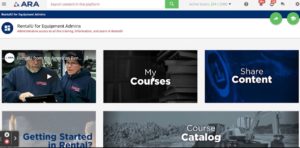
Prioritize safety with ARA’s new video series
The American Rental Association (ARA) just announced the launch of the Prioritize Safety monthly video series focused on essential safety
The American Rental Association (ARA) just announced the launch of the Prioritize Safety monthly video series focused on essential safety
The Women In Trucking Association (WIT) has published a new whitepaper, “Same-Gender Training Policy: Recruiting and Protecting Female Drivers.” Same-gender
Brass Knuckle’s proprietary coatings create a new world standard for anti-fog lenses Lenses can fog in almost every application. Going
Pfannenberg, a global manufacturer of thermal management and signaling technologies, highlights the durable PA 1 PATROL Series Sounder, ideal for
The new FR2 WerkPants offer the same comfort and performance features from Truewerk, but with a flame-resistant treatment. With two-way
Due to the demand for increased automation in material handling, distribution, and manufacturing facilities, Mezzanine Safeti-Gates, Inc. has extended options
In addition to being a resource for occupational safety and health conferences, industry standards, education courses, and networking opportunities, the
It is a common misconception that once machine safeguarding equipment has been installed onto industrial machinery, no further work is
Concentric, LLC, a national provider in DC power management and on-site maintenance for the material handling and critical power industries,
Global supply chain issues are here to stay. Even though these issues and workforce shortages have started getting better, it
viisights real-time video understanding technology further optimizes Cognyte’s situational command and control offerings viisights, the developer of advanced AI-powered behavior recognition
Invixium Integrates Touchless Face Recognition and Multi-Factor Biometric Solutions with AEOS Access Control Invixium, a manufacturer of innovative touchless biometrics,
KEEN Utility’s Juneau offers pull-on convenience with work-focused, tech-forward features. This waterproof medium-duty boot offers the performance, and comfort features
Vestil Manufacturing Corporation is an industry provider in the production and distribution of material handling equipment featuring over 1,000 different
UPDATE: On November 6, the 5th U.S. Circuit Court of Appeals temporarily halted OSHA’s Interim Final Rule on coronavirus vaccination and
Assembled in KEEN’s Portland, Oregon manufacturing facility using responsibly sourced materials from around the world, KEEN Utility’s Dearborn is a
As a global provider in the development of workplace safety and health standards, the American Society of Safety Professionals (ASSP)
Chaotic work environments, distracted workers, and equipment zooming through facilities such as distribution centers, manufacturing facilities, construction sites, or ports
Delivering precise broad area surveillance for demanding environments Hikvision, a global provider in delivering high-performance professional security solutions with tremendous
Invixium Develops New Mobile Platform with Sub-Apps for Remote Face Enrollment, Mobile Credentials, Digital Attestation Questionnaire, and Vital Signs Screening