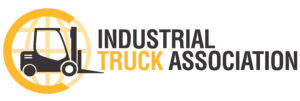
Final Speakers announced National Forklift Safety Day 2025
Tuesday, June 10, 2025 | 9:00 AM – 11:00 AM Live Streamed Event at the National Press Club – Virtual
Tuesday, June 10, 2025 | 9:00 AM – 11:00 AM Live Streamed Event at the National Press Club – Virtual
Toyota Material Handling continues to Drive Industry Awareness Regarding the Importance of Operator Training and Safety Culture with the ‘Every
As the nation observes National Safety Month this June, Riekes Equipment is stepping up with a local initiative that could
Prepare for a groundbreaking showcase of safety innovation as the American Society of Safety Professionals (ASSP) gears up for its Safety
The American Society of Safety Professionals (ASSP) has bestowed its highest honor – the Society’s Fellow distinction – upon five
Two HighwayMAX units acquired last year transform heavy haul The ALL Family of Companies is investing in the future of
J. J. Keller & Associates, Inc. has announced that Adrienne Hartman will become the company’s Executive Vice President of Marketing
AI doesn’t fix safety—that’s the myth. Warehouses that expect real-time insights to magically improve performance are missing the point. AI
Each June, National Forklift Safety Month serves as a valuable reminder of how critical safety is to the material handling
Tackling safety within a warehouse is a multi-layered endeavor. From equipment to building maintenance to the workers themselves, material handling
The American Society of Safety Professionals (ASSP) has named Steven Thygerson its 2025 Safety Professional of the Year. The environmental and
Workplace safety and health professionals have just one week to beat a rate increase for the Safety 2025 Professional Development
Workplace safety and health professionals have just one week to beat a rate increase for the Safety 2025 Professional Development
In high-volume yard operations, safety isn’t just a priority. It’s a critical responsibility. The yard is a dynamic environment where
Launches Safety Ambassador program for companies to promote training achievements Another National Ladder Safety Month has ended with millions reminded,
Visit Booth #139 for cutting-edge products and solutions Pfannenberg, Inc. will present innovative fire alarming solutions tailored specifically for industrial applications
Brass Knuckle® BK-Anti-FOG and BK-Anti-FOG+ get a new brochure Why do the lenses of safety glasses fog? Science! What our
Compact, lightweight, maneuverable, and built for productivity JLG Industries, Inc. has announced its entry into the fast-growing micro-sized scissor lift
FB Chain has been a driving force in transforming lifting equipment worldwide for four decades. From pioneering leaf chain assembly
The values-led shoemaker will not implement tariff-related price increases in 2025 KEEN Inc., the values-led, Consciously Created business, is on