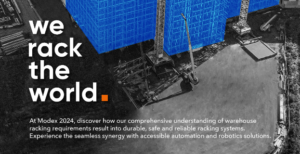
stow Group presents a seamless collaboration of racking and robotics expertise at MODEX 2024
stow Group, a supplier of advanced racking systems and accessible automation and robotics solutions, is presenting its premier brands, stow
stow Group, a supplier of advanced racking systems and accessible automation and robotics solutions, is presenting its premier brands, stow
Tompkins Solutions, a leading supply chain consulting and material handling integration firm, has announced a partnership with Soft Robotics, a
AGILOX North America has announced its participation in the upcoming MODEX 2024 in Atlanta Booth C7492. The company will exhibit
The system enables pre-pack manufacturing testing of battery cells and battery cell performance data storage capabilities McAlister Design & Automation,
Tompkins Solutions, a supply chain consulting and material handling integration firm, has announced that it will be showcasing some of
The next-generation autonomous robotic piece-picking system for warehouse order fulfillment. Building on its industry-leading predecessor, the RightPick 4 system can
Expanding robotic and industrial equipment applications call for small form factor emergency stop switches. IDEC Corporation has expanded its line
Queen City Robotics Alliance (QCRA) recently finished updates and construction of several important projects at The Zone, a 3,000 sq.
Swiss start-up Sevensense, a provider in AI-based navigation, enables the highest levels of speed, accuracy and autonomy of mobile robots,
Piab continues the journey to make our foremost cobot tool family available to all end users. We now offer piCOBOT®
Applied Manufacturing Technologies announces the expansion of its engineering services portfolio to include Ignition by Inductive Automation, a powerful tool
GreyOrange software together with Hai Robotics bots increase throughput, storage density and agility GreyOrange Inc., a global provider in automated
User benefits include seamless network integration, integrated drive safety, versatility, easy installation and commissioning Siemens is extending its drive portfolio
In this episode of The New Warehouse podcast, Kevin welcomes Nilay Parikh, the founder and CEO of Arvist. By leveraging
Following a slowdown in revenues in 2023, the global warehouse automation market will experience some growth in 2024 and return
Motion Industries, Inc., a distributor of maintenance, repair and operation replacement parts, and a premier provider of industrial technology solutions,
In this pre-Thanksgiving episode of The New Warehouse podcast, we welcome Jamie Callihan and Phil Denton from JLC Robotics. Jamie
Movu Robotics, a supplier for designing, developing, and implementing innovative and easier warehouse automation solutions, announces the launch of the innovative Movu eligo
There’s no escaping it—service delivery is a key business driver and not just for Amazon, but across asset-intensive industries where
Movu Robotics, one of the industry warehouse automation and robotics suppliers, proudly announces it was exclusively granted “The Best Use