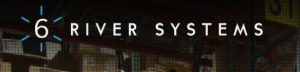
6 River Systems announces next wave of enhancements to its Wall-to-Wall Fulfillment Solution at FLOW 2020
6 River Systems (6RS), part of Shopify Inc., a global commerce company, announced during its second annual user conference, FLOW
6 River Systems (6RS), part of Shopify Inc., a global commerce company, announced during its second annual user conference, FLOW
Providing a perfect platform for heavy and large loads, the self-propelled platform transporter from Hubtex transports machine parts, steel beams,
Artificial intelligence is one of the technologies that is poised to influence the future of the supply chain industry. At it’s
New investment supports high demand for self-driving industrial vehicles as manufacturing and logistics industries continue to embrace automation Seegrid Corporation,
The industry’s top experts and leading companies to participate RIA Robotics Week, the world’s largest virtual robotics show and conference,
In this episode, I was joined by Rob Sullivan at MODEX 2020. Rob is the President and CEO at AutoGuide
Motion Industries, Inc., a distributor of maintenance, repair, and operation replacement parts and a wholly-owned subsidiary of Genuine Parts Company,
In this episode, I was joined by Colman Roche of Swisslog at MODEX 2020. Colman is the VP of E-commerce
Fox Robotics has closed a $9 million Series A led by Menlo Ventures. This brings Fox’s total funding to over
Second expert guide by a leading supplier of rugged mobile computing devices and solutions for logistics, warehousing, and other challenging
The Spanish supermarket chain is investing in logistics automation to ensure picking accuracy, enhanced freshness, and longer shelf life Cimcorp,
In this episode, I was joined by the CEO of Ware, Ian Smith at MODEX 2020. You may remember Ian
On this episode, I had the chance to talk to Joe Campbell of Universal Robots. He is the Senior Manager,
KION Group signs a distribution agreement and a memorandum of understanding on plans for joint development with the Chinese manufacturer,
On this episode, I was joined by Richard Kooistra of Twinlode Automation at MODEX 2020. Richard is the VP of
In this episode, I was joined by CEO and Founder of Vecna Robotics, Daniel Theobald, as we reconnected post MODEX
As part of MHI view’s ongoing video program, this MHI view episode focuses on: Technological innovations are typically pioneered by
In this episode, I was joined by the Founder and CEO of Vecna Robotics, Daniel Theobald at MODEX 2020. I
Located in Alpharetta, Georgia, the office will serve as a center of service excellence for U.S. and Mexican customers with
In this episode, I was joined by Zac Bogart who is the CEO of Productive Robotics. You may remember Productive