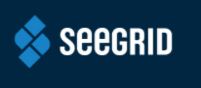
Seegrid doubles revenues, sees record adoption of Material Handling Automation Solutions
Autonomous mobile robot provider announces a 100% increase in revenue for 2020 Seegrid Corporation, a provider in autonomous mobile robots
Autonomous mobile robot provider announces a 100% increase in revenue for 2020 Seegrid Corporation, a provider in autonomous mobile robots
In this episode, I was joined by Andrew Benzinger who is a Business Development Manager at AutoStore. Andrew and I
In this episode, I was joined by the CEO of AutoGuide, Rob Sullivan. Rob was previously on the show on
In this episode, I was joined by Vince Martinelli of RightHand Robotics. Vince is the Head of Product & Marketing
Vanderlande has installed its advanced AIRTRAX Pocket for de Bijenkorf at its Tilburg warehouse, the first large-scale system of its
In this episode, I got a chance to speak with Tracy Hansen of ProGlove. Tracy is the president, North America
In this episode, I was joined by former guest Mark Wheeler of Zebra Technologies. Mark is the Director of Supply
Seegrid Has Added 100 Employees in 2020 As It Continues to Grow Its Autonomous Industrial Mobile Robots Business Seegrid Corporation,
AMT hires George Toldy, Jr., MBA and Stephen D. McLaren to support an increase in demand for the company’s engineering
In this episode, I was joined by the CEO of Wyebot, Roger Sands. Wyebot is the leader in AI-driven WiFi
In a virtual panel hosted by the Association for Advancing Automation (A3), robotics thought leaders gather on November 19 to
Ocado Group plc (“Ocado”), the leading online grocery platform and solutions provider, today announces the proposed acquisition of: · Kindred Systems
Kindred announced a partnership agreement with VARGO® to incorporate its artificial intelligence (AI) pick and place robotic solutions with VARGO®’s
In this episode, I was joined by Dr. Sankalp Arora of Gather AI who is their Chief Robotics Engineer. Gather
The acquisition will accelerate the development of human-like awareness for more consistent and productive self-driving industrial vehicles Seegrid Corporation, a provider
In this episode, I speak with Josh Cloer who is a Sales Director at Mobile Industrial Robot. This episode was
In this episode, I was joined by two guests for the November 2020 cover story of Material Handling Wholesaler. I
Automation in the warehouse setting has been increasing in recent decades, as companies look to boost efficiency and safety. Toss
Softeon, a global supply chain software provider with the industry’s best record of customer success, continues to enhance its powerful
In today’s episode, I was joined by one of my peers, Mike Oitzman who is the founder and publisher of