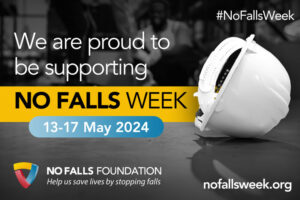
LOBO Systems supports No Falls Week 2024
Safety in working at height environments LOBO Systems has announced its commitment to the No Falls Week Foundation’s upcoming event, No Falls
Safety in working at height environments LOBO Systems has announced its commitment to the No Falls Week Foundation’s upcoming event, No Falls
The National Retail Federation today issued the following statement from Executive Vice President of Government Relations David French after members
NORD’s new gear motor QR codes link to convenient digital services for unit documentation, service and sales contact requests, and
The American Society of Safety Professionals (ASSP) has bestowed the honor of Fellow on Daniel G. Hopwood, who has made
New for Spring ‘24, the Evanston from KEEN Utility offers the burly protection of a work boot with the athletic
Welcome to another fiery episode of The New Warehouse Podcast! Today, we’re joined by Ralph Bless, Executive Vice President at
Carolina Handling has received the 2023 Health & Safety Award for Excellence from Kautex, A Textron Company, a Tier One
The American Society of Safety Professionals (ASSP) encourages safety professionals and employers to raise awareness and participate in the 11th
Matrix Design Group, LLC hosted a groundbreaking ceremony for its new headquarters in Newburgh, Indiana on April 18. It was attended
The American Society of Safety Professionals (ASSP) has named Matthew F. Herron its 2024 Safety Professional of the Year. The safety
The American Society of Safety Professionals (ASSP) has named Thomas G. Bobick the recipient of the 2024 Thomas F. Bresnahan Standards
The American Society of Safety Professionals (ASSP), has announced its new leaders based on the 2024 Society elections. All terms
Ehab Tayel, TÜV (Rheinland), FSE, CFSE, brings nearly two decades of process safety experience and a passion for the safety
Leslie Rex Stockel, a widely respected educator in the occupational safety and health field and member of the American Society
Barcodes are often underrated and underappreciated, but they play a pivotal role in product safety, efficiency, and movement within the
DuraLabel has announced the immediate availability of its new Kodiak Max, industrial sign and label print systems. Kodiak Max allows
Affordable protection that fits and feels great When eyewear fits right, feels good, and looks great, the protection stays on.
Forklift operators who are insufficiently aware of the load they are lifting and the risks that come with exceeding the
Workplace safety and health became national news 113 years ago next week when the Triangle Shirtwaist Factory fire in New York City
The American Society of Safety Professionals (ASSP) is seeking a diverse group of occupational safety and health professionals to join