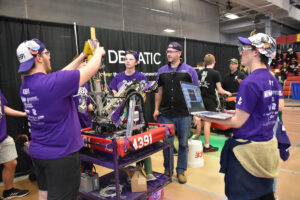
Dematic announces 2023 STEM scholarship winners
Dematic FIRST® Scholarships support students pursuing STEM (science, technology, engineering, and math) educations Dematic announces the 2023 recipients of its Dematic FIRST® Scholarship program,
Dematic FIRST® Scholarships support students pursuing STEM (science, technology, engineering, and math) educations Dematic announces the 2023 recipients of its Dematic FIRST® Scholarship program,
Hamburg-based intralogistics pioneer Jungheinrich is fully taking over Magazino, a Munich-based robotics specialist. In addition to its shareholding, which has
Dual infeed system maximizes robotic movements for heightened throughput; Modular, expandable design brings flexibility and versatility Omega Design Corporation, a
Partnership builds on Seeq advanced analytics innovations and Databricks enterprise AI capabilities to improve data accessibility and enhance machine learning
Lanel Menezes has been named Vice President of Sales for Brenton, a role in which he will be promoting the brand’s
In this exciting episode of The New Warehouse podcast, we sit down with Andrei Danescu, the visionary co-founder and CEO
OTTO Motors, a provider of autonomous mobile robots (AMRs), announced that their autonomous forklift, OTTO Lifter, has been recognized as
Welcome back, avid listeners of The New Warehouse Podcast! In today’s exciting episode, we’re diving into the fascinating world of
In this episode of the New Warehouse podcast, Kevin is joined by Faizan Sheikh, the CEO and Co-founder of Avidbots,
Tompkins Solutions, a supply chain consulting and material handling integration firm, just announced that Dan Bryan has joined the company as
In this exciting episode of the New Warehouse Podcast, Kevin welcomes two guests from Slip Robotics: Chris Smith, the Founder
Sophisticated new machine was concepted, designed and engineered in Norwalt’s dedicated Vision Systems Lab Norwalt, a specialist in custom-built automation
In today’s episode of The New Warehouse Podcast, host Kevin Lawton interviewed Magne Hatteland, the Vice President and Head of Pio.
Chang Industrial and Hai Robotics announced the formation of a strategic partnership targeting North American manufacturers. Chang Industrial has built
Smart Robotics and Labour Power Company announce Strategic Partnership: Providing happy flex workers and the right robotic solutions to optimize
Brenton demonstrates the new XCP Series continuous motion, direct load case packer, and its robotic expertise with an integrated line
We’ve hit the big 400! That’s right, this is the 400th episode of The New Warehouse Podcast, and we couldn’t
The global technology company, AGILOX, was awarded the IFOY award for their latest product innovation the “AGILOX ODM” as the
Emerson Exchange Immerse offers users an opportunity to share successes, improve skills and knowledge, and work hands-on with new technologies
Joe Oliaro, VP of Sales and Chief Real Estate Officer at Wagner Logistics, joins this episode of the New Warehouse