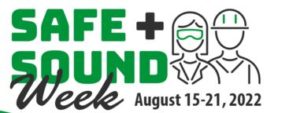
OSHA Safe + Sound Week registration is now open
Safe + Sound Week registration is open! Join thousands of businesses who are recognizing their commitment to workplace safety and
Safe + Sound Week registration is open! Join thousands of businesses who are recognizing their commitment to workplace safety and
The Department of Homeland Security (DHS) Science and Technology Directorate (S&T) announced a Phase 1 Other Transaction award of $161,600 to Kenzen, Inc.,
Mezzanine Safeti-Gates, Inc., an innovator in the design and manufacturing of pallet drop safety gates that provide fall protection in
Brass Knuckle® knee pads for heavy- and light-duty work help protect against injury and extend careers When jobs literally bring workers
APTIM, a global industry provider in program and construction management for critical infrastructure, received 48 safety awards from the National
Brass Knuckle®’s new Spike (BKADJ-5060AFP) eye protection combines a two-pronged strategy for vision protection with a legion of comfort features
New for Summer 2022, KEEN Utility updates the brand’s fan-favorite women’s San Jose work boot, built for the unique fit
The Propane Education & Research Council (PERC) is hosting a new webinar focused on Forklift Safety as part of its Propane Presents Technology Series beginning
Coinciding with National Forklift Safety Day, Yale Materials Handling Corporation just released original training videos as part of the new
Hyster announces completely redesigned training videos for the newly updated Hyster® Operator Training Program, set for release Tuesday, June 14
In this episode, I was joined by Paige Johnson and Dixon Churchill of Toyota Material Handling North America. Paige and
The American Society of Safety Professionals (ASSP) welcomes Doug Parker, assistant secretary of labor for occupational safety and health, to
Toyota Material Handling (TMH) is celebrating National Forklift Safety Day 2022 by reinforcing the importance of creating and maintaining a
Ergodyne announced the launch of an all-new Aerial Bucket Series designed specifically for safer, easier work in bucket trucks and
A scalable virtual reality teaching tool features a wireless HTC VIVE Focus™ 3 headset for a more immersive learning experience
In this episode, I was joined by the Senior Regional Sales Manager at TAWI, Cyrus Choy. TAWI is focused on
With addressing customers’ desire to protect individuals at forklift crossings, Safety Systems & Controls has expanded its Nomad RF transmitter
The American Society of Safety Professionals (ASSP), the world’s oldest professional safety organization, is bestowing the honor of Fellow on
When it comes to warehouse safety, training is a key piece in building the foundation. That line of thinking was
Stahlin® Enclosures, a brand of Robroy Enclosures®, a global manufacturer of fiberglass electrical, instrumentation, and industrial enclosures — announces the availability