouse automation, complete with local support from MHS MHS, a single-source provider of
New cloud-based addition, Fleet Geek, optimizes autonomous mobile robot performance, drives continuous improvement, and demonstrates impact of automation across the
Virtual reality is becoming a valuable teaching tool in training new supply chain employees. With the ability to simulate a
Attendees will have the opportunity to view on-demand demos of Cimcorp’s automated systems and chat live with a company expert
Recent months, and the last holiday season, in particular, brought an e-commerce boom like no other. As the pandemic accelerated
In this episode, I was joined by the CEO and Founder of inVia Robotics, Lior Elazary. You may remember Lior
The new distribution center in Kansas City planned to support the significant growth of Urban Outfitters, Inc. The key automation
New Robot Product Line Self-Charges and Autonomously Stages Pallet Lanes for Uninterrupted Flow of Goods Seegrid Corporation, the provider in
Cost-effective, lightweight plug & play combination consisting of gearbox, encoder, controller, force control system, and motor for service robotics The
Rapidly Growing Autonomous Mobile Robot Provider Increases Strength and Depth of Leadership to Meet Growing Demand for Industrial Automation Seegrid
The announcement comes on the heels of acquisition for growing e-commerce supplier MHS Holdings, Inc. (“MHS” or the “Company”), a
Kivnon expands its mobile robot portfolio with a new range of Automated Forklifts and a new rotational lifting platform AGV/AMR
The acquisition expands MHS’s capabilities to serve the fast-growing e-commerce industry MHS Holdings, Inc. (“MHS” or the “Company”), a global
In this episode, I spoke with Jon Schechter who is a Business Development Manager at AutoStore. We just recently spoke
Supply chain solutions are more critical to business success than ever before. How do you keep up with increasing customer
Autonomous mobile robot provider announces a 100% increase in revenue for 2020 Seegrid Corporation, a provider in autonomous mobile robots
In this episode, I was joined by Andrew Benzinger who is a Business Development Manager at AutoStore. Andrew and I