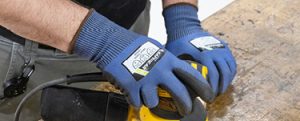
Over 100k hand injuries occur at U.S. workplaces each year
J. J. Keller responds with expanded work glove selection & free informational resource for employers Hand injuries are among the
J. J. Keller responds with expanded work glove selection & free informational resource for employers Hand injuries are among the
As fleets seek sustainable energy solutions, propane delivers 99% reduction in NOx alongside increased reliability This Earth Day, the Propane
The American Society of Safety Professionals (ASSP) encourages safety professionals and employers to raise awareness and participate in the 12th
In-Person and Hybrid Event June 10, 2025 | 9:00 AM – 11:00 AM Industrial Truck Association’s twelfth annual National Forklift Safety
Camera system detects pedestrians near the lift truck in both indoor and outdoor environments, triggers alerts for operator awareness Hyster
The American Society of Safety Professionals (ASSP) will present three keynote sessions that attendees won’t want to miss this summer
The American Society of Safety Professionals (ASSP) has planned another installment of its standards education series called “Stand Up for
Intella Parts Company has published a new blog post analyzing forklift-related fatalities reported by OSHA between 2017 and 2024. The
The American Society of Safety Professionals (ASSP), the world’s oldest professional safety organization, has announced its new volunteer leaders based
The American Society of Safety Professionals (ASSP), is deeply concerned by reports that the National Institute for Occupational Safety and Health
Yale Lift Truck Technologies announces a new pedestrian awareness camera solution, the latest addition to the Yale Reliant™ portfolio of active
As the Global Workforce Ages, MAI Delivers an Ergonomic, Future-Ready Solution to Keep Skilled Workers Productive and Safe ProGlove has
The American Society of Safety Professionals (ASSP) just made the following statement regarding the confirmation of Secretary of Labor Lori
Dawn and Pink Grasshopper eye protection are packed with features, don’t sacrifice style Women in Construction Week will be held March
The American Society of Safety Professionals (ASSP) is helping to lead an occupational safety and health coalition committed to safeguarding
In this episode of The New Warehouse Podcast, Kevin welcomes Pascal Jetté, VP of Business Development at GMR Safety. They
New for Spring ‘25, the men’s Gibson offers a low profile that fits as well on the job site as
Mezzanine Safeti-Gates extends safety gate line beyond people and products Mezzanine Safeti-Gates, Inc., has announced that it now offers RobotGate™,
67% of managers surveyed would consider using virtual reality training J. J. Keller & Associates, Inc. has announced the release
Audible and visual alarms at IIAR Natural Refrigeration Conference & Heavy Equipment Expo 2025. Visit Booth 451 to learn how