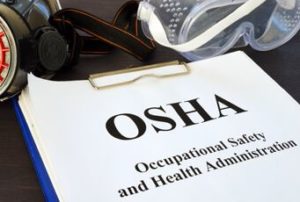
Top 10 OSHA violations of 2021
OSHA unveiled its preliminary list of the top 10 most-cited workplace safety violations for the fiscal year 2021 last week.
OSHA unveiled its preliminary list of the top 10 most-cited workplace safety violations for the fiscal year 2021 last week.
Available in several blade designs and lengths from 10 – 40 inches Metal construction and precision cut rubber for durability
Amanda Birkhead, formerly of Honeywell, joins the Industrial Scientific leadership team Industrial Scientific, a global provider in gas detection and
In this episode, I discuss warehouse standards and their importance. This has been one of the most important things to
Integrates Unique Behavioral Analytics for Public Safety Atos has announced its new partnership to integrate viisights software into its Atos
Toyota Material Handling (TMH) has been recognized with the 2021 Indiana Governor’s Award for Environmental Excellence in the ‘Five Year Continuous Improvement’ category
The new American Built women’s Dover work boot: protection, durability, and a comfortable fit built for a woman. Assembled in
Pronitha Shankarananda, formerly of Fluke, joins the Industrial Scientific leadership team Industrial Scientific, a global provider in gas detection and
The COVID-19 pandemic changed the way many Americans worked last year. So many businesses suffered as a result of the
Major trailer manufacturers are taking initiatives to increase safety for passenger vehicles by reinforcing their rear impact guard (RIG) bars
A radar-based system makes roads safer for pedestrians and cyclists. The system warns drivers with visual and audible alerts. Can
New KeyWatcher Gen3 CPU increases performance, operation, and sync speeds Morse Watchmans, the industry leader in key control and asset
Hikvision, a global provider in delivering high-performance professional security solutions with tremendous value, is introducing a highly versatile standalone mobile
Safety Leaders Exemplify Best Practices in Keeping Workers Safe J. J. Keller & Associates, Inc. just announced the winners of
Despite the growing trend towards electrification, propane continues to keep pace in the material handling space thanks to its reliable
According to the White House website, President Biden has ordered the Department of Labor’s Occupational Safety and Health Administration (OSHA)
Lean, green comfort machine offers eye protection in two ways From its stylish green color, you can tell Brass Knuckle®
New Exit Signs rated for hazardous industrial locations Building on its leadership in providing advanced hazardous location electrical equipment, Emerson
Here’s what to expect at the only show this year to reunite the packaging and processing community Industry excitement remains
Wildeck, Inc. is pleased to announce and welcome Angela Wurtz as its new Director of People Operations. Angela will be