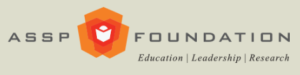
ASSP Foundation receives second grant to advance workplace safety
The American Society of Safety Professionals (ASSP) Foundation has received a second Susan Harwood education and training grant for $159,967
The American Society of Safety Professionals (ASSP) Foundation has received a second Susan Harwood education and training grant for $159,967
From the booth at MODEX 2022, Kevin is joined by Dirk Seis, Director of Marketing at Ideal Warehouse Innovations, Inc.
Acquisition of four generation Maryland-based loading dock specialist supports Miner’s industry expertise and nationwide reach Miner Ltd., the dock and
Responding to disasters is one of the most important activities that employees can be asked to grapple with. From natural
LEDtronics® Inc. has announced its newest series of UL-listed LED Post Top Lamps that put out an impressive amount of
Today’s guest is Aaron Smith, founder of U-Turn Transport and host of the Escape the Odds podcast. Aaron is on
Brass Knuckle® Slingshot™ (BKFLEX-4050AFP) doubles up on vision protection Here’s one Slingshot that’s good for the eyes. New Brass Knuckle® Slingshot™
Cementex, the safety tool specialist, highlights the Cementex Feature Series of Arc Flash Protective Clothing PPE, designed for those seeking
Working at height is inherently hazardous, exposing workers to significant risks that range from falls from roofs, scaffolding, and ladders
The American Staffing Association was promoted to ambassador status in recognition of its longstanding alliance with the Occupational Safety and
Everyone can play a role in minimizing workplace risks that lead to injuries, illnesses, and fatalities. The American Society of
With the release of the Pittsburgh Energy, KEEN Utility incorporates the proven work-hiker performance of the original Pittsburgh for a
Joining me from the booth at MODEX 2022 is Jay Jette, president, and CEO of GMR Safety. With a passion
AttaBox® Enclosures –- the world’s most specified polycarbonate and non-metallic electrical and industrial enclosures — introduces AttaBox SolarShield™ HMI Covers, providing the ultimate HMI
Concentric, LLC, the national provider in DC power management and maintenance for the material handling and critical power industries, announced
The new Independence series from KEEN Utility introduces a work boot built with quality materials, American ingenuity, and get-it-done grit.
Warning, Danger, and Safety Decals Promote a Safe Working Environment Across Verticals Empire Screen Printing, a manufacturer of screen-printed products,
The signature event of the American Society of Safety Professionals (ASSP) returned to Chicago in a big way in June
The new guide builds upon the 2013 Temporary Worker Initiative The American Staffing Association, in partnership with the National Institute
Each segment of the transportation industry carries its own challenges in electrification, and some are easier to overcome than others.