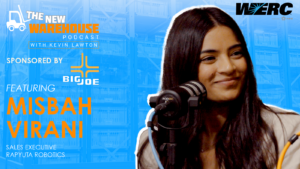
Episode 507: Live from WERC 2024: Rapyuta Robotics
Today, we’re diving into a fascinating discussion from the New Warehouse Podcast, recorded live at the WERC 2024 conference in
Today, we’re diving into a fascinating discussion from the New Warehouse Podcast, recorded live at the WERC 2024 conference in
Partnership with Cycle Labs helps clients elevate testing precision with high-quality, reliable automation NetLogistik, a provider of transformative services for
Dexterity-SC Japan will leverage market-proven AI Technology to address labor shortages and boost efficiency in Japanese warehouse operations with Intelligent
Today’s episode of The New Warehouse Podcast welcomes Cian Denvir, the Director of U.S. Business for Proactive Global. Proactive Global
Unmatched efficacy, convenience, and compliance with food safety regulations Meritech, the provider of automated hygiene technology, highlights its innovative Sole
The Intelligent Logistics Systems Lab will apply new AI- and machine-learning-based methods and technologies to the logistics problems with the
Warehouse software market to grow at a CAGR of 12.7% out to 2030 The standalone warehouse management system (WMS) market
AMT has announced the recent promotions of both Anna Jacobs and Mike Ingles to the roles of Engineering Services Business
In the latest episode of The New Warehouse Podcast, Kevin chats with Erik Nieves, CEO of Plus One Robotics. The
Peak Technologies, a global provider of smart warehouse solutions, has announced its strategic partnership with Robotize, a cutting-edge robotics company
In a groundbreaking move set to enhance and redefine warehouse operations, Zion Solutions Group has announced its strategic partnership with
Supply chain leaders are turning to automation and AI to enhance operational efficiency, reduce costs, and elevate the customer experience Automation
Oren to drive strategic sales efforts for Dematic Americas with two decades of leadership experience Further strengthening America’s leadership team, Dematic
Jungheinrich, RAVAS EUROPE, SAFELOG with Mercedes, SSI Schäfer, and STILL have been announced as winners of the IFOY Award 2024.
In this engaging session from Momentum 2024, I was joined by a panel consisting of Adam Kline and Matt Dermody from
The Robot Roadshow allows attendees eager to learn, experience, or purchase automation to have hands-on interactions with Mitsubishi Electric Automation’s
Cobot Systems has announced that it is now a UR+ Partner with their showcase Laser Welding Cell system. This distinction
Friday, May 31, 5:30-7:30 pm, at The Zone Queen City Robotics Alliance is gearing up for its biggest fundraiser of
Seegrid Corporation has announced Tom Panzarella as Chief Technology Officer (CTO). In this critical leadership role, Panzarella will spearhead Seegrid’s
Comaus S-Family robots are expressly designed for arc welding, e-mobility, food & beverage, and handling applications where accuracy, repeatability, and