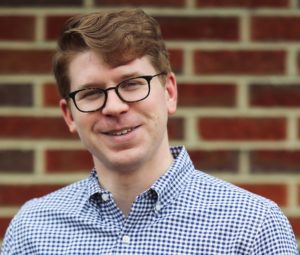
Episode 85 – Lean Ops Solutions at MODEX 2020
In this episode, I was joined by Jason Morin of Lean Ops Solutions at The New Warehouse MODEX booth and
In this episode, I was joined by Jason Morin of Lean Ops Solutions at The New Warehouse MODEX booth and
Houston, Texas Center provides added Automated Guided Vehicle (AGV) Product and Customer Support Mitsubishi Caterpillar Forklift America Inc. (MCFA), the
Swarm Intelligence (SI) and bio-inspired computing have attracted great interest in almost every area of science and engineering, including robotics,
Episode 60 – InVia Robotics at MODEX 2020 In this episode, I am joined by Lior Elazary of InVia Robotics
Episode 70 – Right Hand Robotics at MODEX 2020 In this episode, I was joined by Vince Martinelli who is
FlytBase, Inc. has launched the FlytWare Solution Partner program, designed for win-win partnerships in the supply chain industry, with a
As labor shortages only get worse, moving more products is expanding daily for businesses When it comes to e-commerce, big
The Autonomous Mobile Robot Conference, sponsored by the Association for Advancing Automation (A3), has been rescheduled for Wednesday, Oct. 28, in
Full-Stack platform brings enhanced safety, flexibility, and endpoint security for autonomous and connected machines. Participants at MODEX will get a
Technologies, design and integration expertise combine for a most efficient path to adopt mobile robots MHS a single-source provider of material
Boston Dynamics, a world provider in mobile manipulation robots, and OTTO Motors, a provider in industrial autonomous mobile robots (AMRs),
The free, on-show-floor presentation explains ways to combine traditional material handling automation with collaborative robotic technologies for optimized order fulfillment
Ever wonder what it’s like to drive a security robot? Cobalt Robotics, a manufacturer of intelligent security robots that autonomously
MODEX: POWERED BY POSSIBILITIES THE BEST SUPPLY CHAIN SOLUTIONS THE LATEST EQUIPMENT AND TECHNOLOGY THE SMARTEST THINKING FIND IT ALL
The rise of e-commerce and growing customer expectations has led to more and more logistics companies making residential deliveries. The last
Hytrol will feature the newest additions and enhancements to its products at MODEX 2020 in booth #6605 in March. The
Attendees will learn more about how omnichannel fulfillment gave DSG a competitive edge Bastian Solutions, a Toyota Advanced Logistics company,
The Automatic Guided Vehicle Systems (AGVS) Industry Group of MHI has rebranded as the Mobile Automation Group (MAG). The updated
Tailor-made, efficient and sustainable: Packsize will present its automated solutions for e-commerce at the LogiMAT trade fair in Stuttgart, Germany.
Effective supply chain management can be pivotal for sustained business growth: A Deloitte survey found that “79 percent of organizations