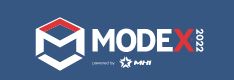
Masks optional at MODEX 2022 in Atlanta
Effective March 1, 2022, the City of Atlanta no longer requires masks indoors. As a result, MODEX 2022 will be
Effective March 1, 2022, the City of Atlanta no longer requires masks indoors. As a result, MODEX 2022 will be
Mark your calendars! Safe + Sound Week will take place from August 15-21, 2022. Safe + Sound Week is a nationwide event held each
Workplace safety and health became national news more than 100 years ago this month when the Triangle Shirtwaist Factory fire in
The American Society of Safety Professionals (ASSP) has opened registration for its signature safety event. The Safety 2022 Professional Development Conference and Exposition will
Saf-T-Gard International, Inc., a full-line, quality-oriented supplier of personal protective equipment for more than eight decades, has stacked its safety
With an easy-on, easy-off laceless design, the new Vista Energy Shift from KEEN Utility builds on the success of its
In this episode, I was joined by the CEO of A-SAFE, Paul Barlow. A-SAFE focuses on protective guarding products made
At first glance, a simple beam of infrared light would seem ineffective protection against fast-moving, dangerous industrial machinery. After all,
With a breathable engineered mesh upper, KEEN Utility’s new Birmingham is a work shoe ready to keep the feet cool
Peggy Arnold, a company driver for Yellow Corporation for nearly 30 years, is one of three finalists for the 2022 Driver of
S.A.F.E. Structure Designs has announced the delivery of custom fall protection maintenance platforms to the Army in Ft Hood, Texas.
S.A.F.E. Structure Designs has announced the delivery of custom fall protection maintenance platforms to the Army National Guard in Springfield
Foul, nasty, or painful debris. Spark. Liquid sprayback. All can slow the most seasoned employee and, worse, bring the threat
Taylor Northeast (TNE), a Pennsylvania-based material handling equipment supplier, just announced that it is now the factory-authorized distributor of EPIQ
Gorbel®, an industry provider in overhead material handling, ergonomic lifting, and industrial fall protection, announces it has been named one
US EPA Administrator Michael Regan recently announced plans to bolster environmental enforcement efforts in communities that have been historically and
Best Mobile App Awards has awarded Kenzen’s mobile app, which alerts workers when their bodies are under stress in hot conditions,
The new Sparta 2 is a fresh update on KEEN Utility’s core athletic work sneaker, designed for light industrial tasks,
Chaotic work environments, distracted workers, and equipment zooming through facilities such as distribution centers, manufacturing facilities, construction sites, or ports
Hikvision, a manufacturer and supplier of security products and solutions, continues to build on its popular line of AcuSense surveillance