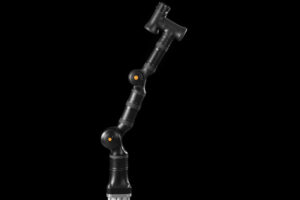
Kassow Robots launches the world’s first 7-axis cobot series with a controller integrated into the base
Greater flexibility for mobile solutions & additional space savings for cramped facilities With its Edge Edition, Kassow Robots has launched the world’s