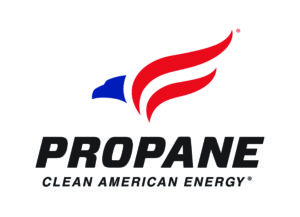
Propane Council announces Mission Zero Pledge, shares free resources for Forklift Safety Day
Take pride in workplace safety and sign PERC’s Mission Zero Pledge In honor of Forklift Safety Day, celebrated June 8,
Take pride in workplace safety and sign PERC’s Mission Zero Pledge In honor of Forklift Safety Day, celebrated June 8,
National Monitoring Center, a third-party monitoring center, proudly announces the 20th anniversary of the company’s founding. In those years, NMC
In this episode, I was joined by Jake Jakobson of Custom Industrial Products for the latest in our partnership with
TVH in the Americas (TVH), a leading provider of quality replacement parts and accessories for the material handling and industrial
To help prevent accidents at aisle ends and other high-risk intersections, Rite-Hite has introduced the Safe-T-Vu™ Warning System, a rack-mounted
Innovative load binders for safer and more efficient load securement The Crosby Group, a global provider in lifting, rigging, and
Brush up on important safety reminders this Forklift Safety Day Forklifts are key to workplace productivity but introduce a variety
No matter the size or type of material handling organization, safety is frequently a top consideration. How to keep employees
The new Vista Energy series from KEEN Utility is a standout introduction for Spring ’21, built for the rigorous indoor
The National Forklift Safety Day (NFSD) sponsored by the Industrial Truck Association will again be virtual on Tuesday, June 8th.
Brass Knuckle® splash goggle/face shield-in-one is the force to be reckoned with When it comes to protective equipment inspiring compliance, only
The new lightweight two-gas monitor offers more accurate alarms and minimizes maintenance with a two-year runtime Industrial Scientific, a global
The eighth annual event takes place the week of May 3-7, 2021 JLG Industries, Inc., an Oshkosh Corporation company and
Not all employers are bound by the recordkeeping and reporting requirements established by the Occupational Safety and Health Administration (OSHA). Generally,
Heavy equipment theft of everything from forklifts, skid steers, and trucks to bulldozers, backhoes, excavators, and wheel loaders can be
The Celebration of Safety is an annual event hosted by the National Safety Council – Nebraska Chapter to recognize companies
The company also expands popular online seminar program to a monthly schedule in response to growing demand Rockford Systems, LLC.
The Upender is an ergonomic “lifting aid” that helps prevent worker injuries, lowering the cost of claims and downtime. Ergonomic
WIKA Mobile Control (WMC), a manufacturer of operator aids and sensors for lifting equipment, names Crane Warning Systems as their
The Occupational Safety and Health Administration (OSHA) has announced the date for Safe + Sound Week. This year it will