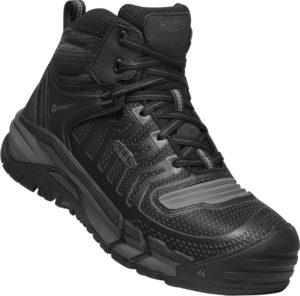
KEEN Utility pushes boundaries with work sneaker
The new Kansas City from KEEN Utility is a standout introduction for Fall ‘21, pushing the boundaries of what a
The new Kansas City from KEEN Utility is a standout introduction for Fall ‘21, pushing the boundaries of what a
Two coats of NBR for extra protection from the world’s worst jobs Why the double dip? Usually, because you want
Provides A Single Platform to Remotely Manage Physical Security Operations Hikvision’s HikCentral Professional platform provides a centralized software solution to remotely
Panasonic i-PRO Sensing Solutions Corporation of America, a subsidiary of Panasonic i-PRO Sensing Solutions Co., Ltd. and a global leader
The new study underscores the need to transition to clean energy sources, like propane, as soon as possible The Propane
Custom Industrial Products, the Pioneer of Modular VRC Material Lifts, expands its business with the launch of new Modular Mezzanines
Brass Knuckle® Crusher safety goggles with contoured channels route moisture away from eyes Whether working in the elements or working
Cleaner look-and-feel as well as new metrics and reports for easier deployment, more actionable insights, and streamlined data interpretation KINETIC,
Safe + Sound Week is a nationwide event held each August that recognizes the successes of workplace health and safety programs
On this episode, I was joined by Peter Schnorbach of Manhattan Associates. Peter is the Senior Director of Product Management
Fit and feel of latex, better durability than vinyl, right-priced The quest for a “just right” disposable glove is seemingly
The 4-Way Fork Box Pallet Dispenser offers a new line of pallet dispensers to improve safety while reclaiming space and
Philly-based startup Juno Jones secures the U.S. Trademark on its iconic “J” logo. Juno Jones recently launched a line of
TVH in the Americas (TVH), a global provider of quality replacement parts and accessories for the material handling and industrial
Impact resistance, ANSI A5 cut protection, ANSI/ISEA 107-2010 high visibility—all without sacrificing comfort Some jobs need a glove that covers
On this episode, I was joined by Sarah Swan of The FPI Consortium. Sarah is a Senior Code Specialist at
Designed for small/medium trucks, ag, construction, and material handling Ideal for use on articulated equipment Specialized camera for forklift applications
On this episode, I was joined by the Co-Founder and CEO at SIERA.AI, Saurav Agarwal. I was very excited for
Newest American Built Boot integrates KEEN.BELLOWS FLEX Technology with premiere safety features This summer, KEEN Utility brings innovation and American
President and CEO Michael Field serves as chair, reinforces training with connected technologies June 8 marks the 8th annual National