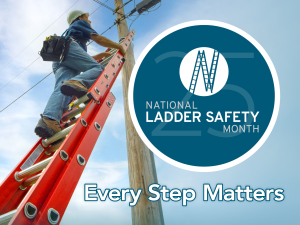
Every step matters: National Ladder Safety Month coming in March
Resources and training from American Ladder Institute help keep workers safe The months leading up to March and National Ladder
Resources and training from American Ladder Institute help keep workers safe The months leading up to March and National Ladder
Smart trial program offers free units to showcase exceptional value and performance Hikvision is redefining the perception of thermal IP
Proprietary BK-Anti-FOG+ is 40 times stronger than the strictest standard One of the simplest, most effective weapons used by early
Learn how to create a safe, productive workplace JLG Industries, Inc., an Oshkosh Corporation business and a manufacturer of mobile
New for Fall ‘24, KEEN Utility introduces the new San Jose 90°. Featuring a 90° heel on the fan-favorite San
Forklifts are essential to the efficiency of warehouse operations, often moving heavy loads and navigating through narrow aisles. However, operating
The American Society of Safety Professionals (ASSP) has updated a key national voluntary consensus standard for construction and demolition sites,
Vestil Manufacturing, a manufacturer of industrial and safety products market, just announced a major expansion project. The development will include
The American Society of Safety Professionals (ASSP) has revised a national voluntary consensus standard that defines core elements of a
As Tropical Storm/Hurricane Helene approaches landfall on the Florida Gulf Coast, ALAN is busy preparing, and we are encouraging all
Today, the NRF Foundation launched a new Customer Conflict De-escalation training program for front-line retail employees. The latest offering is part
Occupational safety and health professionals can now find even more value in being a member of the American Society of
Ladder Safety Month: American Ladder Institute offers sponsorships for 2025 campaign This past March, the message of National Ladder Safety Month reached
The signature event of the American Society of Safety Professionals (ASSP) attracted 6,758 workplace safety and health professionals this month
The American Society of Safety Professionals (ASSP) is seeking a diverse group of occupational safety and health professionals to present
New for Fall ‘24, KEEN Utility’s Overton is a modern work sneaker built with a wide toe and snug heel
J. J. Keller & Associates, Inc. has partnered strategically with Juno Jones Safety Boots, the National Safety Council Award-winning safety
As Hurricane Debby makes landfall in Florida, the American Logistics Aid Network (ALAN) is urging residents of the Southeast to
The American Society of Safety Professionals (ASSP) will welcome Doug Parker, assistant secretary of labor for occupational safety and health,
Knee pads and back support reduce injury risk, minimize joint fatigue According to the Bureau of Labor Statistics, musculoskeletal disorders